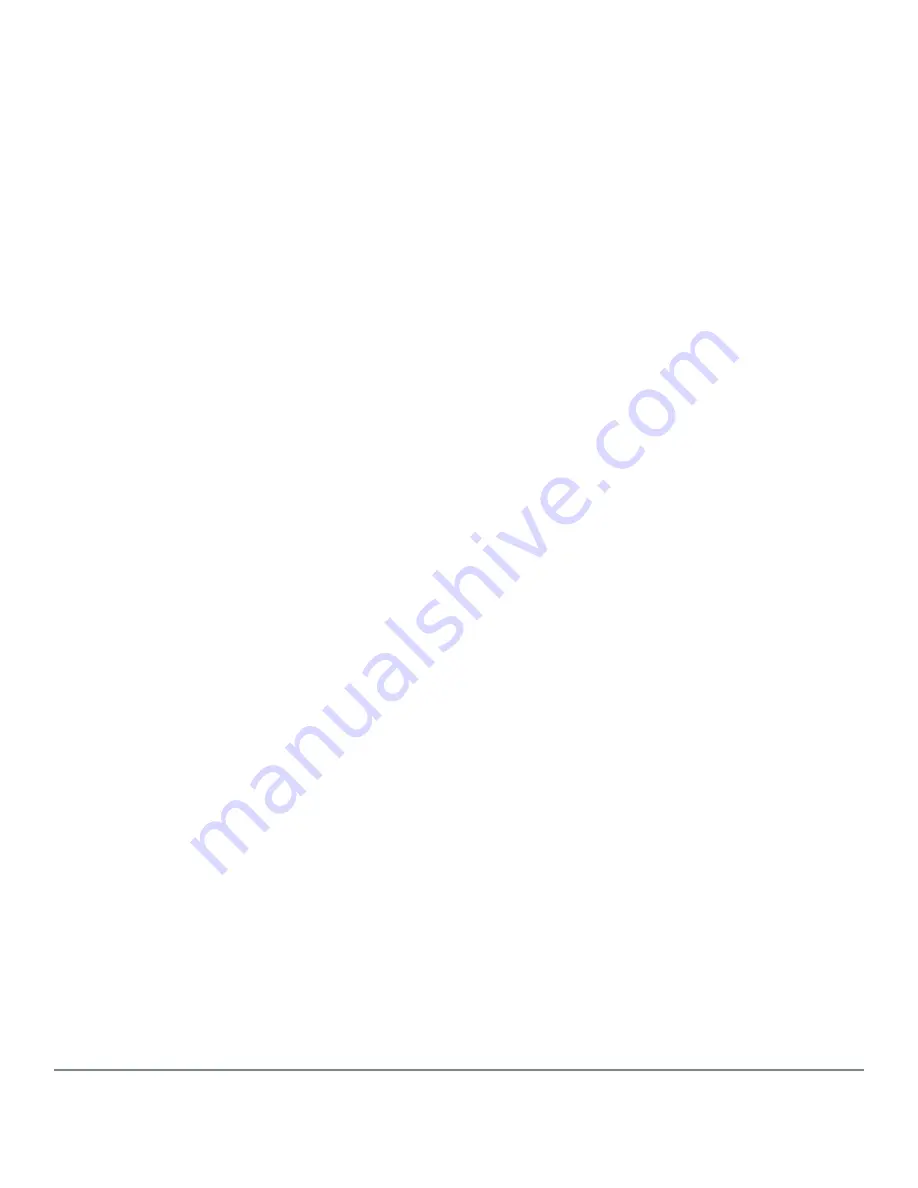
Tuthill Pump Group
12500 S. Pulaski Road, Alsip, IL 60803
www.tuthillpump.com
Excellence at work. Excellence in life.
3.
Pump Works Spasmodically
• Leaky suction lines
• Suction lift too high
• Air or vapour in liquid
• Coupling slipping on pump shaft.
4.
Pump Wastes Power
• Pressure too high
• Liquid more viscous than desired
• Suction or discharge lines obstructed
• Mechanical defects (End thrust on pump shaft)
• Drive shaft and pump shaft misaligned
•
The pump may be binding due to insufficient end clearance
• Pump shaft bent
• Misalignment within pump due to bad piping or poor installation, causing strains or distortion
Note:
Tuthill pumps are not designed to take end thrust toward the pump cover and care must be taken to prevent thrust in this
direction.
5.
Pump is Noisy
• Machine or part of it is acting as a sounding board
• Misalignment or bad design of coupling
• Coupling set too close to pump
• Vibration of pump because of bent shaft or worn parts
• Air leaks on suction side of pump
• Suction lift too high, causing vaporization.
6.
Pump Leaks
• Cover bolts need tightening, or cover gasket is defective
• Seal is defective or worn
Material Returns
If it becomes necessary to return a pump to the factory, a Return Goods Authorization (RGA) must be obtained from either your local
Authorized Distributor or our plant. No RGA can be issued until a completed Material Safety Data Sheet (MSDS) has been forwarded to
our plant and return of the pump approved.
• Tuthill pumps are precision built and must be handled with care
•
Pumps must be drained of all fluid and the ports plugged to prevent foreign material from getting into the pump
• Pumps must be packaged securely to prevent damage while in transit