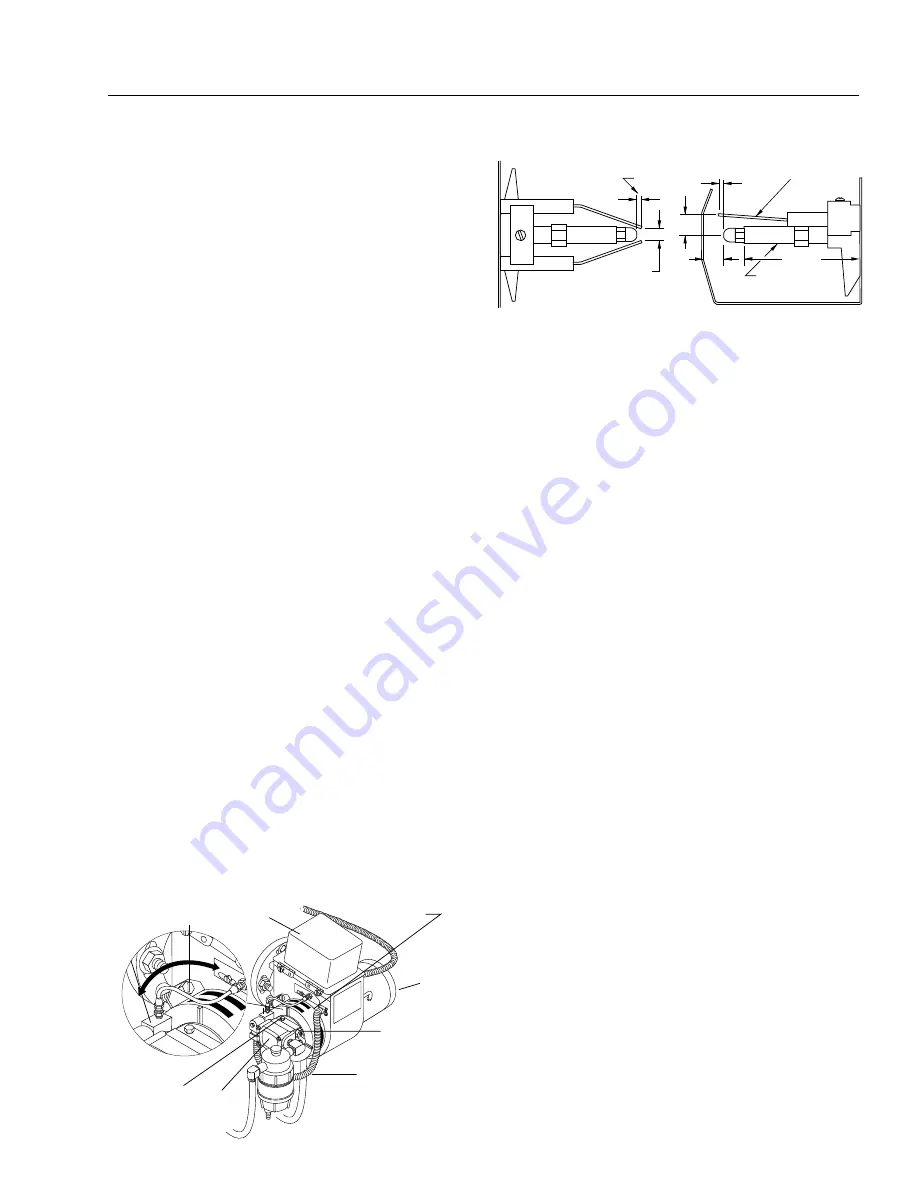
TNT SERIES PRESSURE WASHER
OPERATOR’S MANUAL
9
Rupture Disk:
If pressure from pump or thermal expansion should ex-
ceed safe limits, the rupture disk will burst allowing high
pressure to be discharged through hose to ground. When
disk ruptures it will need to be replaced.
Fuel:
Use clean fuel oil that is not contaminated with water
and debris. Replace fuel filter and drain tank every 100
hours of operation.
Use No.1 or No 2 Heating Oil (ASTM D306) only. NEVER
use gasoline in your burner fuel tank. Gasoline is more
combustible than fuel oil and could result in a serious ex-
plosion. NEVER use crankcase or waste oil in your burner.
Fuel unit malfunction could result from contamination.
Fuel Control System:
This machine utilizes a fuel solenoid valve located on the
fuel pump to control the flow of fuel to the combustion cham-
ber. The solenoid, which is normally closed, is activated by
a flow switch when water flows through it. When the opera-
tor releases the trigger on the spray gun, the flow of water
through the flow switch stops, turning off the electrical cur-
rent to the fuel solenoid.
The solenoid then closes, shutting off the supply of fuel to
the combustion chamber. Controlling the flow of fuel in this
way gives an instantaneous burn-or-no-burn situation,
thereby eliminating high and low water temperatures and
the combustion smoke normally associated with machines
incorporating a spray gun. Periodic inspection, to insure
that the fuel solenoid valve functions properly, is recom-
mended. This can be done by operating the machine and
checking to see that the burner is not firing when the spray
gun is in the OFF position.
Fuel Pressure Adjustment:
To control water temperature, adjust fuel pressure by turn-
ing the regulating pressure adjusting screw clockwise to
increase, counterclockwise to decrease. Do not exceed
200 psi. NOTE: When changing fuel pump, a bypass plug
must be installed in return port or fuel pump will not prime.
DC Electrodes Setting
Burner Nozzle:
Keep the tip free of surface deposits by wiping it with a
clean, solvent saturated cloth, being careful not to plug
or enlarge the nozzle. For maximum efficiency, replace
the nozzle each season.
Air Adjustment:
Machines are preset and performance tested at the fac-
tory - elevation 100'. A one-time initial correction for your
location will pay off in economy, performance, and ex-
tended service life. If a smoky or eye-burning exhaust is
being emitted from the stack, two things should be
checked. First, check the fuel to be certain that kero-
sene or No. 1 home heating fuel is being used. Next,
check the air adjustment on the burner.
Coil Removal:
Removal of coil because of freeze breakage, or to clean
soot from it can be done quickly and easily.
1. Disconnect hose from pump to inlet side of the coil.
2. Carefully disconnect the thermostat sensor making
sure you do not crimp the capillary tube.
3. Remove burner assembly from combustion chamber.
4. Remove the 3-3/8 bolts from each side of coil and
tank assembly (these bolts are used to fasten tank
to chassis).
5. Remove fittings connected to the 1/2" pipe nipples
from inlet and discharge sides of coil.
6. Remove top tank wrap, bend back insulation tabs
and fold back blanket.
7. Remove bolts that hold down coil to bottom wrap.
8. Remove coil.
9. Replace or repair any insulation found to be torn or
broken.
10. Remove insulation retainer plates.
Coil Reinstallation:
Reinstall new or cleaned coil reversing Steps 9 through 1.
Gap
1/8"
1/8"
3/8"
1/2"
3/16"
Top View
Side View
Nozzle
Adapter
2-7/8"
Periodically Check Wiring Connections. If Necessary
To Adjust Electrodes, Use Diagram.
Air
Adjustment
Screw
#7-0009
Fuel
Pump
#7-3753895
Cord Set
Adjusting
Screw
Pressure
Gauge
Port
Air Band
Motor
#7-0005
Transformer
#7-20358
Electrodes
Summary of Contents for TNT-503021E
Page 4: ...4 TNT SERIES PRESSUREWASHER OPERATOR S MANUAL COMPONENT IDENTIFICATION ...
Page 10: ...10 TNT SERIES PRESSUREWASHER OPERATOR S MANUAL EXPLODED VIEW LEFT SIDE ...
Page 11: ...TNT SERIES PRESSUREWASHER OPERATOR S MANUAL 11 EXPLODED VIEW RIGHT SIDE ...
Page 16: ...16 TNT SERIES PRESSUREWASHER OPERATOR S MANUAL TNT CONTROL PANEL EXPLODED VIEW ...