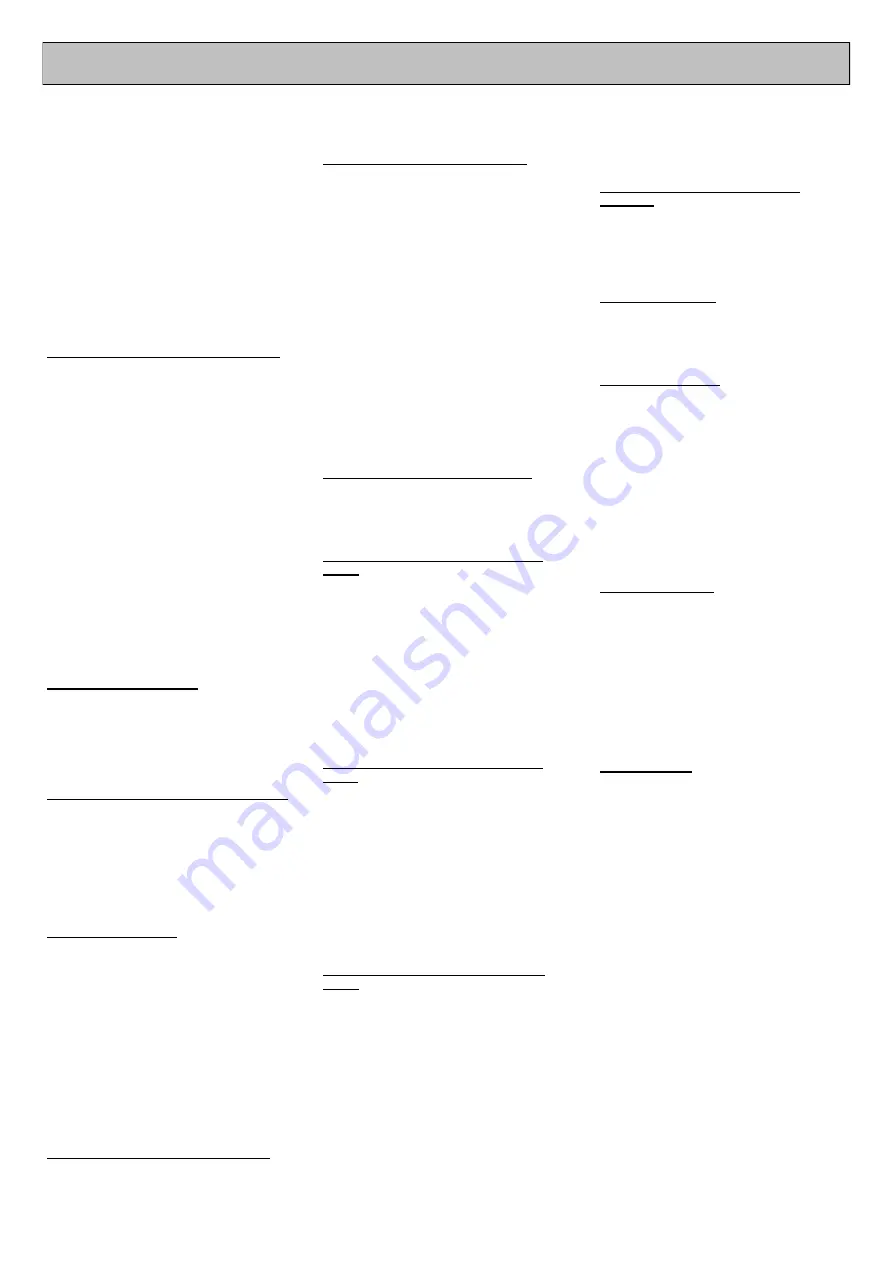
SERVICING
nuts (59) and remove the u-bolts (57) and
mounting brackets (58).
Removal of Handle from Sub-Frame
Lay the tool on its front, with the handle
uppermost. Select two 24mm (15/16”A/F)
spanners and unscrew and remove nut (25)
and washer (27), and withdraw bolt (26) and
washer (27). Depress the foot handle release
lever and remove the handle from the
subframe.
ASSEMBLY
Assembly is generally the reverse of
dismantling. Before assembling, ensure all
parts are clean and all internal parts have a
film of air tool oil. Replace any parts that
show signs of wear. If the tool is being fully
serviced it is recommended to change anti-
vibration mountings (31) and (28), along with
the O‟Rings (44) and the brush seals (48). It is
good practice to replace the split pins (33) and
locknuts (29) and (25) during assembly.
Assembly of Pistons / Cylinder Head
Set the cylinder block in the upright position,
carefully
placing
supporting
blocks
underneath to aid assembly, take care not to
block the exit holes for the pistons.
Cutter Head / Piston replacement (Two
Piece)
Fit the pistons (42) into the cylinders (43) and
insert all pairs into the cylinder block as per
service layout. Fit a new O‟Ring (44) into each
of the recesses on the outside of the cylinders
on top of the cylinder block. Lubricate each of
the pistons. Insert two bolts into the cylinder
head to act as a guide to align the head with
the bolt holes and carefully lower it into place
taking care not to disturb the O‟Rings or
trapping your fingers. Insert the 7 cap head
screws (41) and tighten initially by hand,
tighten to a torque of 55Nm (40lbs/ft).
Cutter Head / Piston replacement (One
piece)
Fit the pistons (52) into the cylinders (43) and
insert all pairs into the cylinder block as per
service layout. Fit a new O‟Ring (44) into each
of the recesses on the outside of the cylinders
on top of the cylinder block. Put a few drops of
recommended lubricating oil on top of each
piston. The cylinder head is very heavy,
carefully lower it into place taking care not to
disturb the O‟Rings or trapping your fingers.
Insert the 7 x cap head screws (41) and
tighten initially by hand, tighten to a torque of
55Nm (40lbs/ft).
Assembly of Exhaust Chamber / Cutter
Heads
Carefully turn the block assembly over on to
the cylinder head (39). Lower the exhaust
chamber (46) into position with the cavity
nearest the block (45), Fit new brush seals
(48) into the brush seal recesses and lower
the sealing plate (47) into position with the
brush seal recesses nearest the block. If a
brush seal is loose in the recess, pull the
brush seal apart slightly to make it a tighter fit.
Insert hexagon head bolts (49) through
sealing plate (47), exhaust chamber and into
cylinder block (45). Tighten initially by hand,
then torque the bolts down to 80 Nm (60lb.ft.).
If fitted, screw on the cutter heads (50) initially
by hand, select a 19mm A/F (3/4") spanner for
the flats of the piston (42) and a 27 mm
spanner for the flats of the cutter head (50),
ensuring that the new heads are tightened to
torque of 55Nm (40lbs/ft) and that both mating
faces are in contact with one another.
Sub-frame to Cylinder Block / Head
assembly
Align mounting holes on sub-frame with anti-
vibration pad (31) studs and fit as shown in
service layout. Fit washer (30) and locknut
(29) to both studs and fasten by hand. Screw
both nuts down to a torque of 40 lb/ft.
Wheel to Sub-Frame
Slide wheel (35) onto sub-frame axle, fit
washer (34) and insert a new split pin (33) into
the hole. Separate legs on split pin and bend
round with pliers. Repeat for the other wheel.
Handle to Sub-Frame
Fit new anti-vibration rubber mountings (28) to
the holes in either side of the handle (19) and
slide assembly into position between the axle
arms of the subframe (32), fit washer (27) to
bolt (26) and align all holes to allow the
insertion of the bolt as shown in the service
layout. Guide bolt through anti-vibration pads
(28) until it appears at the other end. Fit
washer (27) to threaded end of bolt and fit nut
(25). To ensure that the sub-frame does not
buckle through over tightening and that the
vibration rubbers are set correctly, tighten until
both washers are no longer free to rotate.
Ball Valve Mounting
The ball valve should be fitted so that the
valve is open when in line with the handle. Fit
one of the two u-bolts (57) around ball valve
(56) and through u-bolt clamping bracket (58).
Guide the u-bolts through the holes in the
mounting flange on the handle. Fit 2 x nuts
(59) finger tight to hold the unit in place.
Repeat with second u-bolt and bracket. Align
the ball valve lever with the main handle.
Select a 13mm A/F spanner and fasten evenly
four nuts (59) until valve is secure.
Vacuum Shroud
To fit the optional vacuum shroud assembly
(51) remove the eyebolt with a suitable bar,
then lay the tool on its front face, unlock the
handle and pull the cylinder block onto its top
face. Select a 19mm (3/4") A/F socket and
unscrew and remove the 5 x hexagon bolts
(49). Select an 8mm A/F (5/16”) spanner and
unscrew completely the front 3 x hexagon
head screws (53) and the associated front
clamp plate (52). Thread the tube of the
vacuum shroud assembly (51) through the
subframe (32). Align the holes and secure
using the 5 x 10mm cap head bolts supplied
with the vacuum shroud. Refit the clamp plate
(52) with the supplied screws (53) ensure that
the neoprene seal is square and securely
clamped. For dust free working it is
recommended that a Trelawny recommended
vacuum system be connected to the vacuum
shroud assembly.
Disposal
Dismantle into component form for disposal
according to material composition and
disposed of using waste recycling processes
specified by local regulations.
Note: Flammable material such as plastic,
rubber or composite materials must not be
incinerated but should be disposed of using
normal industrial waste disposal processes.
Remove the eyebolt (38) from the cylinder
head, then lay the tool on its front face, unlock
the handle and pull the cylinder block onto its
top face; select a 19mm A/F (3/4”) spanner for
the flats of the piston (42) and a 27 mm
spanner for the flats on the cutterhead (50).
Unscrew the cutterhead and remove from the
piston. It is also advisable at this point to
replace the brush seals, select a 19mm A/F
(3/4”) spanner and unscrew the 5 x hexagon
head bolts (49). Remove the bolts and sealing
plate (49/47). Remove the worn brush seals
(48), which may need prising out of their
recesses.
See:
Assembly of Exhaust Chamber/Cutter
Heads.
Cutter Head / Piston removal (One Piece)
To replace the one-piece pistons (52), place
the cylinder block on wooden blocks so that
the cutterheads are clear of the floor. Unhook
the main handle from the chassis and lay the
handle on the floor. Using a 19mm (3/4")
spanner unscrew and remove the two-nyloc
nuts (29) from the upper vibration reducing
mountings. Using a 10mm Allen key, remove
the 7 x socket headed bolts (41) from the
cylinder head (39). Take care when removing
the cylinder head as it weighs 16.4kg
(36.0lbs), take extreme care against trapping
your fingers when lifting and placing the
cylinder head down, use a hoist or other
suitable lifting equipment whenever possible.
An eyebolt (38) is supplied fitted to the
cylinder head for this purpose. Remove the
O'Rings from the cylinders and remove the
piston and cylinder as an assembly. Inspect
the components for wear paying particular
attention to the small bore of the cylinder.
Exhaust Chamber removal
Remove replaceable cutterheads, if fitted (50),
sealing plate (47) and brush seals as in
“Cutterhead/Piston removal section".
Remove the exhaust chamber and clean out
any dust that may have accumulated inside
the chamber.
Removing Sub-Frame from Cylinder Block
Lay the tool on its front, with the handle
uppermost, select two 32mm (1 1/4”)
Spanners and unscrew the hose (60)
connector from the lower ball valve adapter
(55). Select a 19mm (3/4"A/F) spanner and
unscrew the 4 x locknuts (29) securing the
chassis to the vibration reducing mountings
(31) and remove all nuts and washers (29/30).
Cylinder Head removal
Repeat the above, place the cylinder block on
wooden blocks so that the cutterheads are
clear of the floor.
Select a 10mm A/F hexagon key and unscrew
the 7 x caphead screws (41). Withdraw the
screws and lift the head clear of the cylinder
block. Take care when removing the cylinder
head as it weighs 16.4kg (36.0lbs), take
extreme care against trapping your fingers
when lifting and placing the cylinder head
down, use a hoist or other suitable lifting
equipment whenever possible. An eyebolt
(38) is supplied fitted to the cylinder head for
this purpose.
Removing Ball Valve from its mounting
Select two 32mm (1 1/4”) Spanners and
unscrew the hose (60) connector from the
lower ball valve adapter (55). Unscrew hose
fittings from ball valve unscrew the 4-nyloc