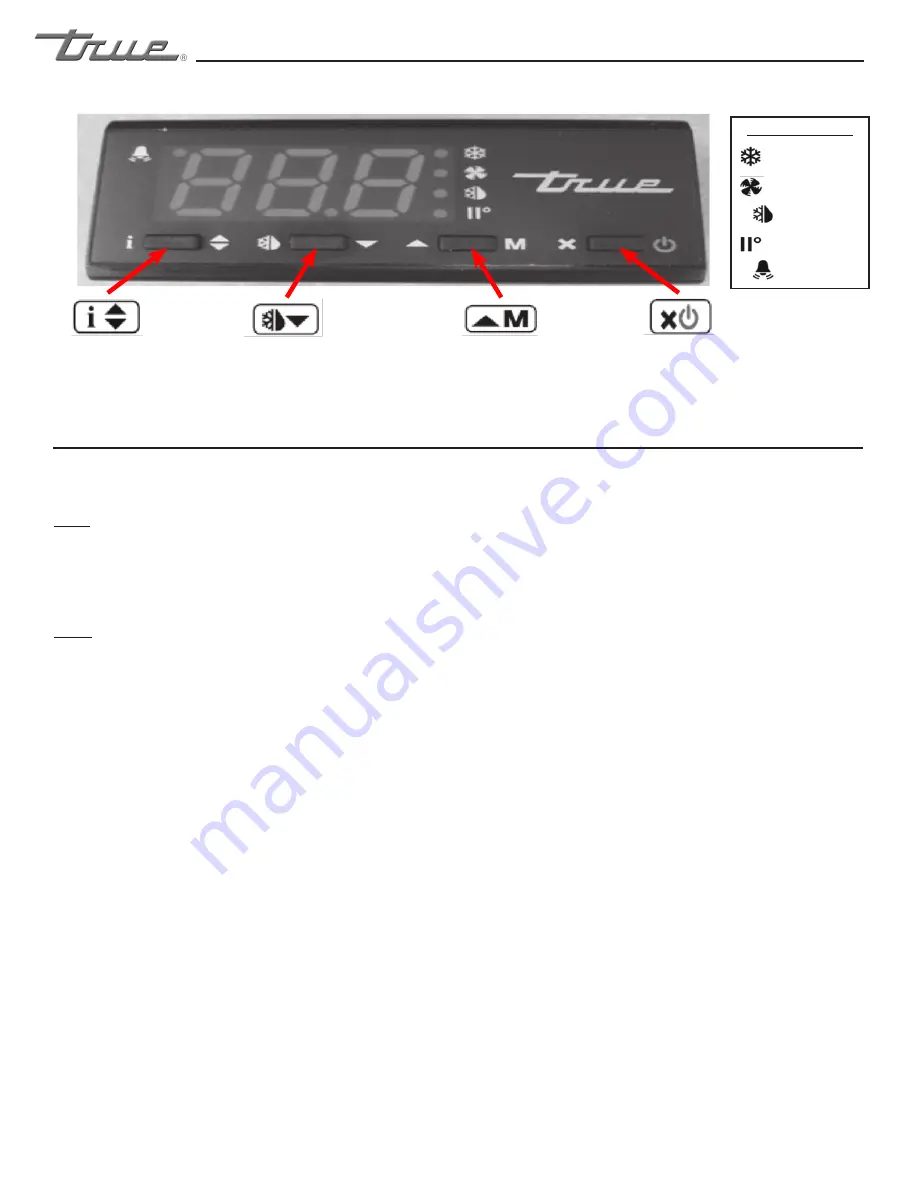
............ www.truemfg.com ............
True Food Service Equipment, Inc.
SAFETY INFORMATION
18
18
HOW TO INITIATE A MANUAL DEFROST
May need to unlock control.
WHY:
A ONE TIME ADDITIONAL DEFROST MAY BE NECESSARY
TO CLEAR ACCUMULATED FROST/ICE FROM EVAPORATOR
COIL.
HOW:
The method to initiate a manual defrost is determined by
the Defrost Mode Parameter “DTM” preprogrammed in
the controller.
A.
REGULAR TIME DEFROST (TIM)
If controller is preprogrammed for “TIM”, press and
release the Manual Defrost button until “dEF” appears.
B.
REAL TIME CLOCK (RTC)
If controller is preprogrammed for “RTC” press the and
hold the Manual Defrost button for 5 seconds until
“dh1” appears. Release the Manual Defrost button and
then press and hold for an additional 5 seconds until
“dEF” appears.
DEFROST WILL ONLY TERMINATE ONCE A SPECIFIC PRESET TEM-
PERATURE OR A PRESET TIME DURATION IS REACHED.
LAE Electronic Control
Info/Set Point
Button
Manual Defrost/
Down Button
Manual Activation/
Up Button
Stand-By
Button
Compressor
Running
Activation of 2nd
Parameter Set - NA
Alarm - NA
Cabinet in Defrost
Evaporator Fan
Running
LAE Control Icons