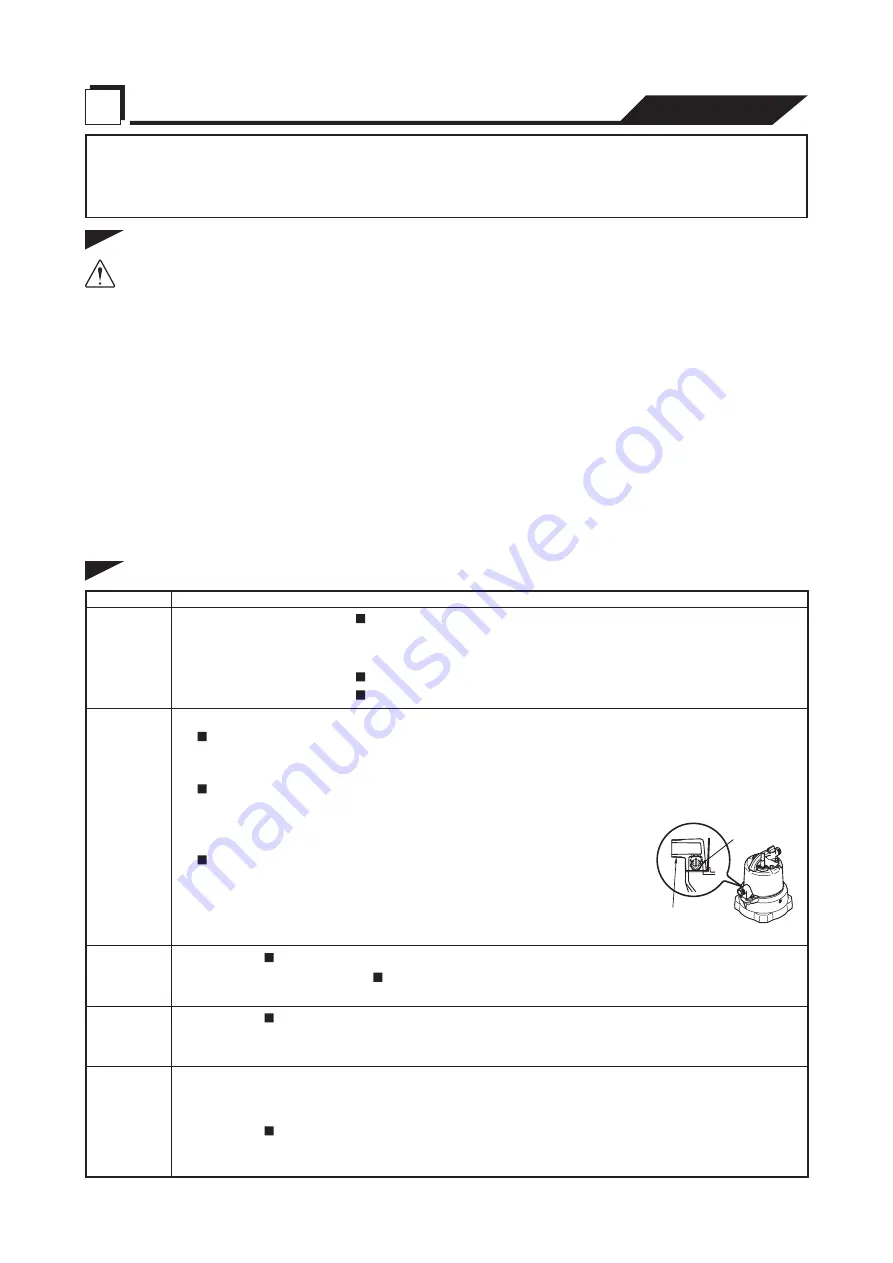
-11-
Regular maintenance and inspections are a necessity for continued efficient functioning
of the pump. If any abnormal conditions are noticed, refer to the section on troubleshoot-
ing (P.15) and take corrective measures immediately. It is recommended that a spare
pump be kept ready in case of any problems.
Prior to Inspecting
WARNING
Detach the cabtyre cable from the receptacle or terminals, after making
certain the power supply (circuit breaker, etc.) is turned off. Failure to follow
this precaution may result in a serious accident from electrical shock or
unexpected starting of the pump motor.
(1) Washing the Pump
Remove accumulated matter from the surface of the pump and wash it with clean water.
Take special care to remove any debris from the impeller.
(2) Inspecting the Pump Exterior
Look for any peeling or chipped paint, and make sure the nuts and bolts are fastened
tightly. Any cracks in the surface should be repaired by cleaning that area, drying it
and then applying a touchup coating.
Note:
Touchup is not supplied. Note that some kinds of damage or looseness may require that
the unit be disassembled for repairs. Please consult with your nearest dealer or Tsurumi
representative.
Regular Inspection
Frequency
Monthly
Annually
Semi-annually
Weekly
Inspection Items
Every
2 to 5 years
Measure insulation resistance
Measure operating current.
NOTE:
If the insulation resistance has become notable lower than the previous inspection, an
inspection of the motor will be necessary.
Pump Inspection.
NOTE:
In some case a siphon effect when the pump stops can
cause water to reverse its flow or the priming water to flow out.
NOTE:
See below on OIL inspection and oil change.
Changing oil.
NOTE:
Specialized know-how is required for inspecting and replacing the mechanical seal.
Consult with your nearest dealer or Tsurumi representative.
Overhaul
NOTE:
Consult with your nearest dealer or Tsurumi representative regarding overhauls.
Swing check valve inspection (LSC).
Check valve inspection (LSP).
Change mechanical seal.
Measure supply voltage
Inlet
Check Valve
LSP
Reference insulation resistance = 1MΩ minimum
Oil inspection. Every 1,000 hours of operation or six months, whichever comes first.
Every 2,000 hours of operation or 12 months, whichever comes first.
Designated oil: Turbine Oil ISO VG32. Oil Quantity: 155ml (LSC) ; 150ml (LSP)
Compare with rated current
Power supply voltage variation ( within ±10% of the rated voltage)
A noticeable drop in performance may indicate wear in the impeller, suction cover, etc., or else clogging
of the impeller, etc. Remove the clogged debris, and replace any worn parts.
If the lip on the bottom plate becomes excessively rounded off, or it the rubber material of the swing
check valve is deteriorated, shutoff function of the valve decrease. Replace the bottom plate and/or the
swing check valve.
The check valve may fail to operate if sand or debris at attached to it.
Wash the valve and inside the inlet at regular intervals. The check valve can
be removed by removing the inlet hex.bolt.
This should be carried out even if there are no problems with the pump. The frequency
depends on how continuously the pump is in use.
Inspection of lifting rope or chain Replace if damage, corrosion, or wear has occurred to the rope or
the chain. Remove if foreign object is attaching to it.
7 MAINTENANCE AND INSPECTION