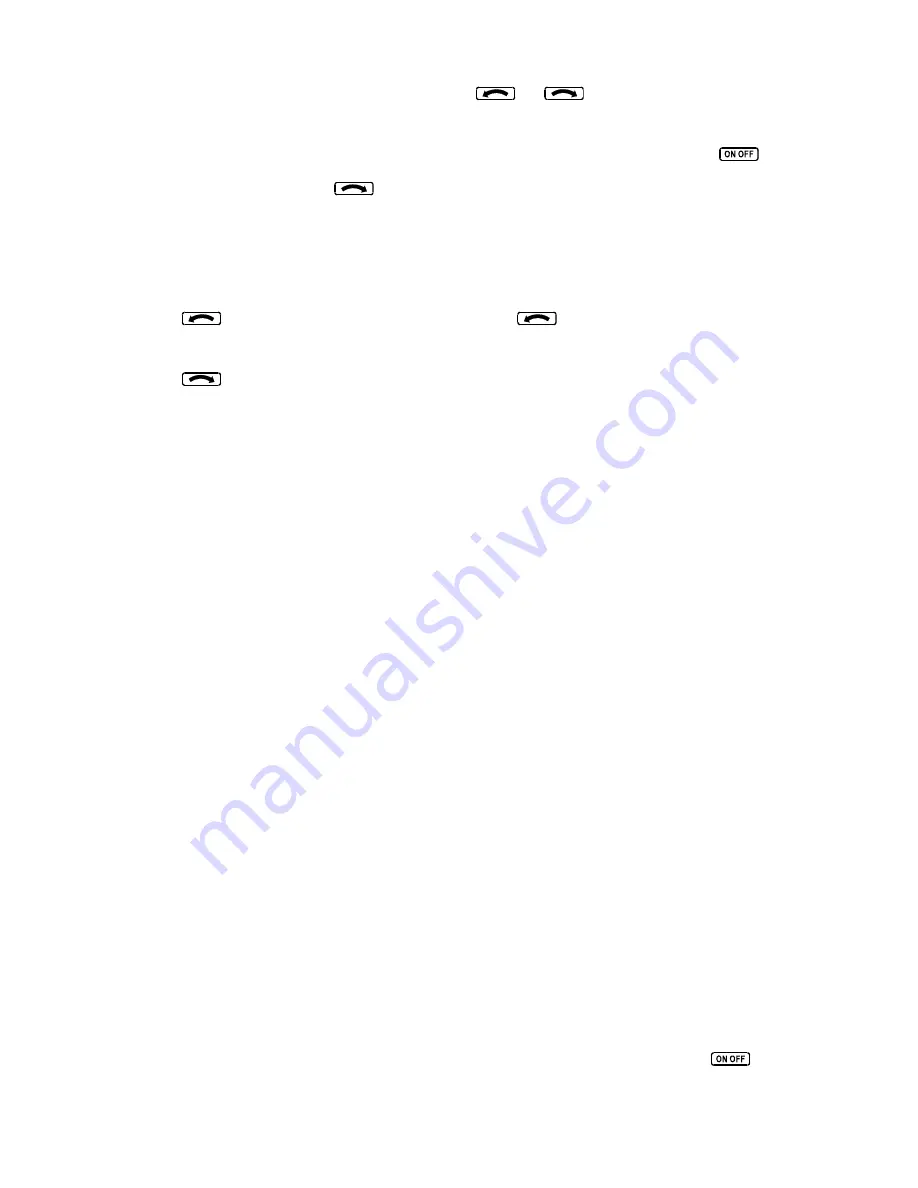
While the autopilot is in its disengaged (off) mode, press and hold
and
simultaneously. The display will now
show “–| – |–” with the center dash character blinking, indicating the Manual Gyro Set operation. Continue to hold both
buttons in for a few seconds while the autopilot is not being moved about, to re-center the gyro manually
The next step in the check-out procedure is to verify that the servo runs, and in the correct direction. Press
to again
engage the autopilot. The servo should be responding at this time, moving the controls only very slowly in attempt to hold
magnetic heading constant. Press and hold
for about 1-1/2 seconds. The autopilot will now move the controls in an
attempt to cause a constant-rate turn towards the right. If servo direction is not correct, the wires going to pins 4 and 5 of the
roll servo (pins 11 and 12 on the main connector) must be reversed to achieve the correct response. If the servo does not move
at all, double-check the torque setting (setup screen 2) to make sure it is at least 10. If a servo jitters but does not actually
rotate, check the wiring on the four servo drive lines to that servo for continuity and correctness. If the servo does not seem to
have any torque, check the roll torque control line for continuity and correctness. With a torque setting of 12, and the autopilot
engaged, the torque control line should measure approximately 4.9 volts DC.
Press and release
to stop the continuous turn. Then press and hold
for about 1-1/2 seconds. The autopilot will
now move the controls in attempt to cause a constant-rate turn to the left. Notice the stroboscopically-moving display
indicating the autopilot is in its constant-turn mode.
Press and release
to stop the continuous turn.
While the servo is running, check that the servo arm or capstan is properly operating the controls. For servo installations using
an arm, check that as the controls go from limit to limit the arm of the servo remains in the operating range of the servo (a
maximum of 100 degrees total rotation) and that when the controls are centered, the connecting push rod is approximately
perpendicular to the arm of the servo. For capstan systems, insure that the cabling remains at proper tension and is properly
secured as the servo moves the controls from stop to stop. Insure that the servo remains secure in its mounting and does not
flex its mounting bracket as it drives the control to its stops. For installations using an arm, insure that as the servo moves the
control towards the end of control travel it does not cause the main control’s torque tube to flex in any way that could cause
control system lockup at the extremes of servo travel. Insure that any “lost motion” in the linkages is eliminated or minimized,
in order to maximize the performance of the autopilot. Lost motion (dead zone) will result in wandering or slow “hunting”
behavior in flight. Lost motion in the linkage can best be observed by temporarily clamping the servo arm and gently moving
an aileron back and forth, while observing how much aileron movement takes place against the clamped servo.
The next step in the check-out procedure is to verify that the serial input from the GPS receiver is being properly received and
interpreted. With the aircraft outside of any building, power up the GPS receiver and the autopilot. After the GPS receiver
acquires its position, the autopilot display will change from “ – – – ” to “OFF” indicating that valid position data is available.
.If the word “OFF” is not displayed, even after it is known that the GPS unit has a position fix, the problem must be diagnosed.
Possible reasons for such a problem are,
Pin 3 on the connector is not wired to a source of RS-232 serial data
The GPS receiver’s baud rate disagrees with that selected within the autopilot
The GPS receiver’s serial output port has not been properly configured to provide the information
The remaining adjustments relate to the dynamics of flight and compensation of the magnetic backup system in the autopilot.
DigiTrak First Flight
The first flight should be done after having completed all the setup and testing on the ground. For the first flight, it is important
that the GPS unit is properly functioning with the autopilot, so that the dynamics of flight can be set without consideration of
the calibration of the magnetic backup system. As discussed earlier, when there is proper connection to the serial input of the
autopilot, the display will show “OFF” when it is disengaged and valid GPS data is present. If this does not occur, it is best to
diagnose and fix the problem prior to first flight of the autopilot.
The activity adjustment (setup screen 1) determines how briskly the autopilot responds to roll disturbances. The setting can be
adjusted, in flight, over a wide range; thus the autopilot can be tailored to adapt to any aircraft installation.
The activity adjustment covers a numeric range of 0 to 12. Unless the value for a particular aircraft is provided by TruTrak, it is
advisable to start with a setting of zero and work up from there. Most installations would ultimately require somewhat higher
settings.
On the first flight, manually fly the aircraft to a suitable area for testing. Engage the autopilot by pressing
. Observe that
the display now shows the captured GPS ground track as the selected direction of flight.
TruTrak Flight System Digitrak Installation & User Guide
6 October 2002 Printing