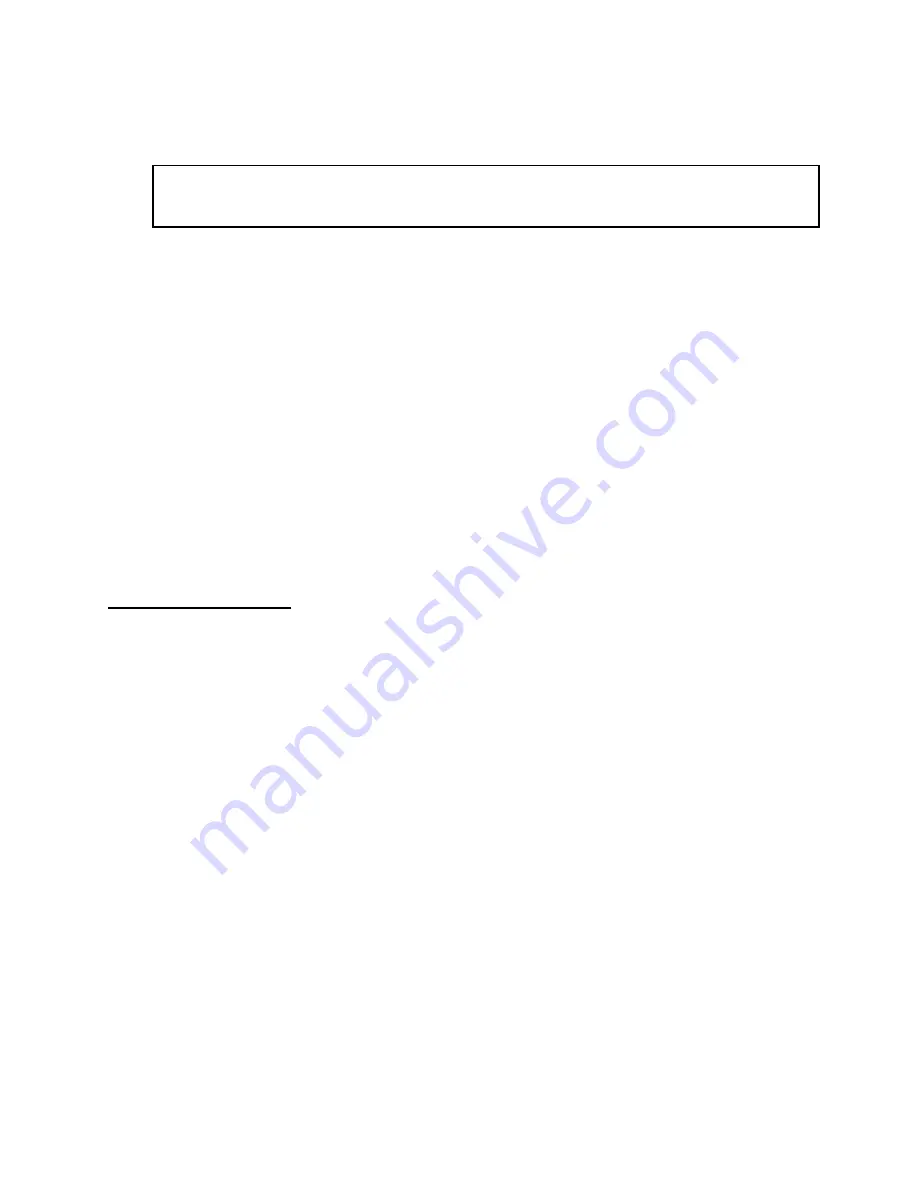
Page 19 of 36
6.
Check to make sure the waste bottle is in the proper position. Specific sample testing can now be
initiated as described in Section 8.4, Operating Procedures.
NOTE:
Whenever changing the fixer, re-prime the pumping system by pressing the fixer buttons
on each station for 60 seconds to clear any air bubbles from the lines. Air bubbles trapped in the
fixer tubing can displace material on the glass substrate if not cleared from the system.
8.3
– SHUT DOWN PROCEDURES
1.
Close FM-6 program.
2.
Go to start menu in lower left corner and go to Windows shutdown command.
3.
Allow Windows to completely shut down before turning off power to the unit.
4.
Flip power rocker switch from red to black to turn power off.
8.4
– OPERATING PROCEDURES
The operating procedures are divided into three groups: automatic cycle, semi-automatic cycle, and fixer
cycle. Once a technician is familiar with these procedures, it is only necessary to follow the steps as a
refresher. All other information is background and of general interest.
8.4.1 – Automatic Cycle
The AUTO button initiates the flow of liquid across the Ferrogram at a controlled rate and automatically
switches to a rinse and drying cycle resulting in a completely prepared Ferrogram.
1.
Preheat the sample to 150°F (65ºC +/- 5º), in the sample oven prior to testing.
2.
Using a pipette dispenser, remove 2 ml of sample lubricant from the sample bottle and add it to a
new sample vial.
3.
Using the dispenser assembly on the fixer/oil bottle, dispense 1 ml of fixer into the sample vial.
Depending on oil viscosity an additional 1 ml of fixer can be added to thin the solution creating 4
ml of solution.
4.
Mix solution thoroughly by shaking vigorously with the opening closed or using a vortex mixer.
5.
Raise the delivery arm assembly vertically corresponding to the station the sample vial will be
positioned in.
6.
Insure the wire slide lifter is positioned down against the magnet assembly.
7.
Unpack a glass substrate from its protective envelope.
8.
Carefully, holding the glass substrate by the edges with the black circle located in the lower left
side of the glass substrate, place entry end of the glass substrate on the lip of the magnet assembly
Summary of Contents for FM-6
Page 11: ...Page 11 of 36 ...