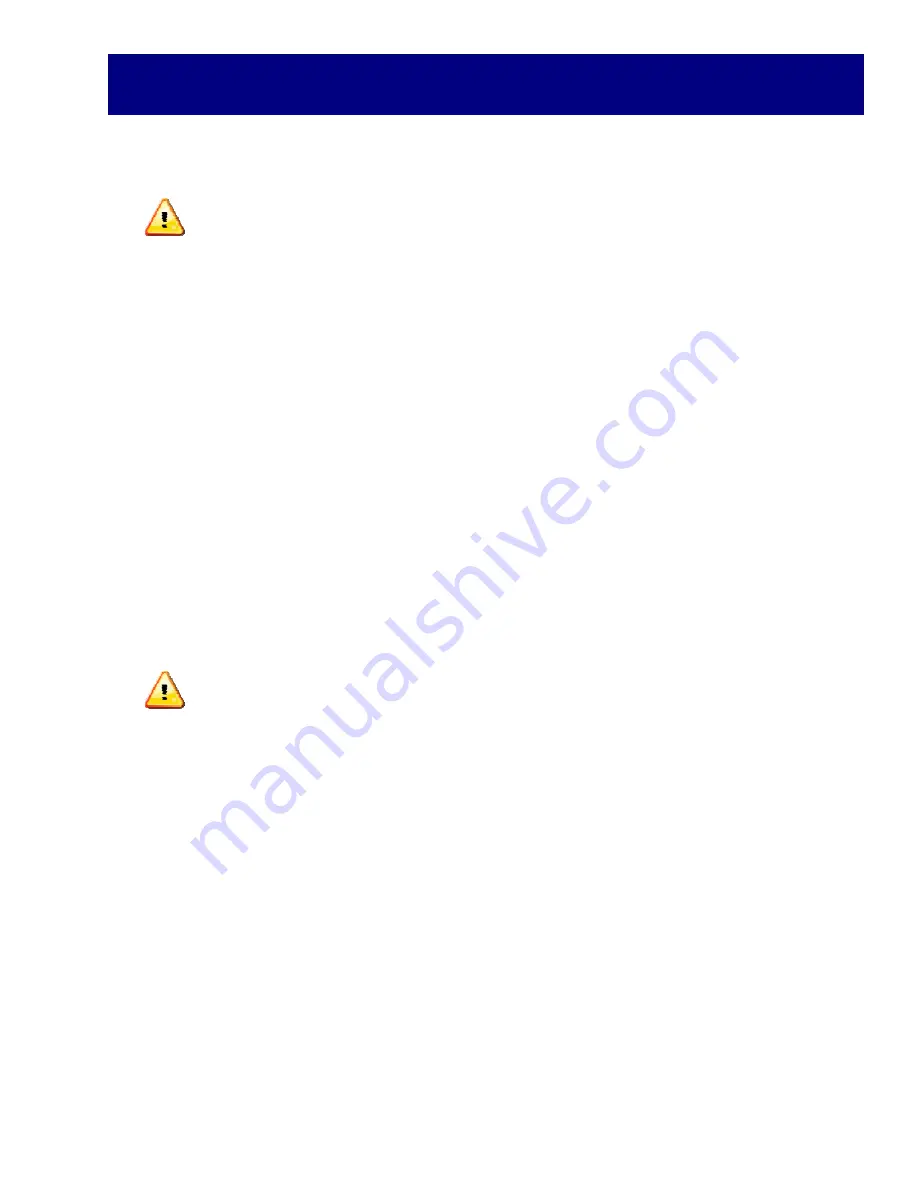
5
ELECTRIC
SHOCK
Electric
shock
can
injure
or
kill!
Precautionary
measures
must
be
taken
to
provide
maximum
protection
against
electri
‐
cal
shock.
♦
Do
not
touch
live
or
energized
electrical
parts
or
store
metallic
objects
near
power.
♦
Ground
the
work
or
metal
to
be
welded
to
a
good
electrical
(earth)
ground.
♦
Do
not
leave
an
energized
machine
unattended.
♦
Never
work
in
wet
clothing,
gloves
or
footwear.
♦
Insulate
yourself
from
work
and
ground
using
dry
insulation.
Make
certain
the
insulation
is
large
enough
to
cover
your
full
area
of
physical
contact
with
work
and
ground.
♦
Inspect
all
system
components,
protective
equipment,
cables,
connectors
and
gas
lines
prior
to
operating
equipment.
Never
use
cables
that
are
longer
than
necessary.
♦
When
testing
a
live
unit,
use
the
one
‐
hand
method.
Do
not
put
both
hands
inside
of
the
unit.
Keep
one
hand
free.
♦
Disconnect
input
power
conductors
from
de
‐
energized
supply
line
before
moving
a
welding
power
source.
♦
Always
be
sure
the
work
cable
makes
a
good
electrical
connection
with
the
metal
being
welded.
The
connection
should
be
as
close
as
possible
to
the
area
being
welded.
♦
Turn
OFF
welding
power
source
before
servicing
unless
the
procedure
specifically
requires
an
energized
unit.
♦
Never
touch
the
energized
stud
or
gun
before
discharging
the
stud
to
ground.
♦
Never
use
the
power
source
to
provide
heat
for
thawing
frozen
pipes.
ARC
RAYS
and
EYE
PROTECTION
Arc
rays
can
injure
eyes
and
burn
skin.
Arc
flashes
are
painful.
♦
Use
a
shield
with
the
proper
filter
and
cover
plates
to
protect
your
eyes
from
sparks
and
the
rays
of
the
arc
when
welding
or
while
observing
open
arc
welding.
♦
Use
protective
clothing
specifically
intended
for
work
with
welding
equipment.
It
should
be
made
of
durable
flame
‐
resistant
material
to
provide
ample
protection
from
the
arc
rays.
♦
Protect
other
nearby
workers
with
suitable,
non
‐
flammable
screening.
Caution
other
workers
not
to
watch
the
arc
nor
expose
themselves
to
the
arc
rays
or
to
hot
spatter
or
metal.
Stud
Welding
Safety
Precautions