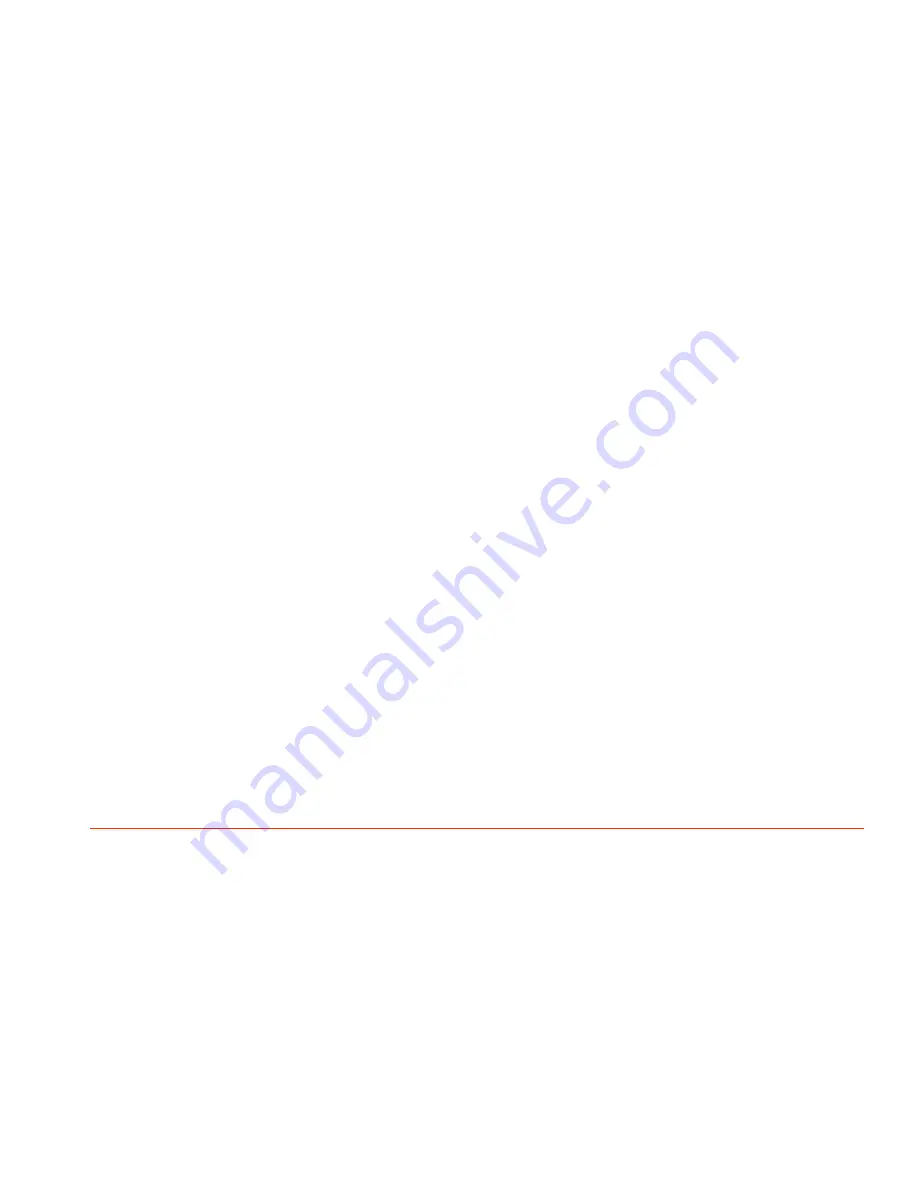
Page 4 of 9
Proper Installation
A large percentage of unsatisfactory pump installations is caused by failure to observe the natural laws limiting the suction lifts on
volatile materials. At temperatures of approximately 70°F or lower, kerosene and light fuel oils may be pumped at nearly full volumetric
efficiency when combined vertical lift and friction in the suction line do not cause a vacuum to exceed 10 inches of mercury at the
suction port of the pump. Ten inches vacuum on kerosene oil is equal to approximately fourteen feet of vertical lift without pipe friction.
This varies with the temperature and various oils, but if, in laying out the suction line, the maximum vacuum is kept at this figure or
lower, good results may be expected. If this vacuum is exceeded, it is almost certain to result in cavitation, loss of volume and a noisy
installation.
When pipelines are installed, an inverted “U” bend should be incorporated in the suction line close to the pump to trap liquid in the
pump for priming. The suction line must be kept free from air leaks and air pockets.
When handling liquids of high viscosity, such as asphalt, heavy gear lubricants, linseed oil, Bunker “C” fuel oil, molasses, etc., the speed
of the pumps and the running clearances are important. Consult Tuthill UK, whenever unusual conditions of speed, pressure, vacuum
or viscosity are encounted.
Before initial start of the pump, it is recommended that some of the liquid to be pumped be introduced into the pump ports to insure
wetting of the rotation elements. Check alignment and rotation of the driver to see that pump will rotate in the designated proper
direction of rotation.
Filter Protection
Piping or tubing should be cleaned out thoroughly to remove chips and pipe scale before connecting the piping to the pump. Neglect
of this precaution may result in damage to the pump when it is put in operation. The suction piping should be as short and direct as
possible. Grit, pipe chips, or other foreign substance that is allowed to pass through the, pump, will almost surely injure and possibly
ruin it. Always remember the following in the selection and position of a filter.
•
A filter should be installed to protect the pump whenever conditions permit
•
When uncertain of pressure drop through the filter, obtain this data from manufacturer, giving pump capacity and type of
liquid to be handled
•
Install filter according to arrows or notation designating flow
•
Have filter accessible for servicing
• Use duplex type where shutdown during servicing is not permitted
•
Provide a vacuum gauge in the suction line for determining when the filter requires cleaning
•
The greater the free opening, the less attention the filter will require
WARNING
All Tuthill pumps contain resigal ISO 32 lube oil form the factory production test. Determine if this is compatible with the fluid you are
pumping. If the fluid is incompatible please consult factory directly. If the pump is to operate at elevated temperatures, it should be
brought up to operating temperature gradually. Rapid or sudden introduction of liquid at an elevated temperature into the cold liquid
chamber of the pump could cause damage to the seal or other internal parts. Do not run the pump dry. This could cause severe damage
to the seal, bushings, and/or metal parts. Temperatures must not exceed 200°C without prior consent