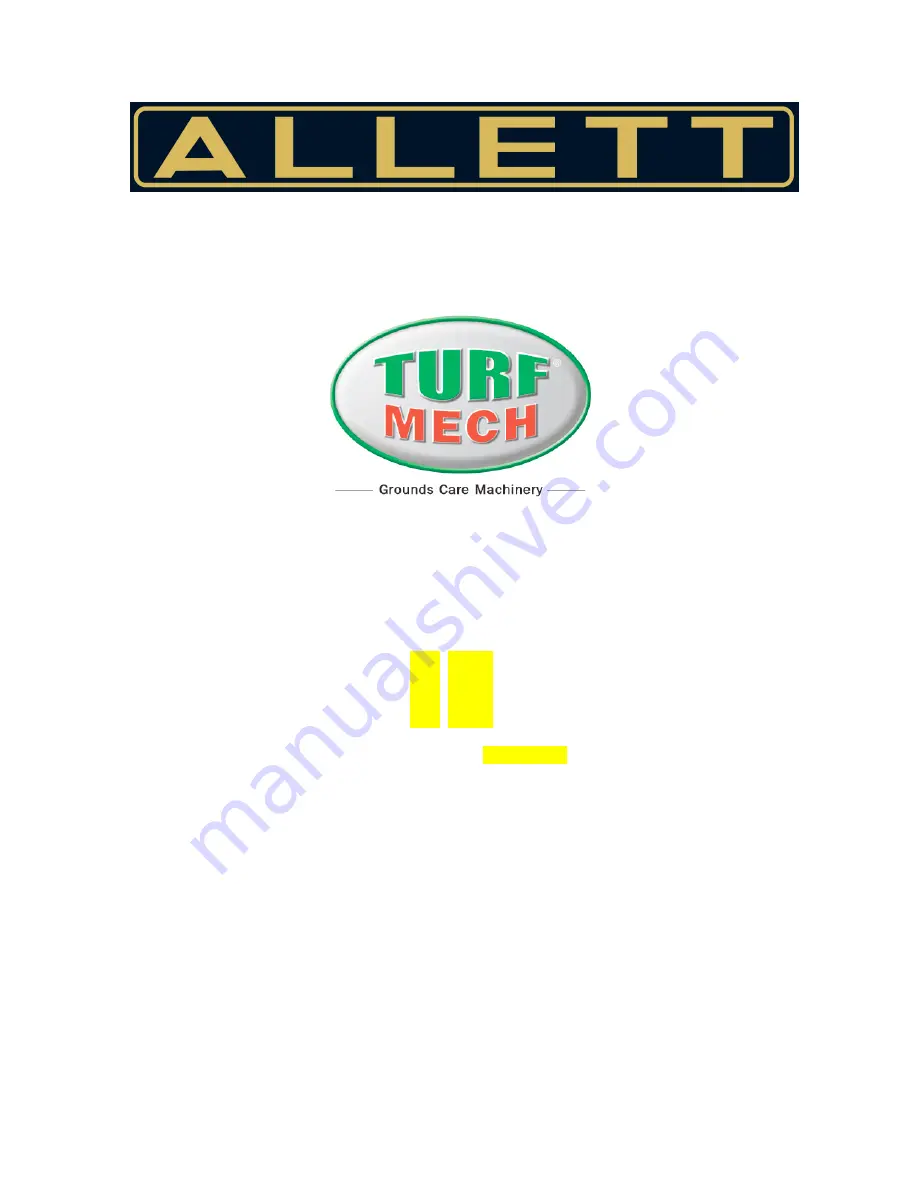
A member of the Turfmech group
Buffalo 20, 24 & 27”
OPERATOR & PARTS MANUAL
For Serial number:
BU20/4-XX-XXX onwards
BU24/4-XX-XXX onwards
BU27/4-XX-XXX onwards
(AM81589 Issue B March 2013)
English version
Turfmech Machinery Limited
Hangar 5, New Road, Hixon, Stafford, ST18 0PJ, United Kingdom
Tel: +44 (0) 1889 271503
Fax: +44 (0) 1889 271321
www.turfmech.co.uk
For Allett spare parts
Tel: +44 (0) 1889 272095
Fax: +44 (0) 1889 271321
www.allett.co.uk
Summary of Contents for Buffalo 20
Page 24: ...24 MODEL BU20 BU24 BU27 Mainframe Assembly BOM FIG 1 ...
Page 26: ...26 MODEL BU20 BU24 BU27 Rear Roller Assembly FIG 2 ...
Page 28: ...28 MODEL BU20 BU24 BU27 Front Roller Assembly FIG 3 ...
Page 30: ...30 MODEL BU20 BU24 BU27 Countershaft Assembly FIG 4 ...
Page 32: ...32 MODEL BU20 BU24 BU27 Cylinder Drive Assembly FIG 5 ...
Page 34: ...34 MODEL BU20 BU24 BU27 Rear Roller Drive Assembly FIG 6 ...
Page 36: ...36 MODEL BU20 BU24 BU27 Top Handle Assembly FIG 7 ...
Page 40: ...40 Notes ...