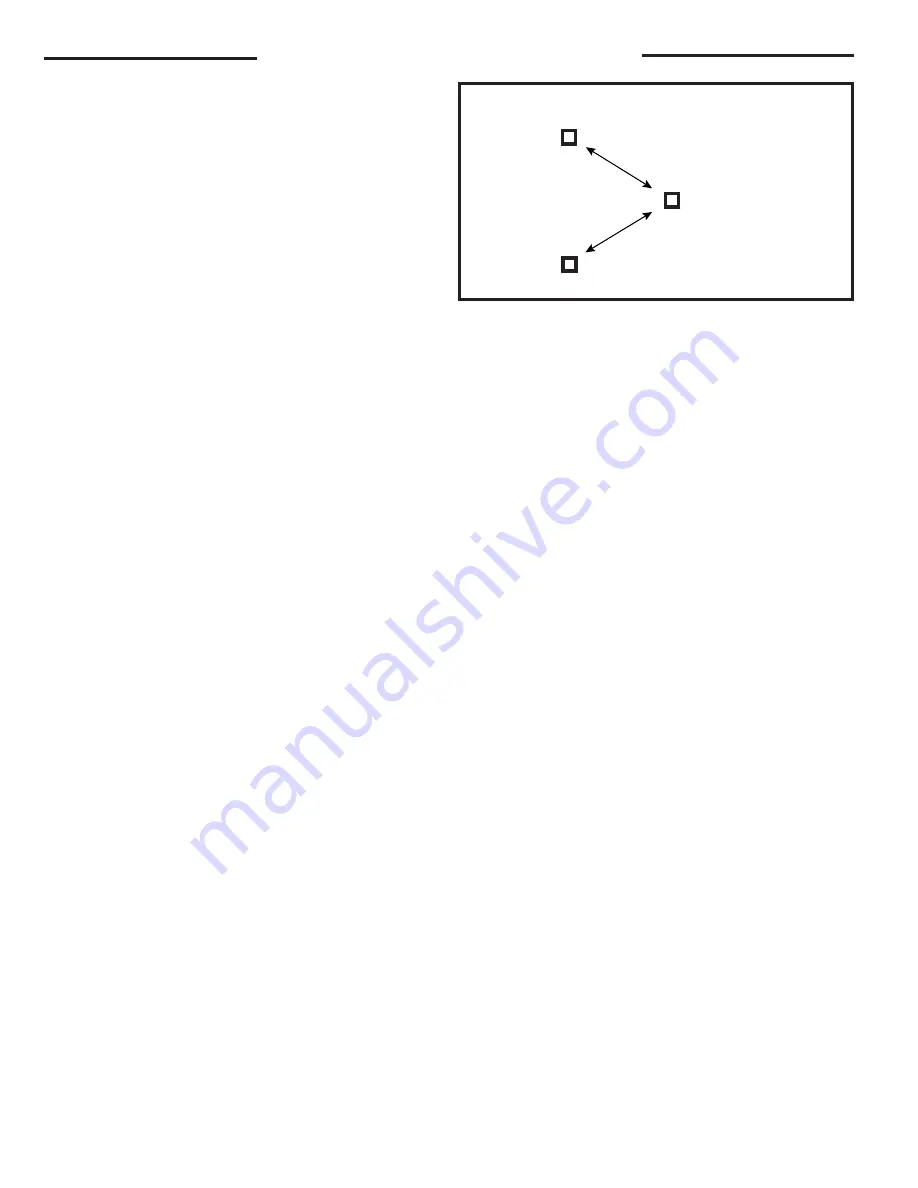
Page 16
FLASH RATE INDICATIONS:
1 — Flash/Second
= Normal operation.
2 — Flashes/Second
= Fault A (Low
∆
T) i.e.: Inoperative compressor, loss of charge, open ambient sensor, shorted coil sensor.
3 — Flashes/Second
= Fault B (20 defrosts terminated on time)
Fault C (High
∆
T) i.e.: SOV stuck in heating, shorted ambient sensor, open coil sensor, closed TXV,
OD motor failure, OD fan on in defrost, undercharged unit.
4 — Flashes/Second
= Fault A & C or A & B
For additional information consult Pub. No. 34-1001 Heat Pump Defrost Controls.
DEMAND DEFROST SYSTEM
PROCEDURE FOR TESTING SENSORS
Measure the temperature the subject sensor is exposed to. If the sensor is mounted on a
tube, place the lead on an Annie A-8 (or equiv.) temperature tester on the same tube near
the sensor and insulate the bulb.
Unplug the sensor and measure the resistance with a good quality ohmmeter (Simpson
260 or equiv.). Read the value as quickly as possible to prevent the meter current from
changing the resistance reading.
Using the chart on the right, locate (as close as possible) the actual sensor temperature.
The measured resistance should be relatively close to the resistance value shown in the
chart.
Example:
Sensor temp.
= 19°F.
Measured Resistance
= 46K ohms
This sensor is good since the measured value is relatively close to the
chart value.
TEMP °F
RESISTANCE
86
7.85K
81
8.85K
75
10.24K
70
11.59K
65
13.14K
59
15.32K
55
16.93K
50
19.41K
45
22.20K
41
24.76K
36
28.45K
32
31.84K
25
37.50K
19
46.44K
14
53.94K
10
57.64K
5
67.06K
0
78.05K
DEFROST CONTROL
The demand defrost control measures heat pump outdoor ambient
temperature with a sensor located outside the outdoor coil. A
second sensor located on the outdoor coil is used to measure the
coil temperature. The difference between the ambient and the
colder coil temperature is the difference or delta-T measurement.
This delta-T measurement is representative of the operating state
and relative capacity of the heat pump system. By measuring the
change in delta-T, we can determine the need for defrost. The coil
sensor also serves to sense outdoor coil temperature for termina-
tion of the defrost cycle.
FAULT DETECTION
A fault condition is indicated by the flashing light on the defrost
control inside the heat pump control box.
In normal operation, the defrost control light will flash once each
second. If the light is flashing more than once per second or not-at-
all, refer to the service manual for that unit.
PIN IDENTIFICATION (See Figure)
1. TEST_COMMON (Shorting any of the other pins to this pin
causes the function of the other pin to be executed. Leaving this
pin open results in the normal mode of operation.)
2. TST = Test (Shorting TEST_COMMON to this pin speeds up
all defrost board timings.)
3. FRC_DFT = Forced Defrost (Short TEST_COMMON to this pin
for two (2) seconds to initiate a forced defrost. Remove the short
after defrost initiates.)
▲
WARNING:
PIN IDENTIFICATION
FRC_DFT
TEST_COMMON
TST
DEFROST CONTROL CHECKOUT
Normal operation requires:
a. LED on board flashing 1 time/second.
b. 24V AC between R & B
c. 24V AC between Y & B with unit operating
d. Defrost initiation when FRC_DFT pin is shorted to
TEST_COMMON pin.
If a defrost control problem is suspected, proceed to DEMAND
DEFROST CONTROL CHECKOUT in this Service Facts.
Do NOT connect 24 VAC to T1
(ODS-A) terminal. ODS-A thermistor WILL BE BLOWN.