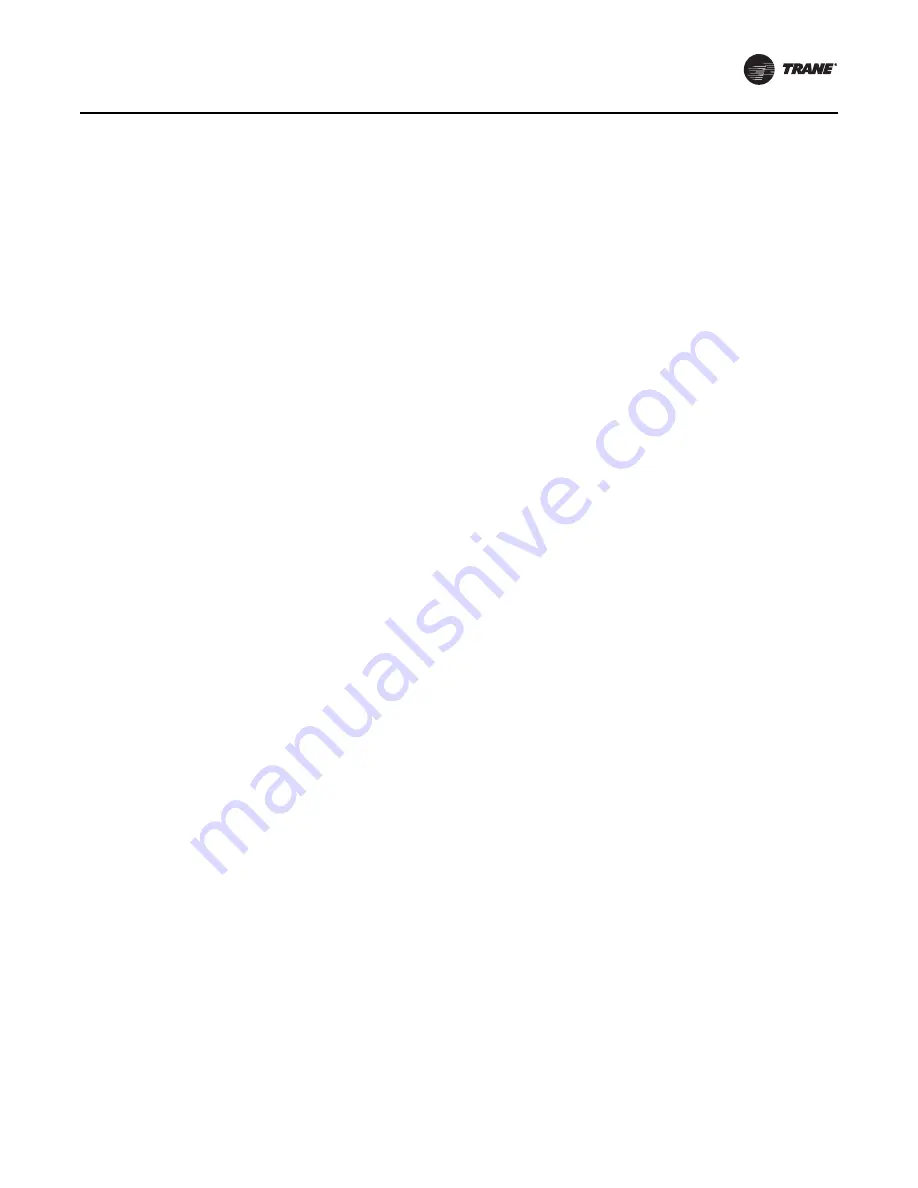
Sequence of Operations
ARTC-SVX002A-EN
47
bypass control regardless of the system pressure
differential between the supply and return headers.)
7. Once this minimum flow is established and the system
demand (based on leaving water/glycol temperature)
indicates that there is a requirement for cooling, the
lead compressor of the lead module will energize
provided all safeties of that refrigeration circuit are
satisfied.
8. Once there is a system load, the building management
system will modulate the system bypass decreasing
the bypass flow, as the flow rate through the fan coils
increases. This control is provided by the customer
external of the chiller but is presumed to be based on
the temperature of the water back to the chiller or the
pressure differential across the most remote fan coil
unit if it has a three-way valve.
9. As the system demand continues to increase, the
second compressor within that module will energize
provided all safeties on that circuit are satisfied.
10. As the system demand continues to increase, the
leaving water/glycol mixture temperature from the
chiller system will slowly increase until the differential
set point is reached. When the differential is reached, a
second module is brought on-line. The pump VFD
control must be set to ramp up quickly to provide
adequate water flow to both operating modules and
eliminate nuisance alarms such as low flow and low
pressure if there is not sufficient flow to the operating
modules.
11. As the flow and demand continue to increase, and the
temperature once again reaches the set point plus
differential setting, the second compressor on the
second module will energize. This operation continues
with all subsequent chiller modules as needed based
on system demand.
12. On a decrease in system demand (and flow) such that
the leaving water/glycol mixture temperature reaches
the set point minus the differential, a compressor will
de-energize. Once both operating compressors within
an operating module have de-energized, the
modulating valve will slowly close off flow to that
module. It is critical that the corresponding pump
variable frequency driver controller slowly ramp down
the speed of the pump to the next operating point so as
not to limit flow to the operating chillers as the valve
time to close is approximately 150 seconds.
13. This process occurs throughout the operating range of
the chiller system. At all “in-between” stages of
system capacity and demand balancing, the digital
scroll compressor on the client module will modulate
its capacity within the temperature control band limits
to maintain the leaving water temperature control as
tight as possible and to minimize the amount of
compressor cycling.
14. Should the client microprocessor fail, the balance of
the modules will continue to operate in response to
demand. If the chiller system is provided with a
redundant client microprocessor on a server chiller
module, all functions of the client microprocessor are
transferred to the redundant client microprocessor
should the client microprocessor fail.
15. The microprocessor control system in each chiller
module will close the electronic isolation valve within
that chiller module if there are alarms on both
refrigeration circuits within that module to prevent
flow from flowing through a non-active module which
causes an increase in the system flow and an
unnecessary increase in the number of chiller modules
to maintain the system set point.