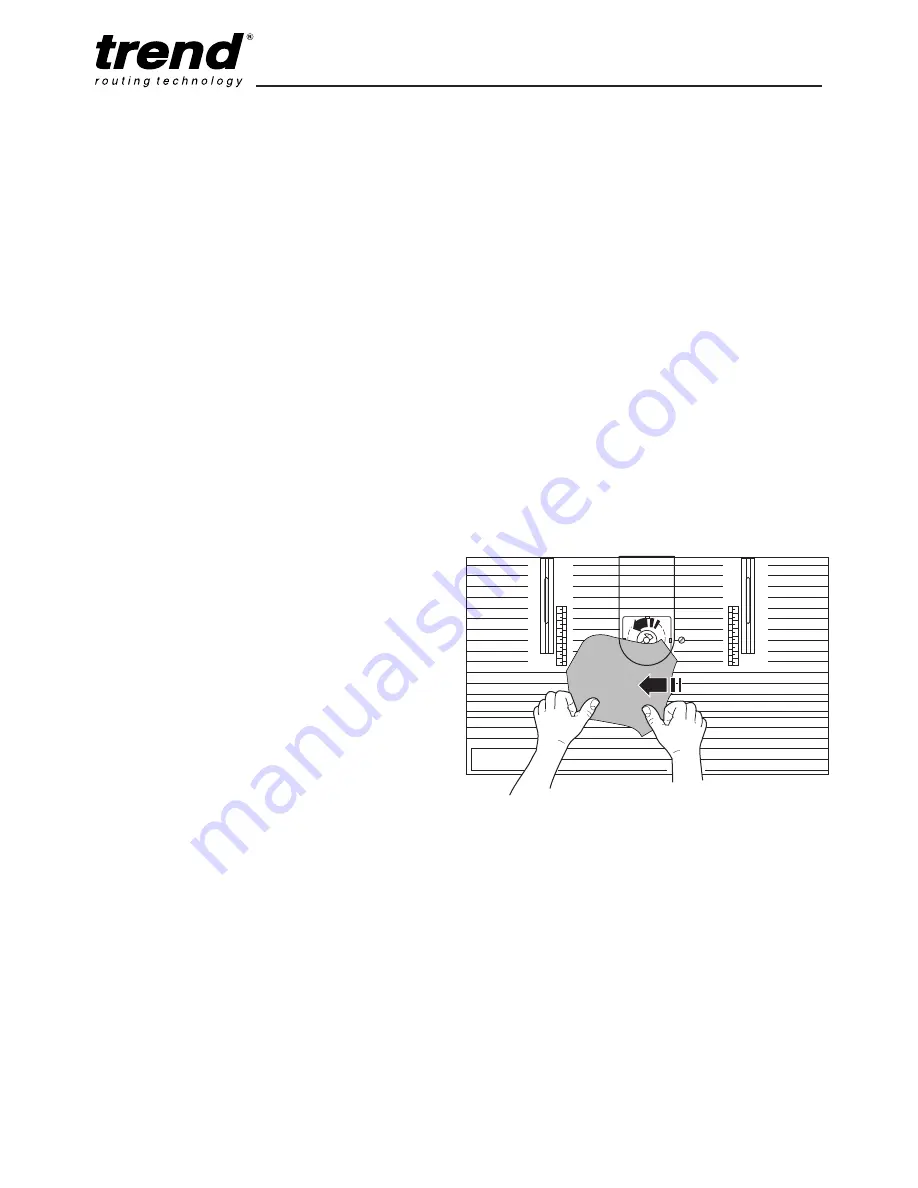
-26-
CRT MK2
EXAMPLE APPLICATION
Producing a Shield
■
Construct an actual size template of the
design from 6mm MDF or plywood ensuring
that it is accurate and free from
imperfections.
■
Fix the template to the back of the workpiece
to be used using screws or double sided
tape.
■
Rough cut the workpiece to the shape of the
template using a band saw or jigsaw leaving
2-3mm oversize.
■
Fit a ball bearing guided trimmer cutter.
■
Lay the workpiece (with template fitted) face
down on the table surface. Adjust the height
of the cutter. Ensure that the ball bearing will
contact the template and the cutting edge of
the cutter will machine the full edge of the
workpiece.
■
Fit the profiling top guard and adjust height to
give a 6mm gap between the top of cutter
and underside of template.
■
Switch router on and position the workpiece
against the lead-on pin as shown. The
workpiece should not contact the cutter.
■
Rout the shield using the procedure
described on the previous pages.
Useful advice
If natural woods are used, consideration should
be given to break-out of short grain which will
effect your decision as to where to start the
routing operation in order to prevent it.
Moulding the Shield
A suitable ball bearing guided cutter should be
chosen to mould the shield.
■
Fit chosen moulding cutter and adjust height
of cutter to achieve shape required.
■
If the full edge of the workpiece is to be
machined, leave the template attached to the
workpiece so as to provide a guide for the
ball bearing. Otherwise the template can be
removed, providing there is sufficient edge for
the ball bearing to follow.
■
Repeat the same routing procedure as
before.
If the profile required involves excessive removal
of material, it is advisable to take two passes
with the cutter. First reduce the height of the
cutter protruding from the table, this in effect,
reduces the amount of material which will be
removed, or fit a larger ball bearing, if one is
available for that particular cutter.
The second pass can then be made to give the
required finish.
Carrying out this two stage routing operation has
many advantages.
■
Improved finish on workpiece
■
Less load on cutter and router
■
Far less risk of workpiece snatching
Definition of Snatching
This can be described as the cutter catching the
workpiece and projecting it away from the
direction of rotation. The workpiece is often
taken from the operator's hands and projected
across the work area. It can have potentially
dangerous consequences if the cutter is
unguarded and/or the operator's hands are too
close to the cutter. Damage to the cutter can
also be caused.
The following precautions should be made to