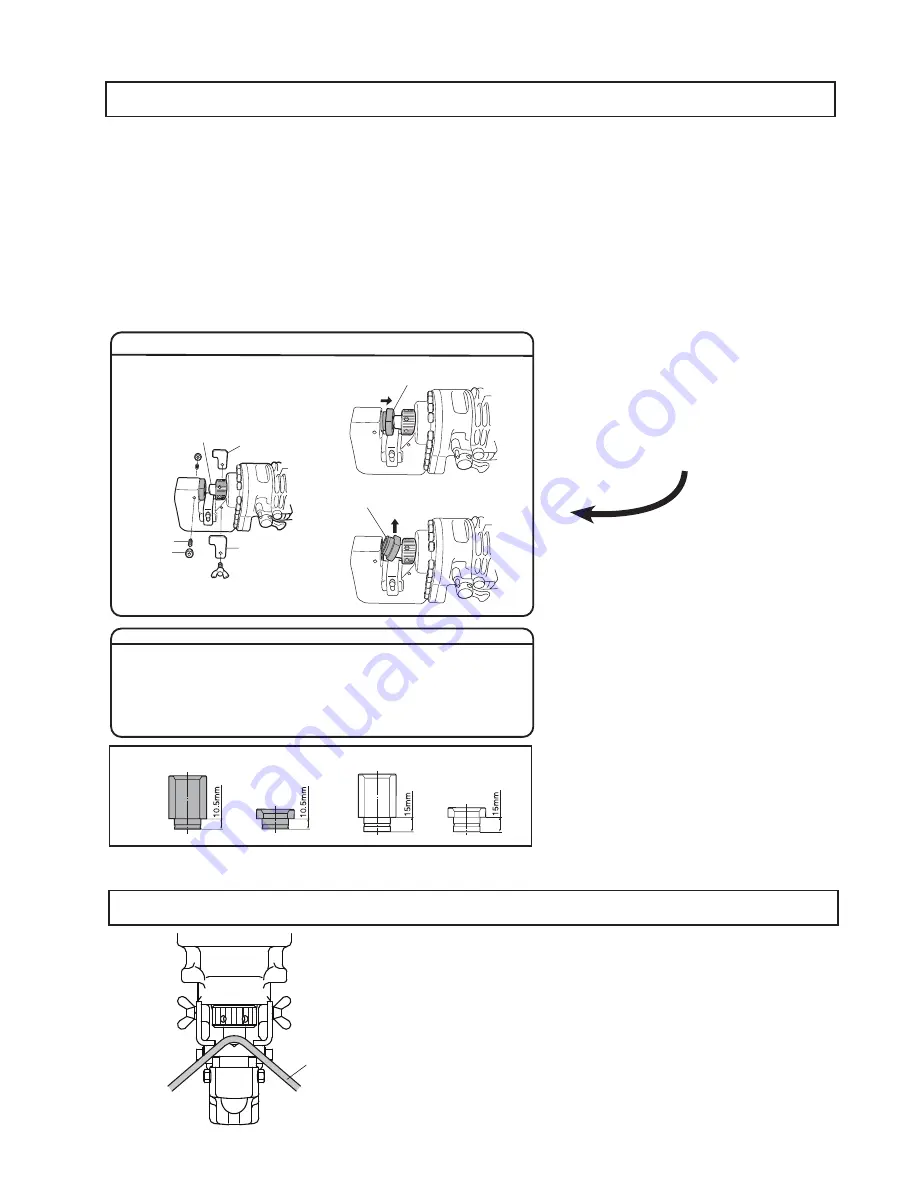
8
SELECTING PROPER DIES
Proper die selection is essential. Other than the obvious
necessity of matching shaped punches and dies, there are
two other basic selection factors that must be considered.
The first is die clearance. Different material types and
different material thicknesses require different clearances
between the punch and die. In order to maintain the best
possible hole while remaining within the tonnage
capacity of the machine, it is essential to choose the die
with the proper clearance. The second is the die angle.
Most structural shapes can be punched with the standard
flat dies, but "I" -beams and most channels which
have a 2-in-12 taper require the use of special
9-1/2 degree angled dies. Car and ship channel
flanges and other structural shapes with a 2 degree
taper can be punched with flat dies. Materials with
a flange taper of less than 5 degrees can also be
punched with the flat die, however, the hole will be
slightly angled. Refer to specific information and
tables within this manual for the proper punch and
die combination.
Hougen-Ogura Punches are
designed to be used in
Structural Steel. If used in harder
or higher tensile strength
materials, performance will be
impeded and serious damaged
could occur to your unit.
Your Hougen-Ogura punch unit
has been equipped with a new
die configuration. Please review
this information prior to
operating your machine
1. To make it easier, please remove the
strippers
3. Pull the die up to the tip of the punch
2. Unscrew the nuts and set screws
that hold the die in place
4. Remove the die from the “C”- frame,
inclining it to remove.
STRIPPER
STRIPPER
PUNCH
SET SCREW
NUT
REMOVING THE NEW DIE
INSTALLING A PUNCH
1. To make the operation easier, first remove the strippers on both sides.
2. Reference your Operators manual and remove your punch and the die.
3. Install a new punch and punch retaining nut.
4. Install the die (Reference the steps above and work in reverse)
5. Tighten the punch retaining nut according to the Instructions in your Operators manual.
New Die
Old Die
CAUTION WHEN SELECTING THE DIE
It is important that the die selected is correct for the thickness of the material to
be punched.
Punching material of thickness 4 mm to 8 mm using a die for thinner material
can cause the punch to jam in the material. This is due to the smaller clearance
betweenthe die and punch. In such a case the material will be pulled up by the
retracting punch as shown in the drawing on the left. Special care should be
taken when punching flat bar of mild steel, aluminum and copper.
Material
Summary of Contents for Hougen-Ogura PUNCH PRO 75004PR
Page 12: ...12 PARTS BREAKDOWN ...