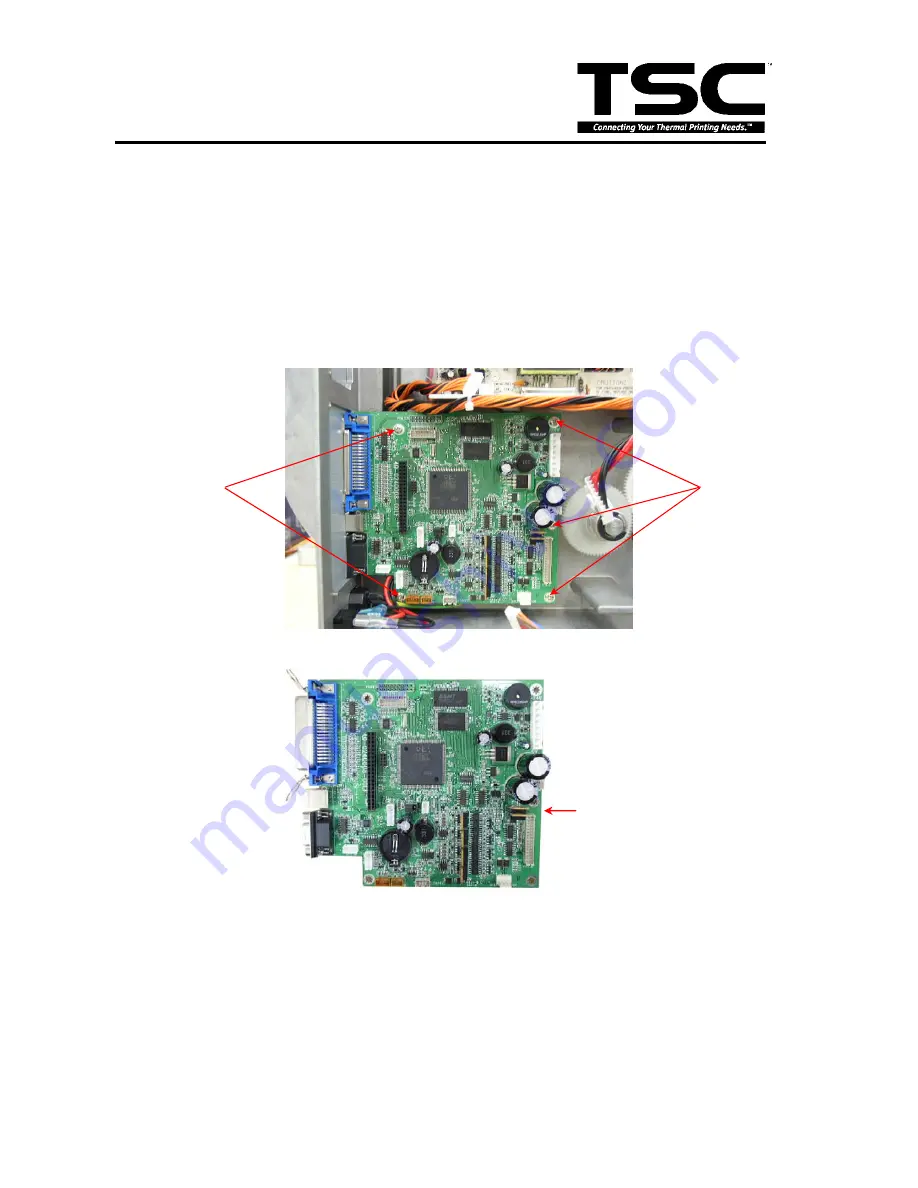
18
18
TTP-2410M/346M/644M
TTP-246M Plus/344M Plus
Bar Code Printer Service Manua
l
3.5 Replacing the Main Board
1. Refer to section 3.1 to remove the electronics cover.
(Refer to section 3.4 to remove the multi-interface board.)
2. Disconnect all connectors from the main board.
3. Remove 5 screws from the main board.
(Remove 2 copper pillars and 3 screws.)
4. Remove/Replace the main board.
5. Reassemble the parts in the reverse procedures.
Screws or
copper pillars
Screws
Main board