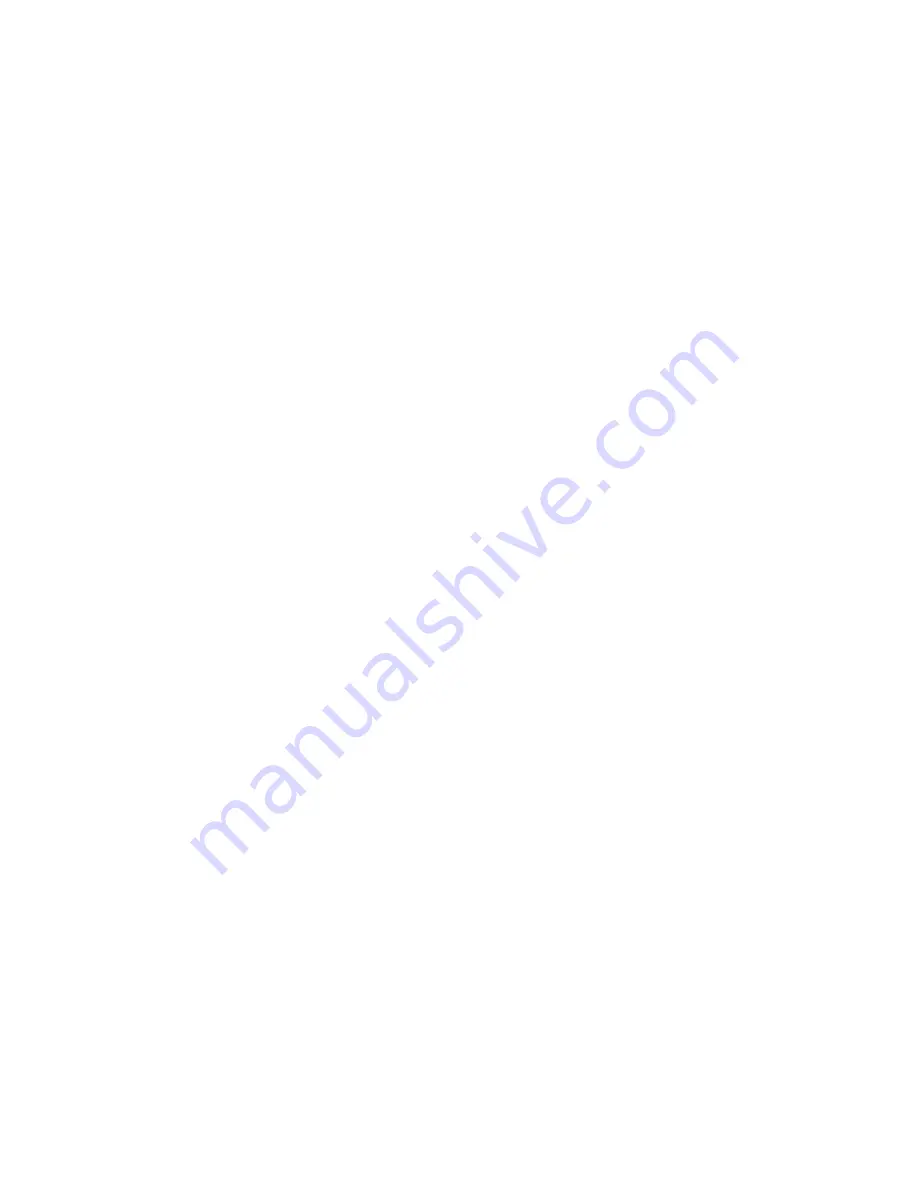
INSTALLATION INSTRUCTIONS
INSTALLATION
The installation and start-up of evaporators should only
be performed by qualified refrigeration mechanics.
This equipment should be installed in accordance with
all applicable codes, ordinances and local by-laws.
INSPECTION
Inspect all equipment before unpacking for visible signs
of damage or loss. Check shipping list against material
received to ensure shipment is complete.
IMPORTANT:
Remember, you, the consignee, must
make any claim necessary against the transportation
company. Shipping damage or missing parts, when
discovered at the outset, will prevent later unnecessary
and costly delays.
If damage or loss during transport is evident, make
claim to carrier, as this will be their responsibility,
not the manufacturer’s.
Should carton be damaged, but damage to equipment is
not obvious, a claim should be filed for “concealed
damage” with the carrier.
IMPORTANT:
The electrical characteristics of the unit
should be checked at this time to make sure they
correspond to those ordered and to electrical power
available at the job site.
Save all shipping papers, tags and instruction sheets for
reference by installer and owner.
APPLICATION
TPLP
evaporators are designed for walker-in cooler and
freezer applications used with a wide range of refriger-
ants. For room temperatures above 35°F
(2°C)
AND
evaporating temperatures above 26°F
(-3°C)
, positive
defrosting means (electric) may not be required,
otherwise, electric defrost defrost models should be
used. Electric defrost models come with defrost
termination and fan delay as standard to control the
defrost cycle termination and fan delay, while defrost
initiation means (e.g. defrost timer) is not included.
The coil must not be exposed to any abnormal
atmospheric or acidic environments. This may result in
corrosion to the cabinet and possible coil failure (leaks).
(Consult manufacturer for optional baked on phenolic
protective coatings).
LOCATION
The unit location in the room should be selected to en-
sure uniform air distribution throughout the entire space
to be refrigerated. Be sure that the product does not
obstruct the free circulation of air. Allow a minimum of
24” clearance at each end. Do not locate evaporators
over doors. Consideration should be given to the coil
location in order to minimize the piping run length to the
condensing unit and floor drain.
EXPANSION VALVE (TXV) PRE-SELECTED
Locate the expansion valve bulb on a horizontal length
of suction line preferably 3 to 6 inches from the suction
header. Locate the bulb at 4 or 8 clock position and
insulate with a waterproof type of insulation. Clamp the
bulb to ensure 100% contact of the bulb with the
suction line.
After following the manufacturer’s installation instructions
and after the room has reached the desired
temperature the valve superheat should be checked.
This will confirm that the evaporator is operating
properly and performing to maximum efficiency. The
superheat should be around 6
(3.3°C)
to 8°F
(4.4°C)
for
a 10 to 12°F T.D
(5.6 to 6.7
°
C)
. Too high or low a super
heat will result in unsatisfactory system
performance and possible compressor problems.
MOUNTING
Refer to dimensional drawing for recommended
mounting arrangements. Ensure adequate clearance
is provided behind the coil as well as each end. The
evaporators may be mounted flush with ceiling with
bolts, or hanging down with rod hangers. When using
rod hangers, allow adequate space between the top of
the unit and the ceiling for cleaning to comply with NSF
Standard 7.
Ensure that the ceiling is level since the drain pan
has been sloped for drainage during the defrost
cycle.
DRAIN LINE
The drain line should be run from the drain connection,
sloping at least 1”
(25 mm)
per foot and should have
the size at least as large as the drain connection. A
P-Trap in a warm area outside the room must be
provided to allow proper draining through the tubing.
Connection should be made to proper drainage facilities
that comply with local regulations.
To prevent freeze-up when the temperature of the
refrigerated space is 35°F
(2°C)
or lower, the drain line
should be heated along its run inside the cold room.
The heated drain line should be insulated. It is recom-
mended that the heater be energized at all times. A
heat input of 20 watts per foot in a 28°F
(-2°C)
room
and 30 watts per foot for -20°F
(-29°C)
rooms, is
satisfactory. Drain line heaters are not required for
constant room temperature above 35°F
(2°C)
.
Always trap evaporator drain line individually to prevent
vapor migration.
Ensure that the drain line has sufficient slope for
proper drainage (prevention of ice build up/block-
age in pan).
TPLP
60Hz
23/12/16
T30-TPLP-PDI-11
- 24 -