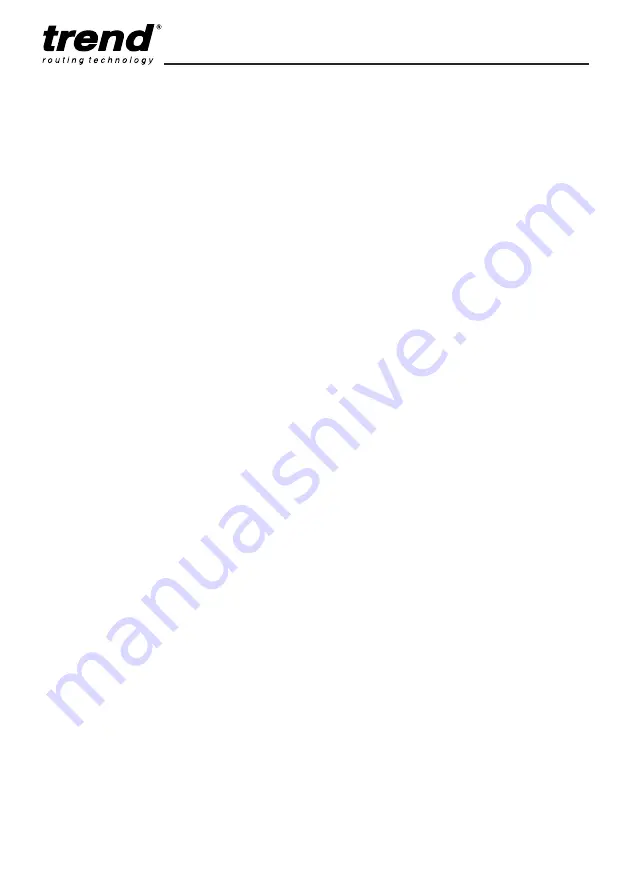
DJ300
SAFETY PRECAUTIONS
■
Always switch off the power and unplug the
router when changing cutters or when making
adjustments.
■
Always wear protective goggles when routing.
■
Wear sound protective ear muffs when routing
for long periods of time.
■
Always wear a dust mask or respirator. Use
dust extraction equipment whenever possible.
■
Do not wear loose clothing. Make sure baggy
sleeves are rolled up and ties are removed.
■
Always remove spanners and hex keys from
the workpiece before switching router on.
■
Keep hands well clear of the router cutter
when routing.
■
Avoid accidental starting of the router. Make
sure the power switch is in the ‘Off’ position
before plugging in and connecting to the
electrical supply.
■
Never leave the router unattended when
running. Always wait until the router comes to
a complete stop before making any
adjustments.
■
Do not switch the router on with the cutter
touching the workpiece.
■
Mount the Dovetail Jig securely to a work
bench or to a workboard fitted to a suitable
surface.
■
Periodically check all nuts and bolts to make
sure they are tight and secure.
■
Use dust extraction equipment.
Cutter Care
■
Do not drop cutters or knock them against
hard objects.
■
Cutters should be kept clean. Resin build-up
should be removed at regular intervals with
Resin Cleaner
®
. The use of a dry lubricant
will act as a preventative such as Trendicote
®
PTFE spray.
■
Cutter shanks should be inserted into the
collet at least
3
/
4
of shank length to prevent
distortion. A distorted collet should be
discarded, as it can cause vibration and
damage the shank.
■
Do not overtighten collet as this will score the
shank and create a weakness.
■
It is also advisable to periodically check the
router collet nut for wear.
Useful Advice
■
Judge your feed rate by the sound of the
motor. In time, the operator will acquire a
‘feel’ for the router and a feed speed relative
to the work will come naturally. Too slow a
feed will result in burning.
■
Apply the normal precautions as with any
electric power tool.
■
The main cause of routing machine failure is
the inclination for operators to overload them.
The motto is ‘Keep the revs up’. The drop in
revolutions should not exceed, if possible,
more than 20% of full running speed.
■
The motor of a router is susceptible to the
accumulation of sawdust and wood chips and
should be blown out, or ‘vacuumed’,
frequently to prevent interference with normal
motor ventilation.
■
Refer to the Instruction Manual supplied with
your router for full details of it’s features and
safety information.
■
The use of a fine height adjuster is highly
recommended (if available for your router) for
accurately adjusting the height of the cutter
when dovetailing.
■
Trial cuts should be made on waste material
before starting any project.
-3-
Summary of Contents for DJ300
Page 1: ...DJ300 DOVETAIL JIG...