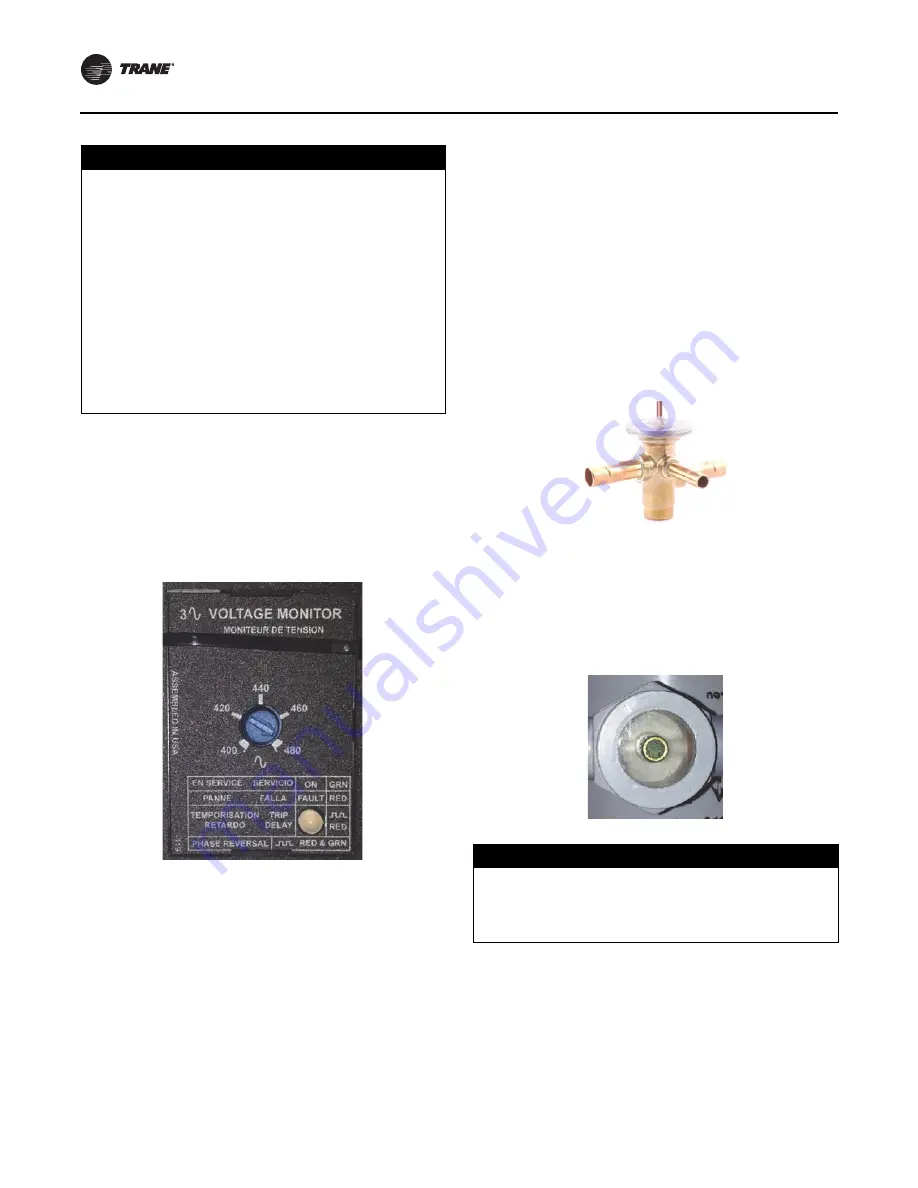
Controls Interface
44
ARTC-SVX002A-EN
Phase Monitor
A compressor can fail if operated in reverse for more than
a minute. A phase monitor is used on three phase power
systems to ensure that the electricity supplying the chiller
is configured appropriately. A phase monitor prevents a
motor from operating in reverse—if any of the three legs
of power are landed incorrectly—and will shut the system
down upon detection of a reversed phase condition.
Refrigeration Controls
Controls on the refrigeration system are designed to
provide safety for the major components and for proper
operation of the system.
Pressure transducers convert pressure into an electronic
signal that the microprocessor displays in pounds per
square inch (psi). Transducers vary in pressure ranges that
depend on the type of refrigerant used. Pressure
transducers are calibrated using the interface panel.
Temperature sensors transmit temperature data
electronically to the microprocessor for display in either
Fahrenheit (°F) or Celsius (°C). Temperature sensors are
calibrated using the interface panel.
Expansion Valve
An expansion valve is a metering device controlling the
flow of refrigerant to the evaporator based on evaporator
superheat.
Superheat is factory-set for around 12 °F (-11 °C). Close the
valve to increase superheat. To accurately read superheat,
install a temperature sensor at the evaporator outlet. The
sensor bulb should be located at the 4 o’clock or 8 o’clock
positions on the pipe for the most accurate pressure
measurement.
Ensure that the closed cell insulation covers the thermal
expansion valve sensing bulb. If insulation is missing, the
bulb will tend to feed more refrigerant to satisfy the
superheat setting.
Sight Glass
When the sight glass shows a green indicator, no moisture
is present. When the sight glass shows a yellow indicator,
there is moisture in the refrigerant line. Bubbles can be
observed whenever chiller cycling causes the pressure to
change up or down.
Low Pressure Bypass
Logic that uses a time delay that temporarily bypasses the
low-pressure switch for compressor start up. Once the
delay times out the normal controls are put back on line
within the control circuit.
NOTICE
Proof of Flow Switch!
Failure to provide flow switches or jumping-out of
switches could result in severe equipment damage.
Evaporator and condenser water circuits require proof
of flow switches.
•
Failure to include the proof of flow devices and/or
jumping out these devices could cause the unit to
stop on a secondary level of protection.
•
Frequent cycling on these higher level diagnostic
devices could cause excessive thermal and pressure
cycling of unit components (O-rings, gaskets,
sensors, motors, controls, etc.) and/or freeze
damage, resulting in premature failure of the chiller.
NOTICE
Equipment Damage!
Failure to remove moisture from system could cause
corrosion within the chiller/heater components, and
degrade performance.