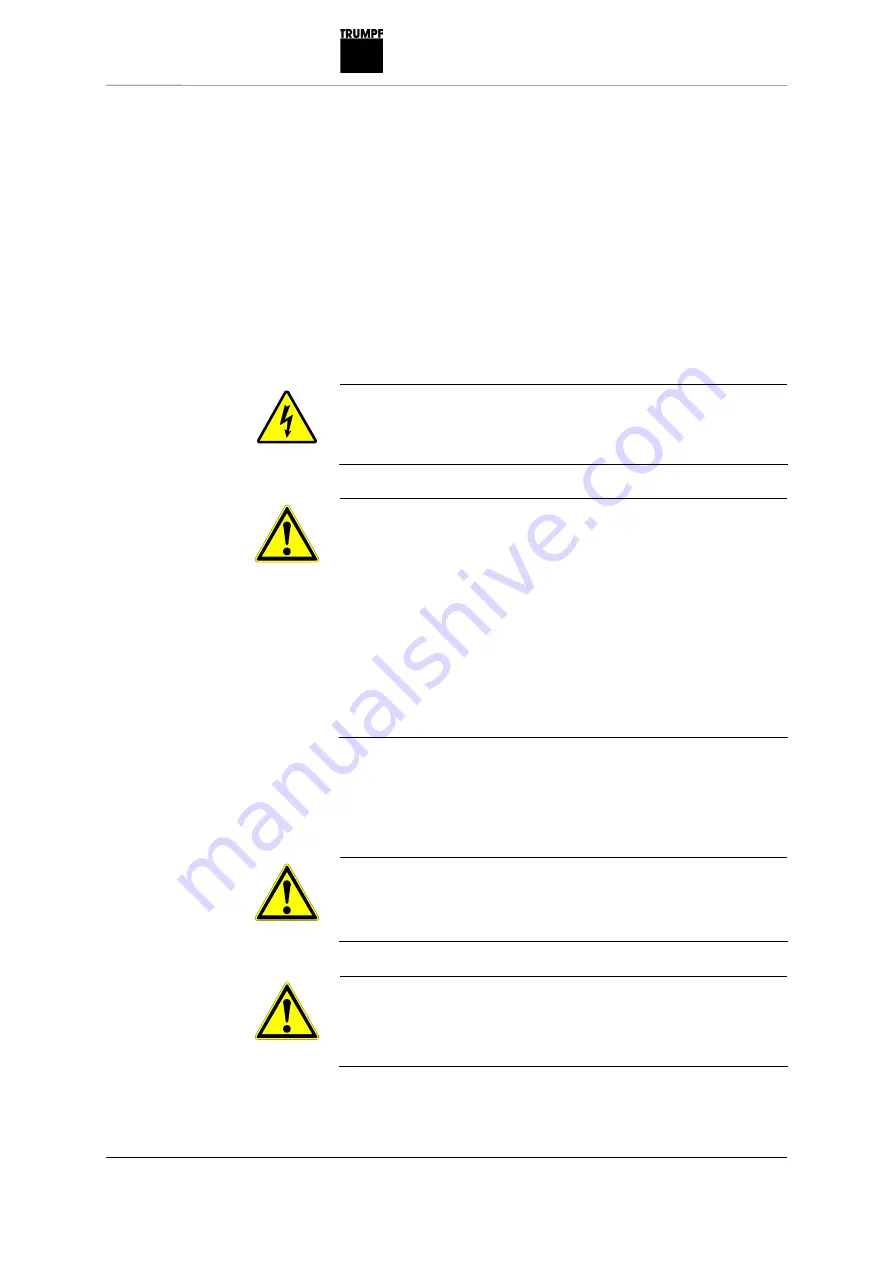
4
Safety
E609EN_01.DOC
1. Safety
1.1 General safety information
¾
Before starting-up the machine, read the operator's manual
and the safety information (order no. 0373678, red document)
in its entirety and carefully follow the instructions given.
¾
Comply with the safety regulations in accordance with
DIN VDE, CEE, AFNOR as well as any other regulations that
apply in the individual countries.
Danger
Risk of fatal injury from electric shock!
¾
When working with the machine do not touch any electrical
lines. The machine is not insulated.
Warning
Risk of injury due to improper handling!
¾
Always remove the compressed air hose from the machine
prior to maintenance work.
¾
Check the compressed air hose, connection coupling, and
machine for damage each time before using the machine.
¾
Wear safety glasses, hearing protection, protective gloves
and work shoes when working at the machine.
¾
Connect compressed air only when the machine is switched
off.
¾
Always lay the compressed air hose away from the back of
the machine.
1.2 Specific safety information
Warning
Risk of injury to hands
¾
Do not reach into the processing line with your hand.
¾
Use both hands to hold the machine.
Warning
Risk of injury from hot and sharp chips!
Hot chips and sharp chips are emitted from the chip
dumping at high speed.
¾
The use of a chip bag is recommended.
Summary of Contents for TruTool N 200
Page 1: ...Operator s manual English TruTool N 200 1A2...
Page 2: ......