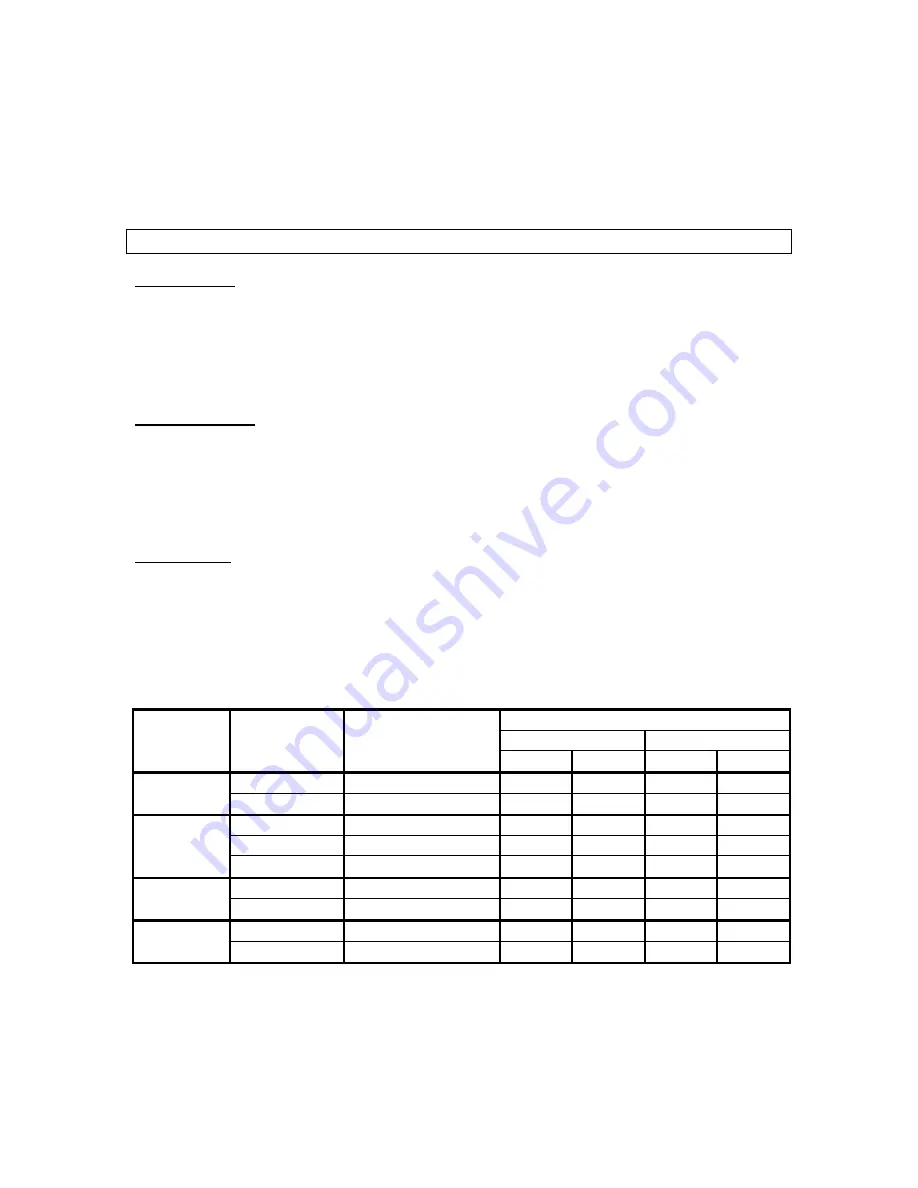
Service Manual 73
Page 7 of 32
Do not over-tighten. Packing is designed to keep leakage to a slight weep. Normally 2-3 drops
per minute is acceptable.
If excessive leakage persists after complete adjustment, consider re-packing the stuffing box or
using another packing type.
Lubrication Requirements
Outer Bearing
The standard outer bearings are maintenance-free. They are greased and sealed by the
manufacturer.
Optional high temperature outer bearings must be re-lubricated at least every 250 hours or 30
days.
Bracket Bushing
Bracket bushings that do not have grease fittings are fully lubricated by the pumped fluid and are
maintenance-free.
Bracket bushings that are provided with grease fittings must be re-lubricated at least every 500
hours or 60 days.
Idler Bushing
Idler bushings that are used with standard solid idler pins are fully lubricated by the pumped fluid
and are maintenance-free.
Idler bushings that are used with optional greasable idler pins must be re-lubricated at least every
500 hours or 60 days.
Recommended Lubricants
Recommended Temperature Range
Minimum
Maximum
Description Manufacturer
Grade
Deg. F
Deg. C
Deg. F
Deg. C
Lubriplate
1200-2
-25
-32
350
177
standard
grease
Mobil
Mobilith AW 2
-25
-32
350
177
Lubriplate
HIGH-TEMP
40
4
500
260
Lubriplate
930-AA
0
-18
400
204
high
temperature
grease
Mobil
Mobilith SHC PM
0
-18
450
232
Lubriplate
MAG-1
-60
-51
200
93
low temp.
grease
Mobil
Mobiltemp SHC 32
-60
-51
200
93
Lubriplate
FGL-2
10
-12
350
177
food grade
grease
Mobil
Mobilgrease FM 102
10
-12
350
177
NOTE:
This lubrication data is only intended as a guide. Some applications may have different
lubrication requirements, depending on actual conditions.
Table 2 – Recommended Lubricants