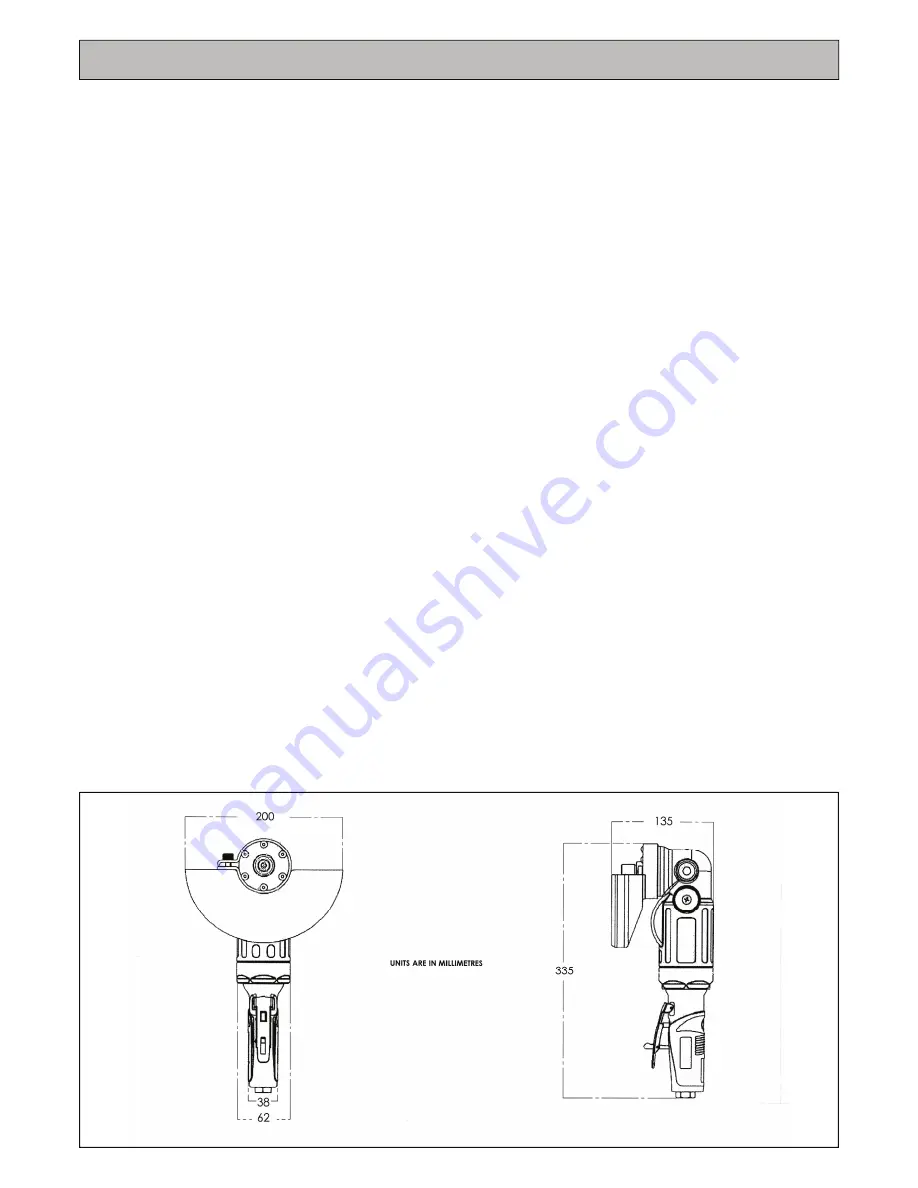
OPERATION
Putting into service
Remove plastic bung from air inlet using
a pair of pliers.
Use a clean lubricated air supply that will
give a measured air pressure to the tool
of 6.3bar (90psi). It is recommended a
air filter/regulator/lubricator is used which
can be obtained from air tool supplier.
Operating
With the grinder correctly connected to
the air supply, check the speed of the
grinder with an inlet pressure of 100
psi/7.0 bar measured at the tool inlet.
Check with a calibrated tachometer.
Check that the guard (53) is in position
and securely fixed.
Unsure that the grinding wheel is of the
correct dimensions, that it is not cracked
or chipped and has a permitted speed
rating
higher
than
the
maximum
permissible running speed of the grinder
which is 7,500 RPM.
When first starting the grinder with a new
or changed wheel fitted, the grinder
should first be started in a protected area,
i.e. such as under a heavy bench well
away from other persons and run for, say,
one minute.
This will provide protection if the wheel
should break because of a fault that was
not visibly detected
Always use eye protection and wear
protective gloves if there are sharp edges
in the working area.
Disconnect tool from air supply.
To dismantle, insert the peg spanner (63)
into disc nut (65/66) and with a spanner
(56) on the flats of gear shaft (51)
unscrew disc nut, take off disc and
unscrew disc receiver (64).
Check that it is screwed tightly to the shaft
and locates the bore of the grinding wheel
on the spigot of the disc receiver and
screw on disc nut item (65/66) using the
spanners provided. It should be tight
enough to prevent wheel spin off when
the air supply is shut off.
If you intend using the alternative
threaded hub grinding wheels with this
tool, the following procedure must be
followed.
1) Remove the rear, wheel mounting
flange (64). (65,66 & 67 not required)
2) Screw on the threaded Disc with the
hexagon boss at the rear face of the
wheel.
3) Hold the spindle with the spanner
provided and securely tighten the
wheel with a second wrench.
Only use threaded hub wheels certified
by the disc manufacturer
Handle the grinder with care.
If the grinder is dropped, carefully
examine the wheel for damage and
replace if necessary.
Start the machine as if for the first time of
fitting a wheel, i.e. under a bench.
Make sure the object to be ground is in a
firm fixed position.
The tool and the grinding process can
create a noise level such that ear
protectors should be worn.
If the grinding process creates a dust then
use a suitable breathing mask.
Check that the material being worked will
not cause harmful dust or fumes. If this is
so then special breathing apparatus may
be required. Seek advice before starting
work.
If the grinder vibrates when first fitting the
wheel or during use, remove from service
immediately and arrange for the fault to
be corrected before continuing to use.
Do not apply excessive pressure as this
will reduce the cutting efficiency.
Apply light loads and allow the wheel to
cut.
Replacement Grinding
Disc Instructions
Only personnel trained in the Abrasive
Wheels Regulations 1970 standard for the
correct fitting of grinding wheels must
maintain this tool.
PUWER 98, which covers the selection
and use of work equipment in general,
revoked the remaining provisions of the
Abrasive Wheels Regulations 1970
(these dealt with the training,
competence and appointment of people
to mount abrasive wheels).
See also ANSI B7.1 Safety code for the
use, care and protection of abrasive
wheels.This tool has an output shaft with
5/8-11 UNC threaded shaft.
Summary of Contents for 735.7075A
Page 1: ...Vibration Reduced 7 Angle Grinder Operation and Maintenance Manual www trelawnyspt co uk ...
Page 2: ......
Page 3: ......
Page 9: ...NOTES ...
Page 10: ...NOTES ...
Page 11: ...NOTES ...