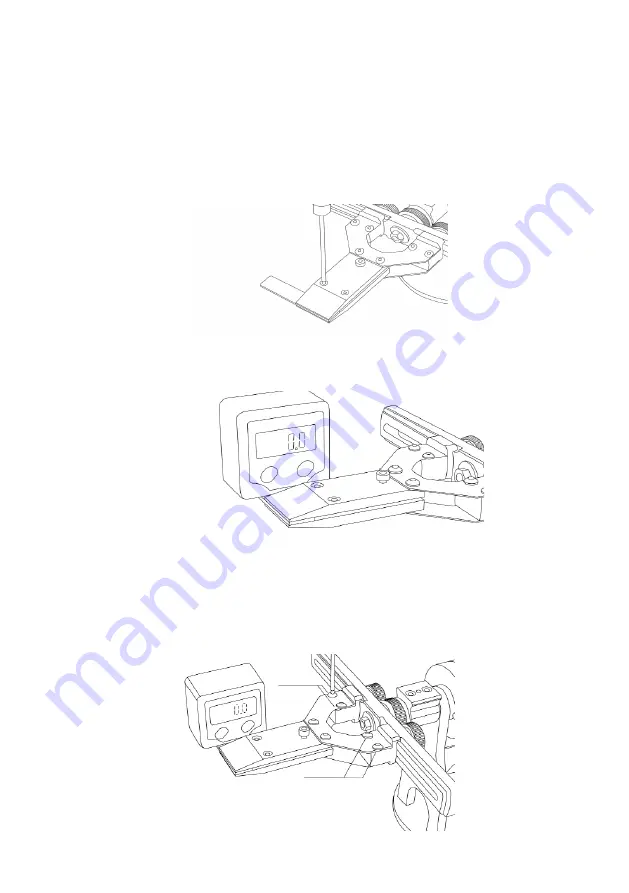
Adjusting the angles symmetry while turning the clamp
Calibration is required to equalize the asymmetry of the angles while turning the clamp
which may appear during transportation, as well as during long term use. Digital protractor is
required for the calibration. The device should be firmly fixed on a flat surface.
1.
Set the calibration plate (14D) from the spare parts packet in the clamp. Jaws should
remain parallel.
2. Place the protractor on the plate along the axis of rotation of the clamp and reset.
3. Turn the frame with clamp and make measurements. If the value is more than 0.3 °, loosen
screws (1) and with arms adjust the angle of value equal to the previously measured 1/2
difference. Holding this value, tighten the screws.
(1)
(1)
17