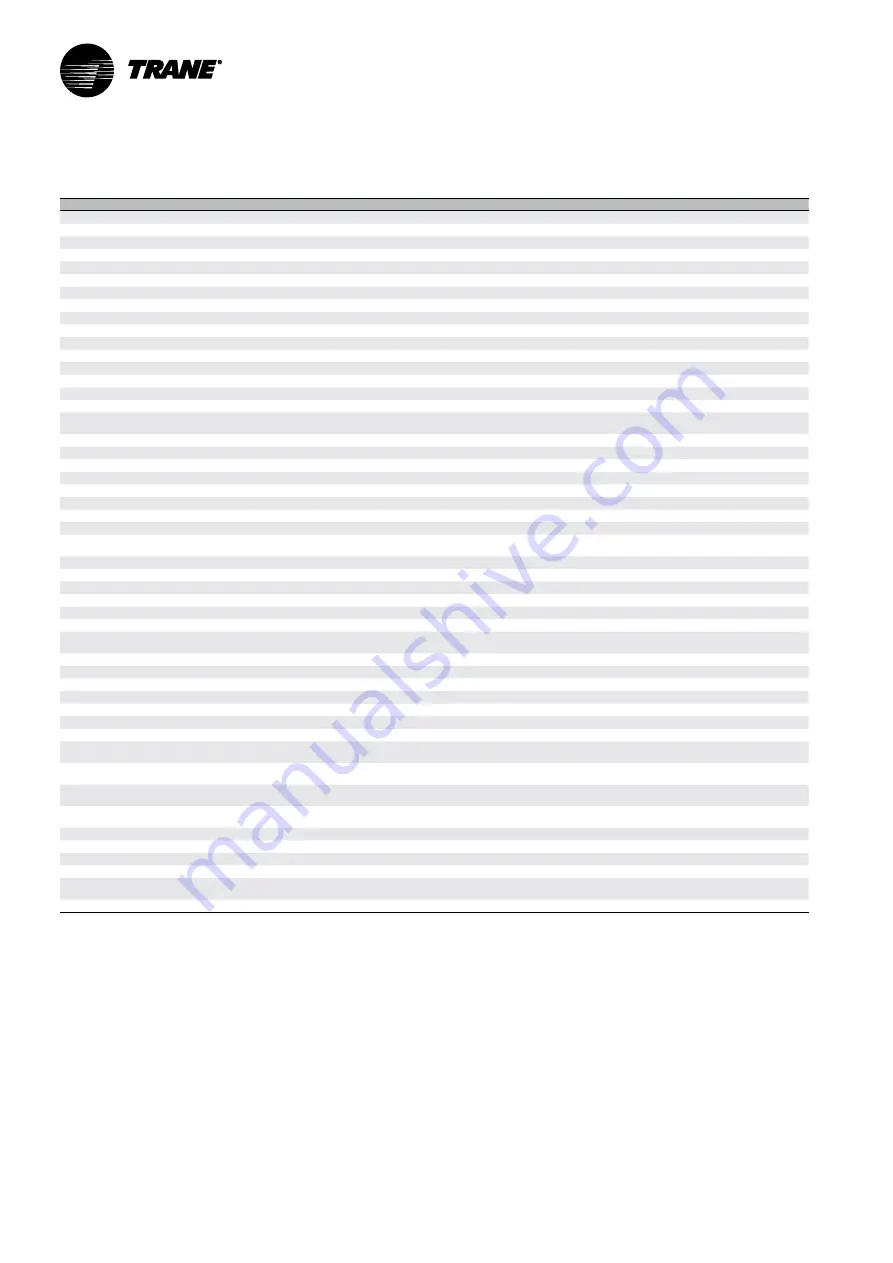
RT-SVX056D-GB
10
IC - IH 039
IC - IH 049
IC - IH 059
IC - IH 064
IC - IH 074
IC - IH 084
Energy Recovery Module (ERM)
Max Exhaust Air @ ESP=400Pa
m3/h
9500
9500
9500
9500
9500
9500
Max Fresh Air @ Wheel PD=300Pa
m3/h
18000
18000
18000
18000
18000
18000
Min Wheel Airflow
m3/h
2500
2500
2500
2500
2500
2500
Exchanger Wheel Diameter
mm
1200.0
1200.0
1200.0
1200.0
1200.0
1200.0
Exhaust Air Fan Diameter
mm
400.0
400.0
400.0
400.0
400.0
400.0
Exhaust Air Fan Motor Power
kW
3.4
3.4
3.4
3.4
3.4
3.4
Length x Width x Height
mm
1750x1180x1510
1750x1180x1510
1750x1180x1510
1750x1180x1510
1750x1180x1510
250x1180x1530
Weight
kg
375.0
375.0
375.0
375.0
375.0
455.0
Gas Burner
Gas burner type - Premium modulating
PCH045
PCH045
PCH065
PCH065
PCH080
PCH080
Thermal output (Hi) [Min-Max]
kW
8,50 - 42,0
8,50 - 42,0
12,40 - 65,0
12,40 - 65,0
16,40 - 82
16,40 - 82
Useful heat output [Min-Max]
kW
8,97 - 40,45
8,97 - 40,45
13,40 - 62,93
13,40 - 62,93
17,77 - 80,03
17,77 - 80,03
Gas Flow [Min-Max] (5)
m3/h
0,90 - 4,45
0,90 - 4,45
1,31 - 6,88
1,31 - 6,88
1,74 - 8,68
1,74 - 8,68
Flue gas emission
Carbon monoxide - CO - (0% of O2) (5)
ppm
<5
<5
<5
<5
<5
<5
Nitrogen oxides - NOx - (0% of O2) (5)
mg/KWh
-ppm
19 - 33
19 - 33
22 - 39
22 - 39
18 - 32
18 - 32
CO2 max (5)
%
9.1
9.1
9.1
9.1
9.1
9.1
Gas Connection Pipe Diameter
UNI/ISO 228/1-G 3/4" UNI/ISO 228/1-G 3/4" UNI/ISO 228/1-G 3/4" UNI/ISO 228/1-G 3/4" UNI/ISO 228/1-G 3/4" UNI/ISO 228/1-G 3/4"
Energy Recovery Circuit (ERC)
Cooling Mode
Net Cooling Capacity (ERC only)
kW
15.4
15.6
15.7
15.9
21.3
21.3
ERC Compressor Power Input
kW
3.7
3.7
3.7
3.7
4.1
4.1
ERC Exhaust Fans Power Input
kW
0.5
0.5
0.5
0.5
0.9
0.9
Total ERC Power Input
kW
4.2
4.2
4.2
4.2
5
5
Net Cooling Capacity
(ERC + IH standard)
kW
61.3
72.1
77.8
85.5
107.9
114.6
Total Power Input (ERC + IH standard)
kW
17.5
21.5
25.3
29.9
32.9
36.6
Heating Mode
Net Heating Capacity (ERC only)
kW
15.0
15
15
15
21
21.1
ERC Compressor Power Input
kW
2.4
2.3
2.3
2.3
2.7
2.7
ERC Exhaust Fans Power Input
kW
0.5
0.5
0.5
0.5
0.9
0.9
Total ERC Power Input
kW
2.9
2.8
2.8
2.8
3.6
3.6
Net Heating Capacity
(ERC + IH standard)
kW
53.6
63.3
69.5
79.3
93.3
100.3
Total Power Input (ERC + IH standard)
kW
14.2
17.2
19.9
22.8
24.4
27.2
Exhaust Fans & air management (7)
Number of Exhaust Fans
1
1
1
1
2
2
Exhaust Air Fans Type
Axial / AC
Axial / AC
Axial / AC
Axial / AC
Axial / AC
Axial / AC
Exhaust Air Fans Model
W4D450CO1401
W4D450CO1401
W4D450CO1401
W4D450CO1401
W4D450CO1401
W4D450CO1401
Exhaust Air Fans Diameter
mm
450
450
450
450
450
450
Minimum Fresh Air
%
20
20
20
20
20
20
Maximum Recommended Fresh Air
(compared to max airflow)
%
50
41
37
33
51
47
Maximum Fresh Air (building
pressurisation issues to be considered)
%
100
100
100
100
100
100
Maximum Return Air Pressure Drop
(without Return Roofcurb)
Pa
100
100
100
100
100
100
Maximum Additional Air Pressure Drop
(indoor coil)
Pa
10
15
15
20
20
20
Oil & Refrigerant (7)(6)
ERC Circuit Refrigerant Charge
kg
2.3
2.3
2.3
2.3
2.7
2.7
ERC Circuit Oil Quantity
l
1.24
1.24
1.24
1.24
1.24
1.24
Dimensiond and weights (7)(6)
Length x Width x Height
(ERC + IH standard)
mm
3010x2250x1565
3010x2250x1565
3010x2250x1565
3010x2250x1565
3890x2250x1585
3890x2250x1585
Weight (ERC + IH standard)
kg
1117
1134
1145
1145
1484
1496
(1) Indicative performances. For detailled performances, consult order write up (OWU).
(2) Under 400V/50Hz/3Ph.
(3) Electrical & system data are indicative and subject to change without notice. Please refer to unit nameplate data.
(4) Indicative data. For details consult lifting and handling instructions in document package shipped with the unit.
(5) Value referenced to Gas G20 - for other refer to burner IOM manual.
(6) OIL058E or OIL057E are European reference for POE oil and can be mixed in any proportion with OIL00078 or OIL00080 (same oil with US
reference on compressor nameplate).
(7) IH unit only.
(8) The ERM data is only for Digit -18 R.
IC - IH General Data
Table 1
–
Single compressor circuit (continued)