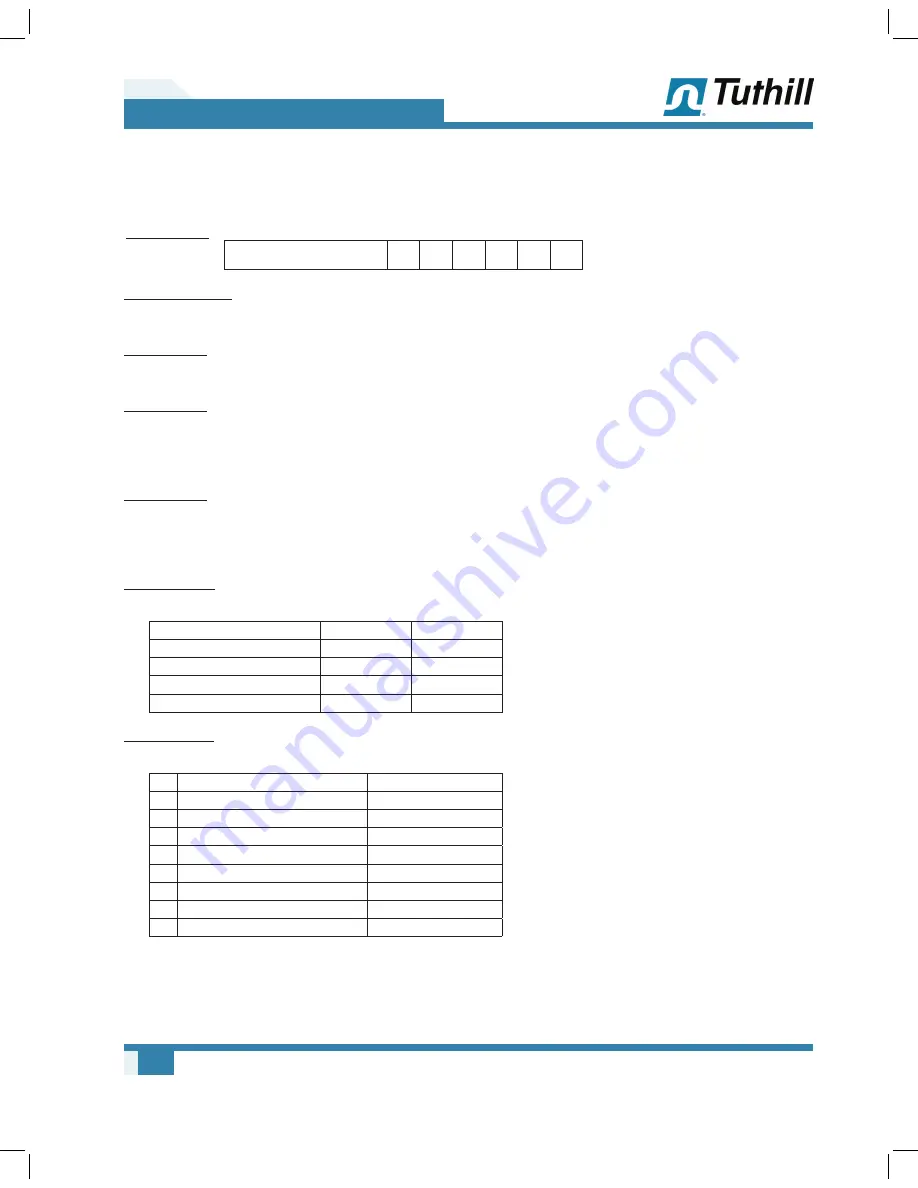
34
09
Troubleshooting
Manual 1843 Rev B p/n 001843 0000
KT SERIES PART NUMBER DESIGNATIONS
EXAMPLE: MODEL KT300D-M4A0
POSITION #:
1
2
3
4
5
6
7
8
9
10
11
K
T
3
0
0
D
–
M
4
A
0
POSITIONS 1–5:
PUMP MODEL NUMBER
POSITION 6:
PUMP REVISION LEVEL
POSITION 8:
SCOPE OF SUPPLY
L
= Pump Complete Less Motor
M = Pump Complete
POSITION 9:
ENCLOSURE RATING
4 =
NEMA 4
7 =
NEMA 7
POSITION 10:
POWER SUPPLY OPTIONS
VOLTAGE
TEFC
XP
3/60/200
9
G
3/60/230-460
A
H
3/50/190-380
D
L
3/60/575
E
M
POSITION 11:
SERVICE OPTIONS
0
Standard Construction
Viton
2
Phosphate (TAP)
Viton
3
Refrigeration (POE)
Buna
4
Mineral Oil
Buna
5 Hardened Internals (QPQ)
6
Brake Fluid (UCON)
EPR/EPDM
7
Ammonia Service (POE)
EPR; no Cu/Bronze
8 Customer Supplied Oil (O2)
9 Radiator Filled
Buna