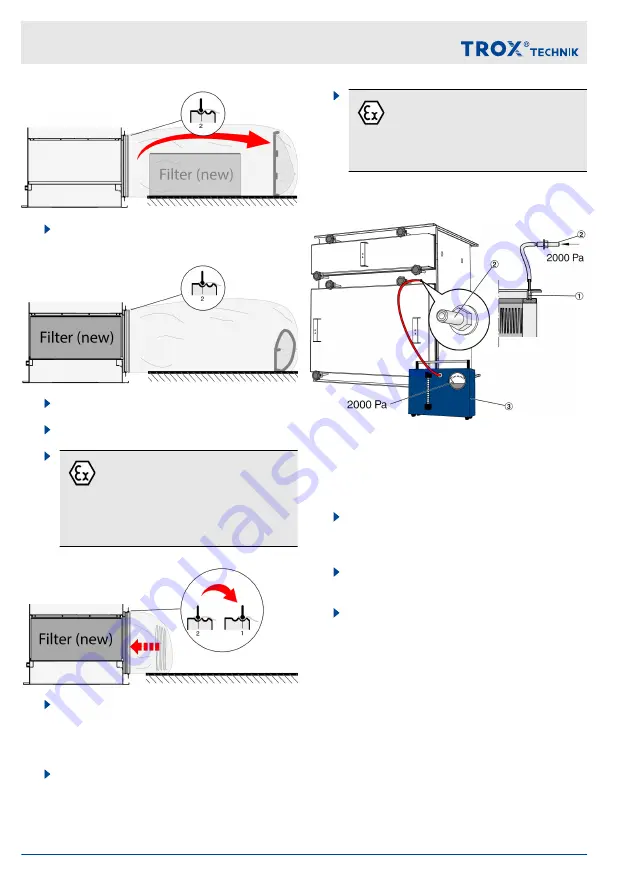
10.
Remove the old maintenance sack from
groove 1 and place it behind the new filter.
11.
Pushing the new filter into the casing
12.
13.
EXPLOSION HAZARD!
KSFS-...-Ex: Connect the earthing cable
to the filter element with the blade con-
nector (Fig. 2/3).
14.
Move the maintenance sack with the ring
seal from groove 2 onto groove 1. Roll up
the maintenance sack and place it in the
casing.
15.
Close the casing, Fig. 14.
16.
EXPLOSION HAZARD!
KSFS-...-Ex: Mount the earthing cable
from the filter chamber cover (Fig. 2/2).
Sealing integrity test
Fig. 15: Sealing integrity test
The casing is fitted with a sealing integrity test
facility. Sealing integrity is tested with a sealing
integrity test device (see operating manual).
1.
Connect the sealing integrity test device
(Fig. 15/3) to the connection point on the
filter (Fig. 15/2).
2.
Apply at least 2000 Pa to the test groove
(Fig. 15/1).
3.
Check the leakage rate on the flow rate
meter of the sealing integrity test device.
ð
The value must not exceed 0.003% of
the nominal volume flow rate.
If this value is exceeded, adjust the clamping
screws or the clamping frame; also check the seal,
test groove and filter element for damage. Then
repeat the sealing integrity test.
Maintenance
KSFS
∙
KSFS-...-Ex Ducted particulate filters
14