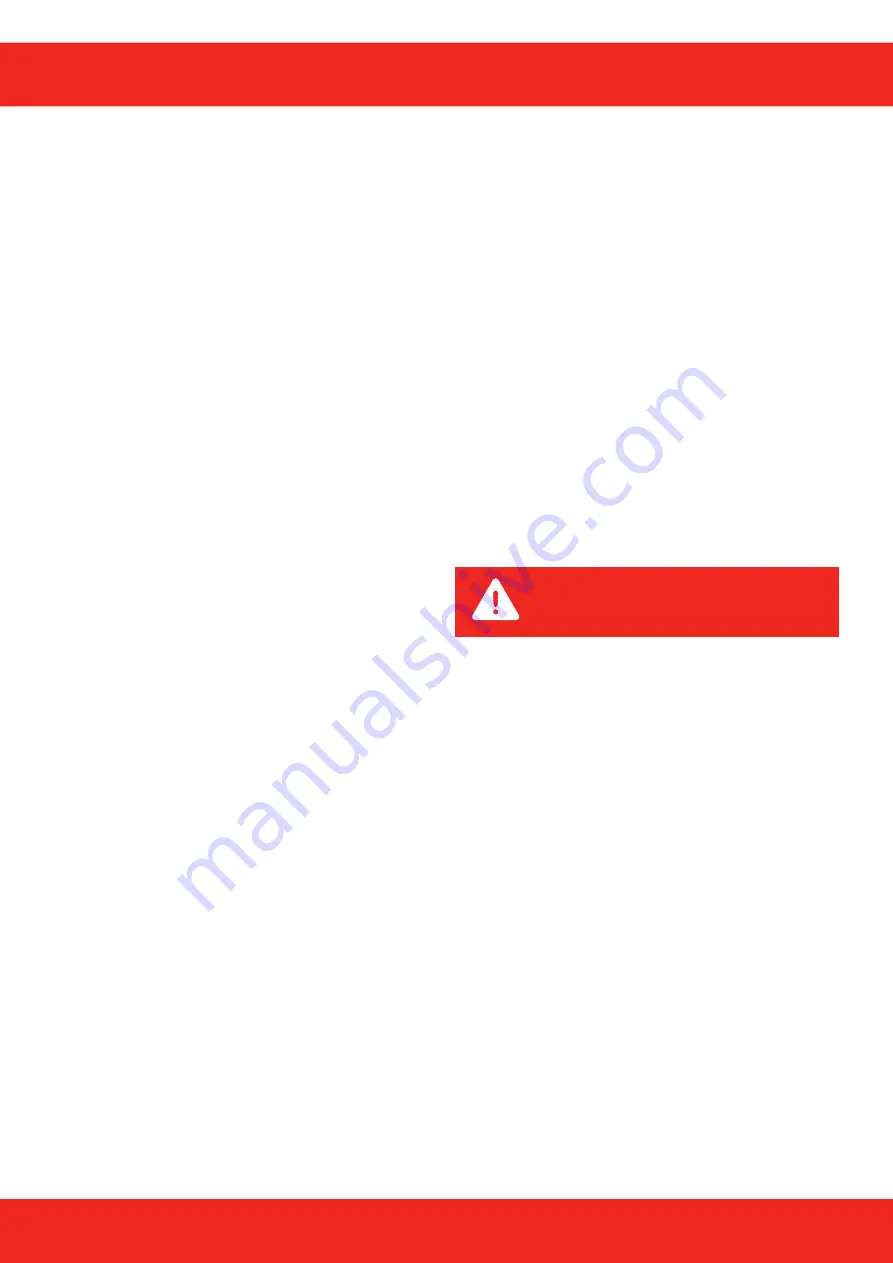
PAGE 8
VL203EX Needle Scaler
MAINTENANCE
Removing Needles
Disconnect from air supply, hold the Cover (10) in a vice using
the flats provided, keeping the tool horizontal, unscrew by
hand, the Front Tube assembly (30,31,32,33,34) complete
with Return Spring (32), Needles (31), and Needle Holder (30).
Check the condition of the Front Tube Locking O’Ring (25).
Take care not to invert the Needle Scaler while removing
the Front Tube (34) or the Piston (26) may fall out of the
Intermediate Tube (22). Remove the Needles from the Needle
Holder and dispose of the used Needles in an appropriate
manner.
Re-fitting the Needles
Insert the new needles into the Needle Holder location holes;
ensure that the Needles are inserted into the chamfered side
of the holes. Fit new Front Tube Locking O’Ring (25) to the
Intermediate Tube. Fit the Return Spring (32) over the needles
(31) and insert the Needle assembly into the Front Tube. Screw
the Front Tube assembly onto the intermediate Tube until
hand tight.
Recommended lubricants
Oil the tool daily during use. Put a few drops of one of the
following bio-degradable air tool lubricants through the
air inlet.
SHELL Naturelle HF
CASTROL Carelube HTG 22
Always use clean oil from a sealed container and ensure
ignition temperature is above 185Deg°.
Piston and Cylinder removal
Remove the Front Tube assembly (See Removing Needles)
Hold a clean lint free cloth over the open end of the
Intermediate Tube (22), remove from vice and tilt the Tube
downwards to remove the Piston (26). Secure the Cover (10) in
a vice with the Intermediate Tube in the vertical position, using
the flats provided. Use a suitable 6mm bar through the holes
provided, unscrew the Intermediate Tube anticlockwise.
Carefully remove the Intermediate Tube from the cover and
remove the Cylinder (15) from its location hole in the Cylinder
Guide Plate (12), which is fitted in the cover (10). The Cylinder
Guide Plate can be pulled out of the cover to gain access to
the Guide Plate Seal (13).
Cylinder Ball Valve replacement
This is a consumable item and will require replacing after
approximately 120 -160 hours use; this is dependent on the
cleanliness of the air supply and frequency of lubrication.
Do not replace this plastic ball with a steel version, as it will
invalidate the ATEX certification. Remove the ball retaining
O’Ring (18) from its groove just inside the bore of the cylinder
stem using a suitable pointed implement. Remove the ball (17)
from the bore, replace and refit new O’Ring into groove.
Piston Valve Pin replacement
Hold the piston (26) in a vice by the stem, using a pair of pliers
break off the valve pin (28), use a 6mm drill & bit and remove
the remainder from the piston. A small socket (4mm) which
just fits over the actual pin, will stop damage occurring. Drive
the valve pin in up to its shoulder using a vice or a small
hammer. Valve Body - Valve Stem removal Hold the Valve
Body (6) in a vice using the flats provided. Using a 3 mm
diameter punch, drive the Throttle Lever retaining Spring Pin
(8) out of the Valve Body (6) and withdraw the Throttle Lever
(7). Remove the Valve Cap (1) with O’Ring (2), Valve Spring (3),
Valve Stem (4) and the Valve Seat O’Ring (5).
Valve Body removal
Remove the Front Tube assembly (30,31,32,33,34)
as per instructions for Removing Needles. Replace the Front
Tube (34) without the Needles etc, onto the Intermediate Tube
(22) and screw up until hand tight. Clamp the Valve Body (6)
with its flats securely in a vice, with the Cover (10) uppermost.
Turn the tool anti-clockwise around the Valve Body by holding
the Cover and Front Tube, unscrew the Valve Body from the
handle until loose, remove from vice and finally unscrew
by hand. A vacuum shroud (42) is available (see parts list for
shroud and cuff) which fits over the front tube. Position the
front of the cuff (43) with the needle tips 15-20mm inside,
adjust as the needles wear. Tighten the caphead screw to
secure. Use a Trelawny recommended ATEX and HEPA
vacuum for 99.9% dust containment.
VERY IMPORTANT Before carrying out any dismantling,
ensuring the air supply is turned off,
Summary of Contents for VL203EX
Page 1: ...www trelawny co uk www trelawny co uk VL203ex NEEDLE SCALER operations and maintenance manual...
Page 10: ...PAGE 10 VL203EX Needle Scaler EXPLODED DIAGRAM...
Page 13: ...www trelawny co uk notes...
Page 14: ...PAGE 14 VL203EX Needle Scaler notes...
Page 15: ...www trelawny co uk notes...