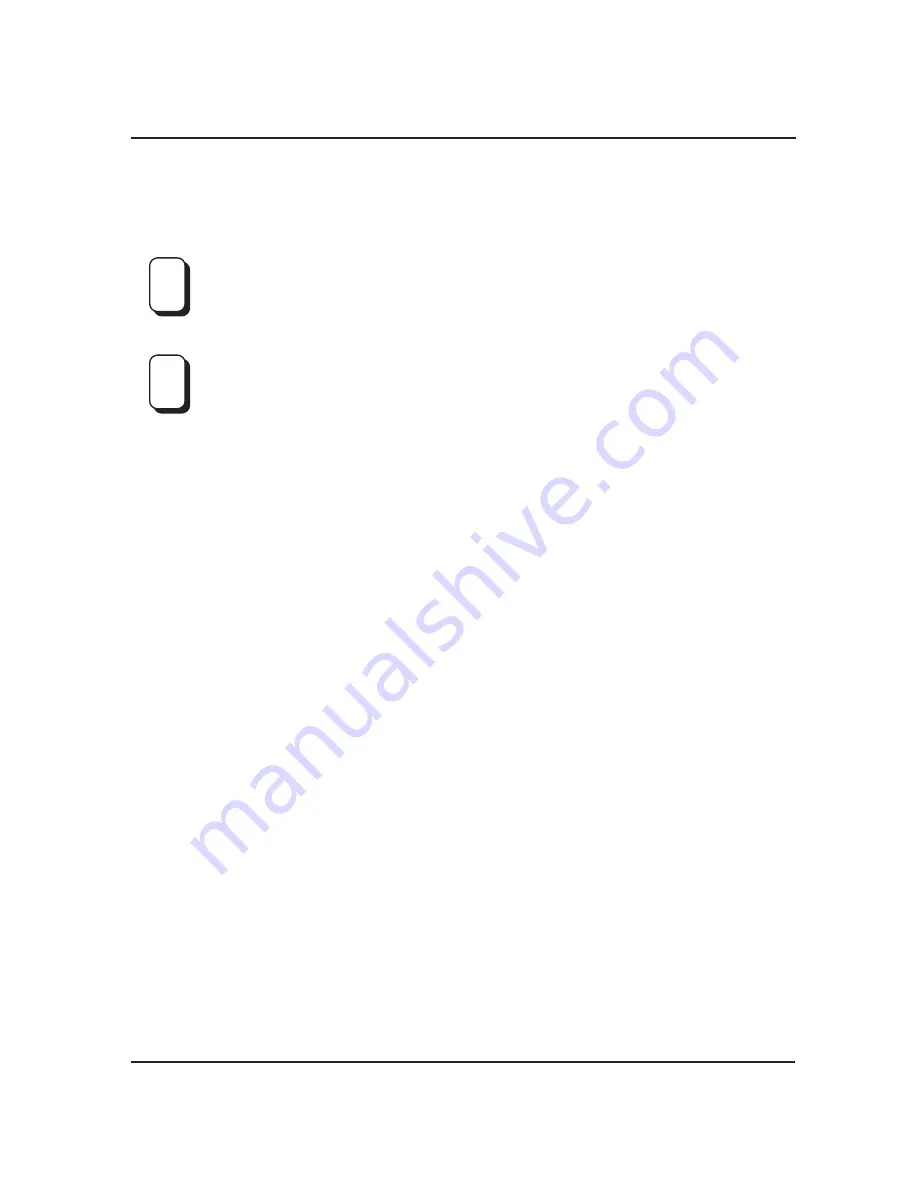
2.4 ELECTRICAL CONNECTIONS
Connect the electrical power cable to a 220-240 V, single phase, 50 Hz grounded power
supply. The electrical connecting is done by the DIN connector located on the front face
of the dryer.
Risk of electrical shock: When connecting the machine, cut off the power at the
connecting point.
2.5 RUNNING THE INSTALLATION
Various risks (explosion, projection, noise, ...): Do not pressurise until the installation
procedure has been completed.
The valves upstream and downstream of the dryer must be closed and the by-pass valve open
before the compressor is started.
1. Close the isolated switch located upstream of the dryer.
2. Check if the LED of the tower in drying operation glows and if the automatic drain valve
at the bottom of the prefilter drains every 4 mins.
3. Open slowly the down stream valve and check the pressure on the dryer's pressure gauge.
4. Avoid any sudden variation in pressure as this may damage the dryer.
5. Slowly open the upstream valve and check the pressure at the dryer's pressure gauge.
6. Slowly close the by-pass valve.
3. Operation
3.1 OPERATOR
Only a minimum level of experience in handling compressed air is necessary to operate a
Dryspell dryer:
l
Pressure and bar unit
l
Flow and m
3
/h unit
l
Dew points and
o
C unit
l
Components of a fluid network : compressor, valves, drains, taps, pressure
gauges, filters, tanks, ...
6
INSTRUCTION MANUAL -
Dryspell
This Document may be modified without notice
reproduction, even partial, forbidden without written Authentication
!
!