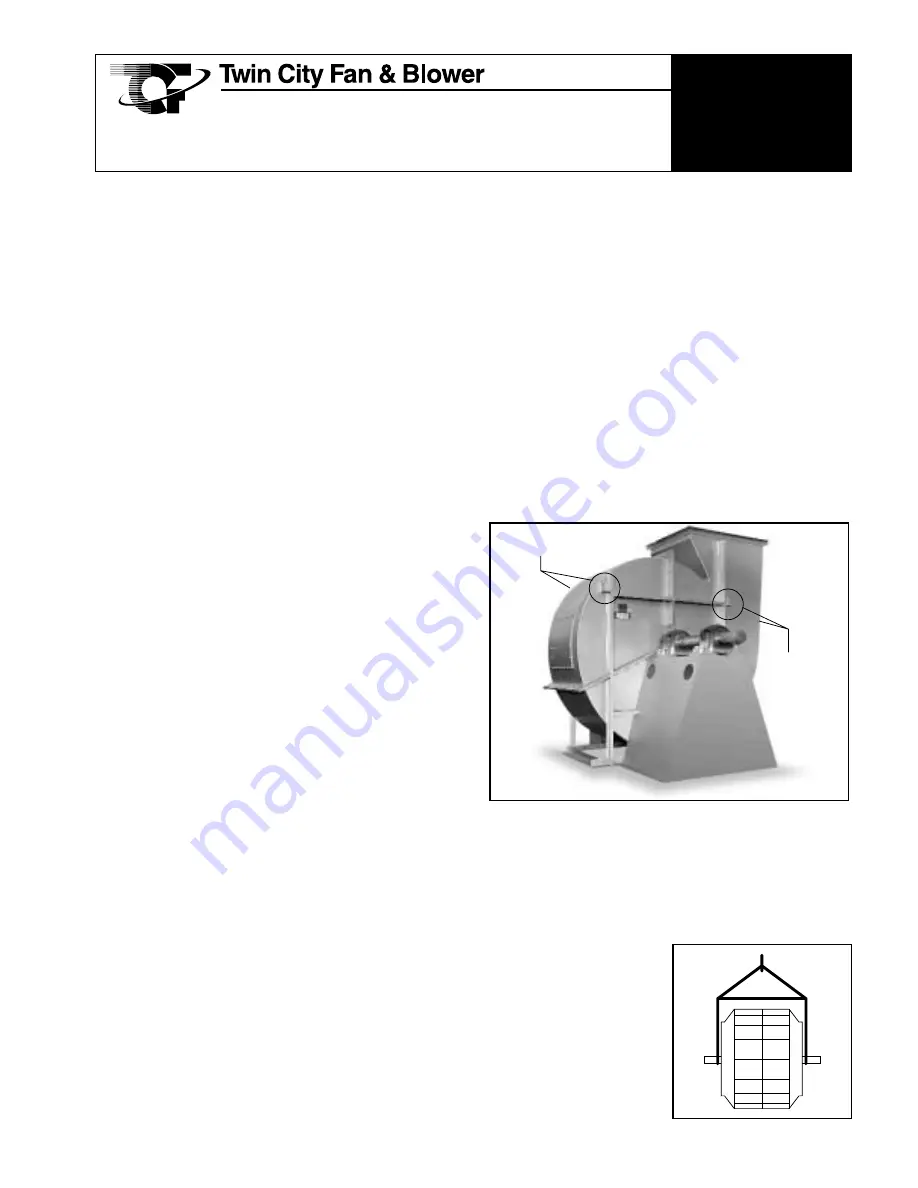
Contents
Introduction . . . . . . . . . . . . . . . . . . . . . . . . . . . . . . . . . . . 1
Shipping and Receiving . . . . . . . . . . . . . . . . . . . . . . . . . . 1
Handling . . . . . . . . . . . . . . . . . . . . . . . . . . . . . . . . . . . . . 1
Short Term Storage . . . . . . . . . . . . . . . . . . . . . . . . . . . . . 2
Long Term Storage. . . . . . . . . . . . . . . . . . . . . . . . . . . . . . 2
Foundations and Supporting Structures . . . . . . . . . . . . . . 2
Fan Installation
Factory Assembled Units. . . . . . . . . . . . . . . . . . . . . . . 2
Disassembled Units. . . . . . . . . . . . . . . . . . . . . . . . . . . 2
Fan Operation – Safety . . . . . . . . . . . . . . . . . . . . . . . . . . 3
Operation Checklist . . . . . . . . . . . . . . . . . . . . . . . . . . . . . 4
Maintenance of Fans . . . . . . . . . . . . . . . . . . . . . . . . . . . . 4
General Motor Maintenance . . . . . . . . . . . . . . . . . . . . 4
Drive Maintenance. . . . . . . . . . . . . . . . . . . . . . . . . . . . 5
Bearing Maintenance. . . . . . . . . . . . . . . . . . . . . . . . . . 5
Lubrication . . . . . . . . . . . . . . . . . . . . . . . . . . . . . . . . . 5
Wheel and Shaft Maintenance . . . . . . . . . . . . . . . . . . . 6
Structural Maintenance . . . . . . . . . . . . . . . . . . . . . . . . 6
Troubleshooting Guidelines . . . . . . . . . . . . . . . . . . . . . . . 6
Troubleshooting Performance Problems
Air Capacity Problems . . . . . . . . . . . . . . . . . . . . . . . . . 6
Noise Problems . . . . . . . . . . . . . . . . . . . . . . . . . . . . . . 6
Vibration Problems . . . . . . . . . . . . . . . . . . . . . . . . . . . 7
Motor Problems. . . . . . . . . . . . . . . . . . . . . . . . . . . . . . 7
Drive Problems . . . . . . . . . . . . . . . . . . . . . . . . . . . . . . 7
Bearing Problems . . . . . . . . . . . . . . . . . . . . . . . . . . . . 7
Limitation of Warranties and Claims . . . . . . . . . . . . . . . . . 8
Introduction
The purpose of this manual is to provide instructions that
complement good general practices when installing or oper-
ating fans manufactured by Twin City Fan & Blower. It is the
responsibility of the purchaser to provide qualified person-
nel experienced in the installation, operation, and mainte-
nance of air moving equipment.
Instructions given in the body of this manual are general
in nature and apply to a variety of models manufactured by
Twin City Fan & Blower. Most units can be installed and
maintained with the instructions given.
Special applications may require additional information.
These instructions are supplied in the form of attached
appendices. Use the instructions in the appendix if the direc-
tions in this manual differ from instructions in the appendix.
As always, follow good safety practices when installing,
maintaining and operating your air moving equipment. A
variety of safety devices is available. It is the user’s respon-
sibility to determine adequate safety measures and to obtain
the required safety equipment.
Shipping and Receiving
All Twin City Fan & Blower products are carefully construct-
ed and inspected before shipment to insure the highest
standards of quality and performance.
Compare all components with the bill of lading or pack-
ing list to verify that the proper unit was received.
Check each unit for any damage that may have occurred
in transit. Any damage should be reported immediately to
the carrier and the necessary damage report filed.
Handling
Handling of all air moving equipment should be conducted
by trained personnel and be consistent with safe handling
practices. Verify the lift capacity and operating condition of
handling equipment. Maintain handling equipment to avoid
serious personal injury.
Units shipped completely assembled may be lifted with
slings and spreader bars. Use well-padded chains, cables
or nylon straps. On most units, lifting lugs are provided for
attaching chains (see Figure 1). Lift the fan in a fashion that
protects the fan and fan coating from damage. Never lift a
fan by the inlet or discharge flange, shafting or drives, wheel
or impeller, motor or motor base, or in any other manner that
may bend or distort parts.
Partial or disassembled units require special handling. All
parts should be handled in a fashion which protects the
coatings and parts from damage. Components should be
handled such that forces are not concentrated and bending
or distortion cannot occur.
Housings should be lifted using straps and spreaders. Do
not distort housing or side plates when lifting.
Bearing pedestals should be lifted using straps or
padded chains. Under no circumstances should an
attached or separated bearing pedestal be lifted by the
shaft, bearings, drives, motor
or wheel.
The shaft and wheel
assembly may be lifted
using a hoist and a spreader
with a sling around the shaft
at points nearest the wheel
(see Figure 2). Take care not
to scratch the shaft where
the wheel or bearings will be
mounted. Never lift or sup-
port the assembly by the
wheel. Always support the
assembly by the shaft when
lifting or storing. Do not sup-
Figure 1. Lifting Lug Locations
Figure 2. Moving Shaft and
Wheel with Spreader Bar
Lifting Lugs
Lifting Lugs
INSTALLATION, OPERATION & MAINTENANCE MANUAL
Centrifugal Fans
ENGINEERING SUPPLEMENT
ES-52
Issue Date: 1-1-94
Rev. Date: 1-24-01