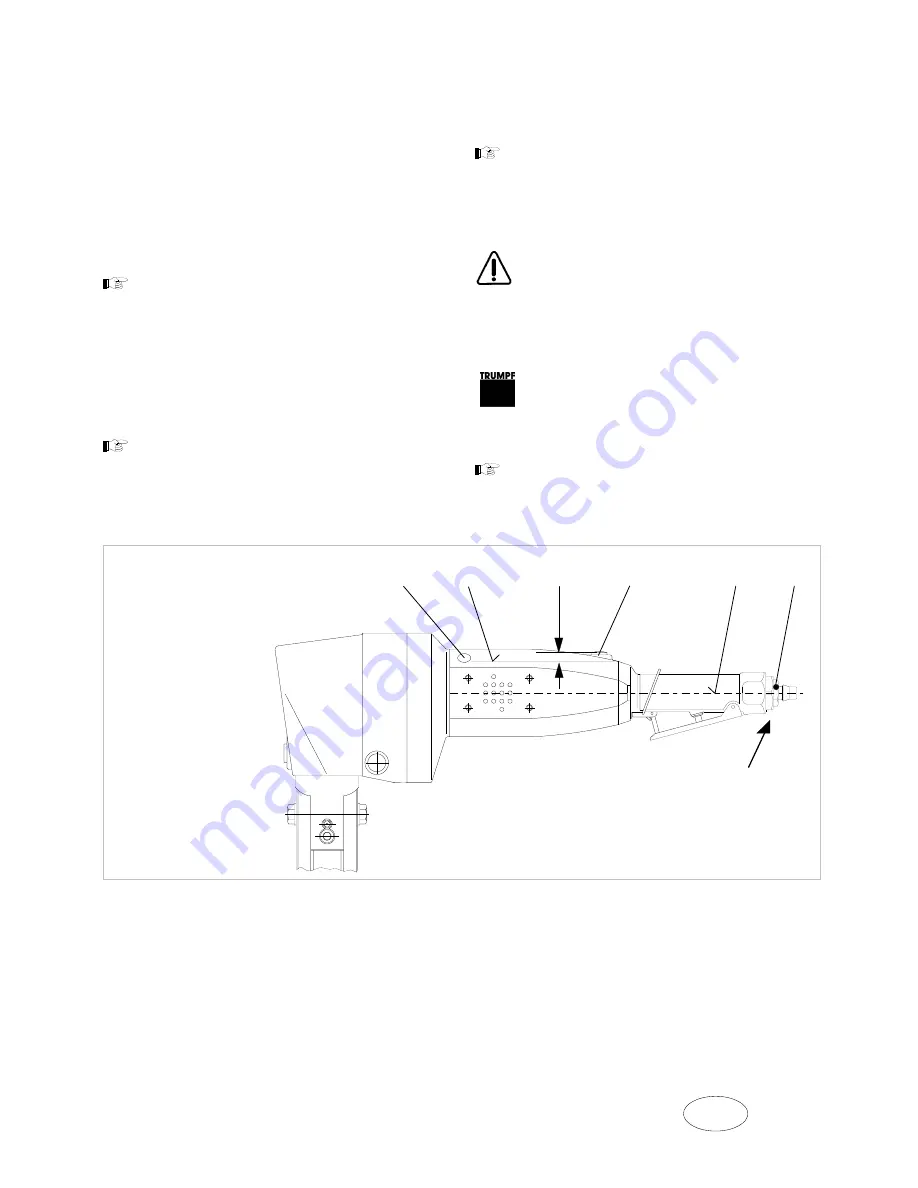
E211en1_2.doc
N700-1
GB
8
Motor bearing l u b r i c a t i o n
The ball bearing in the motor flange is to be lubricated
via the lubricating head using a grease gun.
Lubricating interval:
every 10 operating hours
Recommended
greases:
BP Energrease LS-EP 2
SHELL Alvania Grease EP 2
Cleaning
Clean the filter 355 every 10 operating hours in order
to prevent throttling or power loss.
See the spare parts list for an diagram of filter
355.
Speed limiter and ball bearing are to be lubricated
with gear grease during regular machine mainte-
nance.
Warning:
Speed limiter 324 is to be handled with
particular care, as damage can cause overspeed.
See diagram in the spare parts list.
Changing vanes
The performance of the machine decreases if the
vanes are excessively worn.
Vane replacement and all other repair work is to be
carried out by an expert!
Vane set (4) on the rotor of the compressed-
air motor. See Item 310 in the spare parts list
for corresponding diagram.
Repairs
Danger of injury
Pneumatic tools conform to the applicable
safety regulations. Repairs may only be
carried out by qualified electricians in order
to prevent unnecessary accidents.
Use only o r i g i n a l s p a r e p a r t s.
Please note the specifications on the output plate.
You will find a list of TRUMPF representatives
at the back of this operating manual.
Fig. 10776
312 Lubricating head for
motor bearing lubrication
313 Sealing screw of oil filler
neck
314 O-ring (9.2 x 1.8) under
the sealing screw
355 Filter
358 Quick-release coupling
M
center machine axle
max.Maximum oil level when
refilling oil (15 mm under
the filler neck when the
center axle is horizontal)
Note: If the oil level is
too high, oil will spill out
of the motor housing
exhaust opening
312
max.
15mm
M
358
355
313
314
Summary of Contents for N700-1
Page 1: ...Operator s manual english N 700 1...
Page 2: ......
Page 12: ...E211en1_2 doc N 700 1 GB 10...