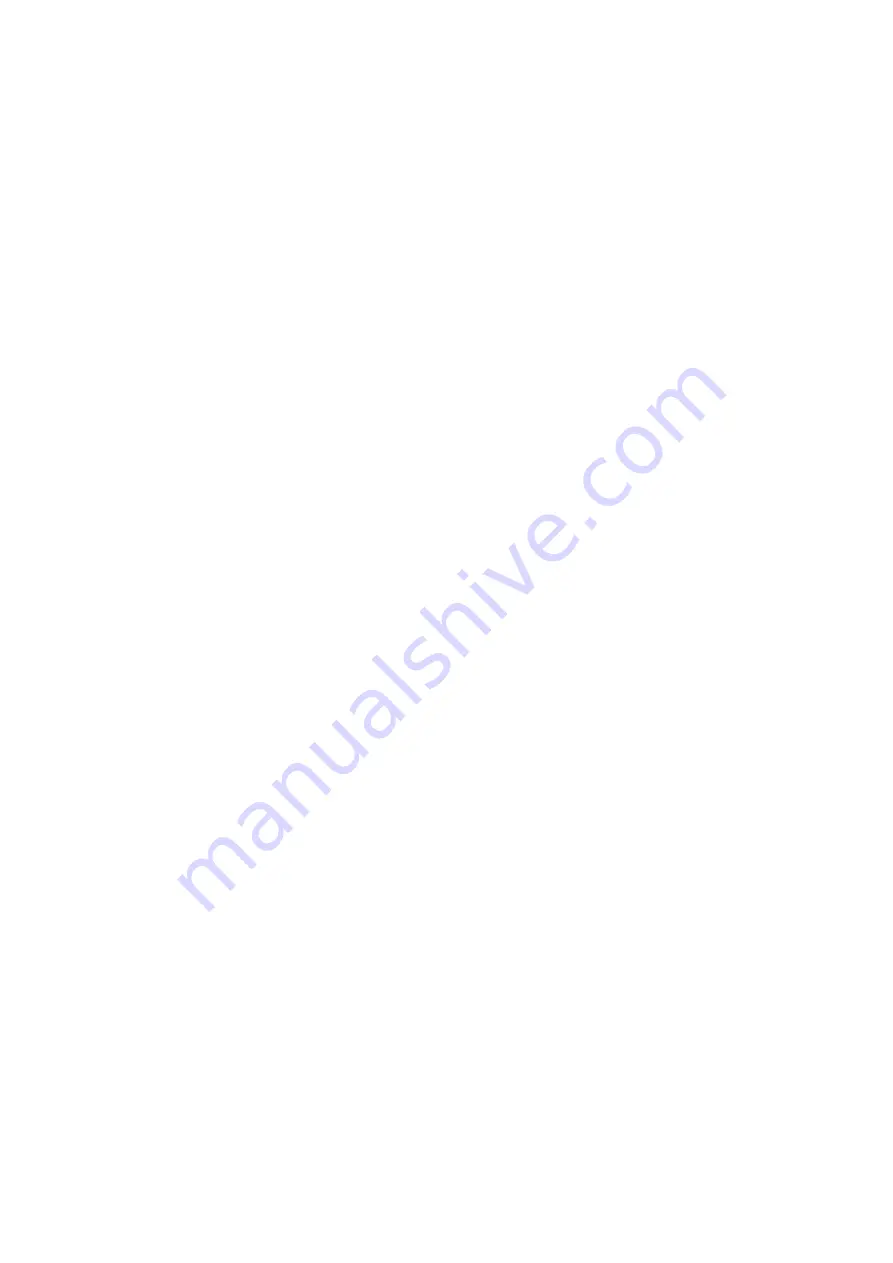
11
5. OIL SUPPLY
Oil
The oil burner is factory set to burn Kerosene C2 to BS 2869.
Note: Only Kerosene is permitted for use on this appliance.
IMPORTANT NOTE:
The oil storage tank and supply pipe must be installed by
an OFTEC-trained and registered engineer.
Oil Storage Tanks
Size and Location of Tank
The tank should be large enough to allow for economic
deliveries and be located in the most unobtrusive
position, having regard to the need for safety, filling,
maintenance (if steel tank) and the head of oil required.
Whilst it is highly unlikely that a fire could start from a
domestic oil tank, it does however need to be protected
from a fire that may originate in a nearby building,
therefore the tank should not be located nearer than 1.8
metres from a building, nor closer than 760mm from a site
boundary. Where a tank has to be less than 1.8 metres,
the building wall must not have any openings other than
small ventilation openings. The wall shall have a half
hour resistance to an internal fire and extend 1.8 metres
from any part of the tank.
Alternatively, a non-combustible radiation barrier must be
provided which meets the requirements of BS 5410 Part
1: This standard applies to tanks up to a capacity of
3,400 litres which is deemed the maximum size for a
single family dwelling.
Steel Tanks
Steel tanks should comply with the requirements BS 799,
Pt. 5: 1987 and mounted on brick or block piers with a
waterproof membrane between the piers and tank.
The tank should be fitted with fill and vent connections
(weather protected), a drain-off cock, shut-off valve and
an oil level indicator.
Plastic Tanks
Polyethylene tanks are now widely used because of their
advantages over traditional steel tanks:
(a) They do not need pier supports and can be mounted
directly on any flat surface giving uniform support for
the tank base.
(b) They do not corrode and therefore never need
painting.
(c) They are easier to handle because of their lower
weight.
(d) They have a 10 year manufacturer’s guarantee.
Plastic tanks should be fitted with similar components to
those used with steel tanks.
Fire Protection
To comply with building regulation Section J5:
1
Where a storage tank is close to a dwelling, fire
cladding must be provided to the eaves, if less than
1.8m from the top of the tank.
2
The cladding must extend 300mm beyond the tank.
3
The tank must be sited on a non-combustible base.
Pollution Protection
To comply with building regulation section J6, the tank
must be ‘BUNDED’ (i.e. double walled) if:
1
The tank is less than 10m from a stream.
2
The tank is less than 50m from a well, spring, or drinking
water.
3
The tank cannot be viewed from the delivery point.
4
In the event of a leak, there is a risk of oil reaching a
manhole cover or drain.
5 The tank capacity exceeds 2500 Litres.
Oil supply line
A long life flexible oil hose is supplied with the boiler, a
filter and shut-off valve are required. These should be
fitted as shown in Figs. 11,12 & 13.
The oil shut-off valve should be fitted as close to the
burner as practicable to enable the burner to be
disconnected without undue loss of oil. The filter must be
connected in the oil supply pipe and positioned outside
the building.
Fire Valve
A fire-valve must be fitted in the oil line outside the
building with its sensing phial positioned within the boiler
casing above the level of the burner. A clip is provided for
retaining the phial.
All oil line joints must be completely sealed and the total
pipe run thoroughly flushed out before connecting to the
burner. No soldered joints are permitted in the oil line.
The oil line can be fed into the back of the boiler base tray
or through the holes at the side.
Single pipe oil supply (Fig. 11 )
When, the bottom of the oil supply tank is above the
burner, a single pipe gravity system can be used. The oil
supply pipe must be connected to the suction port on the
burner pump via the flexible hose.
Summary of Contents for EuroStar Premier 100/125 Condensing
Page 10: ...FIG 5 WIRING DIAGRAM 7...
Page 21: ...Fig 19 19 7 18...