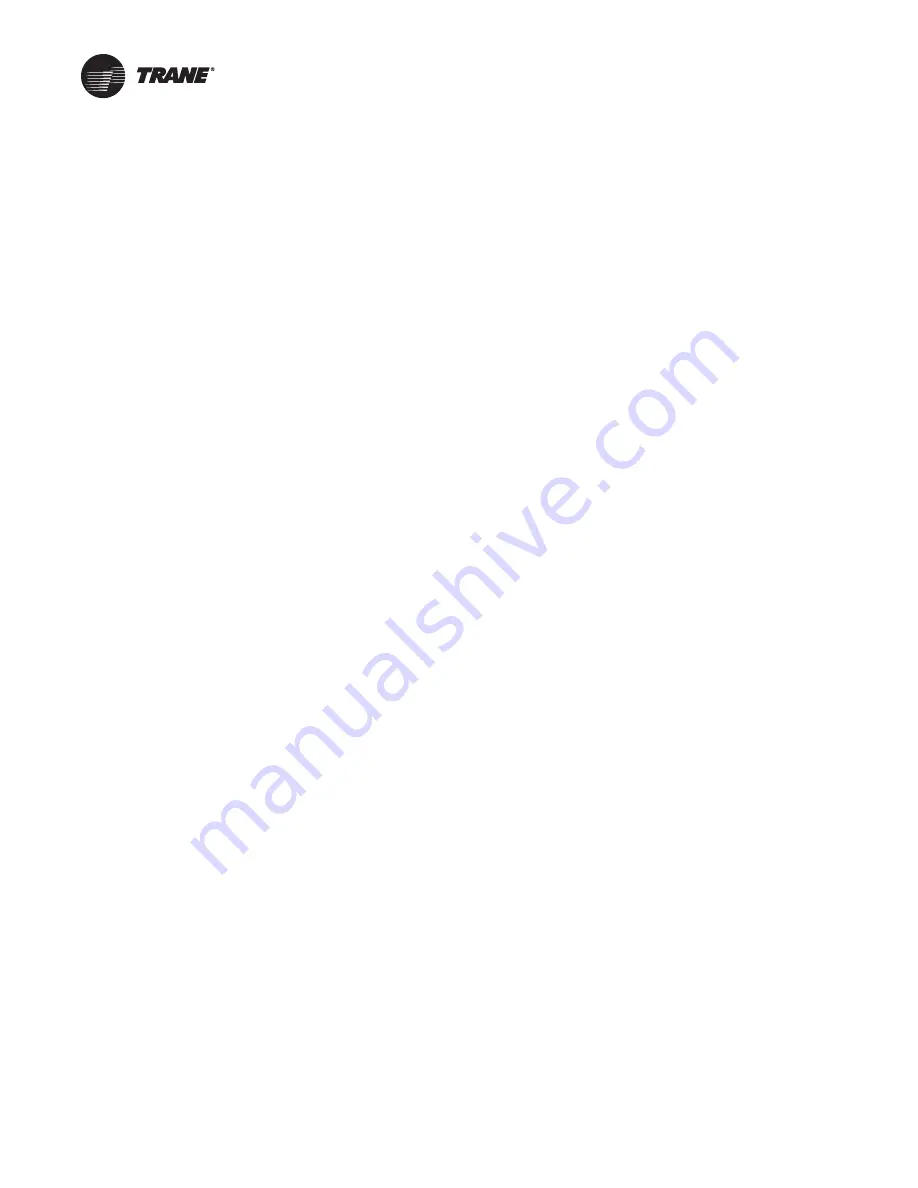
4
UNT-SVX07J-EN
Table of Contents
UniTrane™ Fan Coil/ Force Flo™ Cabinet
Heater
. . . . . . . . . . . . . . . . . . . . . . . . . . . . . . . . 5
UniTrane™ Fan Coil Low Vertical Model
. . 8
. . . . . . . . . . . . . . . . . . . . 10
. . . . . . . . . . . . . . . . . . . . . . . . . 11
. . . . . . . . . . . . . . . 11
. . . . . . . . . . . . . . . . . . . . . . 11
. . . . . . . . . . . . . . . . . . . . . . 12
. . . . . . . . . . . . . . . . 13
. . . . . . . . . . . . . . . . . . . . 13
. . . . . . . . . . . . . . . . . . . . . 14
. . . . . . . . . . . . . . . . . . . . . 15
. . . . . . . . . . . . . . . . . . . . . 41
. . . . . . . . . . . . . . . . . . . . . . . . . . . . 47
. . . . . . . . . . . . . . . . . . . . . . 48
. . . . . . . . . . . . . . . . 49
. . . . . . . . . . . . . . . . . . 49
. . . . . . . . . . . . . . . . . . . . . 50
. . . . . . . . . . . . . . . . . . . . . 52
. . . . . . . . . . . . . . . . . . 54
External Insulating Requirements
Balancing Manual Circuit Setter Valve
. . . . . . . . . . . . . . . . . . . 60
. . . . . . . . . . . . . . . . . 60
. . . . . . . . . . . . . . . . . 60
Electrical Grounding Restrictions
. . . . . . . . . . . . . . . . 60
. . . . . . . . . . . . . . . 65
. . . . . . . . . . . . . . . . . . . . . . . . . . . . 65
Electronically Commutated Motor (ECM)
VelociTach Motor Control Board
Installation and Initial Setup
. . . . . . . . . . . . . . . . . . . . . . . . . .72
. . . . . . . . . . . . . . . . . . . . . . . .75
. . . . . . . . . . . . . . . . . . . .80
. . . . . . . . . . . . . . . . . . . . . . .80
. . . . . . . . . . . . . . . . . .84
Tracer® ZN010 and ZN510 Controllers
Air-Fi® Wireless Communications System
89
. . . . . . . . . . . . . . . . . . . .91
. . . . . . . . . . . . . . . .92
. . . . . . . . . . . . . . . . . .95
. . . . . . . . . . . . . . . . . . . . .97
Wireless Sensor Specifications
. . . . . . . . . . . . . . . . . . .99
. . . . . . . . . . . . . . . . . . . . . . . . . . . . . . . .103
. . . . . . . . . . . . . . . . . .103
. . . . . . . . . . . . . . . . . . . . . . . . .104
Tracer® ZN010/ZN510 Controllers
. . . . . .104
. . . . . . . . . . . . . . . . . . .122
. . . . . . . . . . . . . . . .122
. . . . . . . . . . . . . . . . . . . . . . . . . . . .122
. . . . . . . . . . . . . . . . . . . . . . . . . . . . . . . .123
. . . . . . . . . . . . . . . . . . . . . . . . . . .125
. . . . . . . . . . . . . . . . . . . . . . . . . . . . . . . .127
Diagnostics and Troubleshooting
Servicing/Testing Wireless Zone Sensors
136
ZN010, ZN510, and ZN520 Controllers
. . .137
Summary of Contents for UniTrane
Page 163: ......