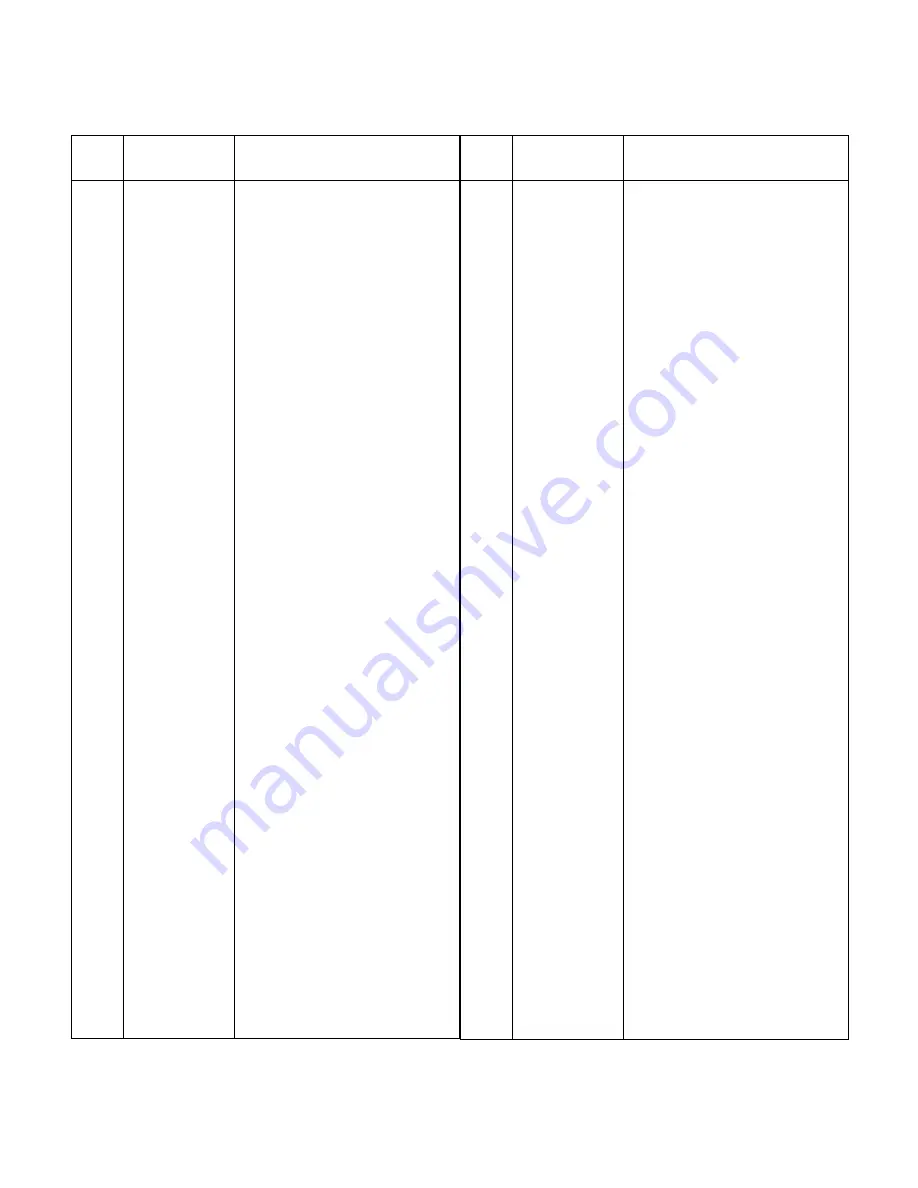
15
Model LS275
Ref.
No.
Part No.
Part Description
1.
718-0769
Hydraulic Cylinder
2.
727-0634
Hydraulic Tube
3.
710-1018
Hex Cap Screw 1/2-20 x 2.75
4.
737-0192
90 Degree Solid Adapter
5.
781-0526
Hose Guard
6.
737-0153
Return Elbow
7.
718-0481
Control Valve
8.
781-0538
Hose Guard
9.
710-0515
Hex Cap Screw 1/2-20 x 3.50
10.
719-0550
Wedge Assembly
11.
737-0238
Nipple Pipe 1/2-14
12.
712-0239
Lock Nut 1/2-20
13.
712-0711
Hex Jam Nut 3/8-24
14.
710-0459A
Hex Cap Screw 3/8-24 x 1.5
15.
781-0351
Adjustable Gib
16.
710-0604A
Hex Washer Screw 5/16-18 x .625
17.
781-1054
Support Bracket
18.
681-0162
Beam Assembly
19.
736-0300
Flat Washer .406 ID x .875 OD
20.
710-0654A
Hex Washer Screw 3/8-16 x 1.0
21.
781-1048
Dislodger
22.
781-0790
Back Plate
23.
736-0921
Lock Washer 1/2
24.
737-0312
Adapter 3/4-14
25.
727-0443
Return Hose 3/4” ID x 44” Lg.
26.
726-0132
Hose Clamp 5/8”
27.
737-0316
Filter Housing
28.
781-04000
Fender
29.
710-1238
Hex Washer Screw 5/16-18 x .875
30.
712-3010
Hex Nut 5/16-18
31.
736-0119
Lock Washer 5/16
32.
781-1024
Fender Mounting Bracket
33.
723-0405
Oil Filter
34.
710-0376
Hex Cap Screw 5/16-18 x 1.0
35.
681-0164
Light Bracket LH
36.
625-0062
Taillight
725-2058
RH Taillight Assembly
725-2059
LH Taillight Assembly
725-2060
Wiring Harness
37.
711-1587
Clevis Pin
38.
736-0116
Flat Washer .635 ID x .93 OD
39.
714-0470
Cotter Pin
40.
781-1027
Light Bracket RH †
41.
710-3097
Carriage Bolt 3/8-16 x 1.0
42.
712-0798
Hex Nut 3/8-16
43.
781-0682
Log Tray
44.
781-0686
Log Tray Bracket
45.
681-0161
Frame Assembly
46.
726-0214
Push Cap
47.
732-0583
Compression Spring
48.
710-0521
Hex Bolt 3/8-16 x 3”
49.
781-0690
Lock Rod
50.
737-0348
Vented Dipstick
51.
710-1338
Hex Screw 5/16-24 x 3.25
52.
710-0654A
Hex Washer Screw 3/8-16 x 1.0
53.
634-0186
Wheel Assembly
54.
712-0359
Slotted Nut 3/4-16
55.
714-0162
Cotter Pin
56.
734-0873
Hub Cap
57.
719-0353
Coupling Shield
58.
714-0122
Square Key 3/16” x .75
59.
718-0686
Flexible Coupling
60.
712-0123
Hex Nut 5/16-24
61.
736-0119
Lock Washer 5/16” ID
62.
781-0097
Rear Coupling Support Bracket
63.
727-0633
Hose
64.
718-0683
Gear Pump (11gpm)
65.
737-0329
45 Degree Elbow
66.
727-0502
High Pressure Hydraulic Hose
67.
781-0788
Tongue Tube Assembly
68.
747-1261
Latch Rod
69.
781-1045
Latch
70.
715-0120
Spiral Pin
71.
732-3127
Spring Compression
72.
736-0169
L-Washer 3/8”
73.
712-0798
Hex Nut 3/8-16
74.
710-0944
Hex Cap Screw 3/8-16 x 4.25
75.
736-0262
Flat Washer .385 ID x .870 OD
76.
713-0433
Chain
77.
750-0497
Spacer .375 ID x .625 OD
78.
727-0311
Coupling Hitch
79.
712-0375
Hex Lock Nut 3/8-16
80.
711-0813
Clevis Pin
81.
736-0185
Flat Washer .375 ID x .738 OD
82.
732-0194
Spring Pin
83.
781-0789
Jack Stand
84.
736-0351
Flat Washer .760 ID x .500 OD
85.
736-0371
Flat Washer
Ref.
No.
Part No.
Part Description