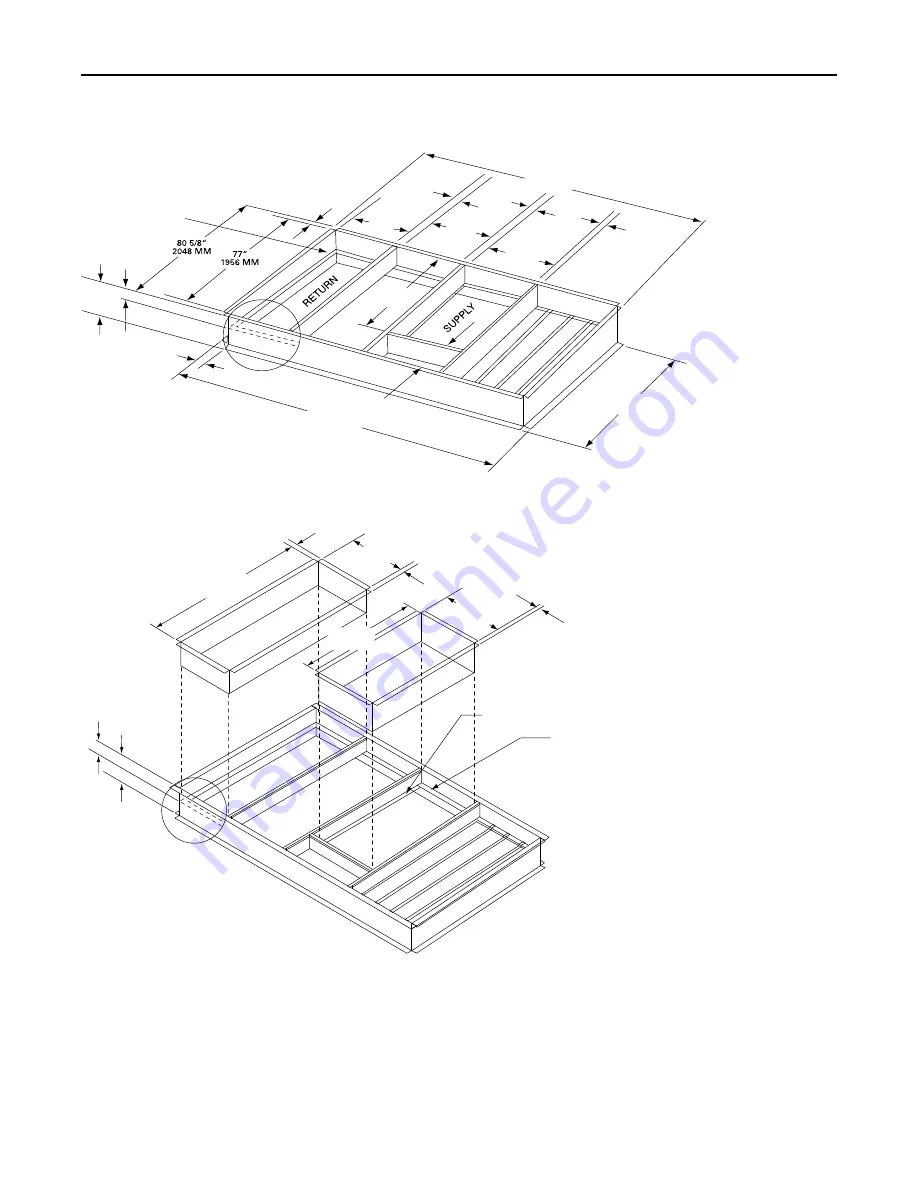
RT-SVX51L-EN
13
Figure 6.
Cooling with optional electrical heat — roof crub
117 3/16”
2977 MM
7 1/2”
191 MM
81”
2057 MM
1”
25 MM
1”
25 MM
116 7/8”
2969 MM
28 9/16”
725 MM
23 1/4”
591 MM
22 1/4”
565 MM
1”
25 MM
1 13/16”
46 MM
1 1/2” (38 MM) PERIMETER
CURB FLANGE
7 7/6”
189 MM
14 1/16”
357 MM
2”
51 MM
69 1/2”
1765 MM
Figure 7.
Cooling with optional electrical heat — downflow duct connections—field fabricated
1”
25.4 MM
CURB FLANGE
LONG SIDES
14 1/16”
357 MM
7 7/16”
189 MM
73 7/16”
1865 MM
1”
25 MM
19 5/16”
491 MM
1”
25 MM
26 5/16”
668 MM
1”
25 MM
1 1/2”
38 MM
CURB FLANGE
SHORT SIDES
66 1/2”
1689 MM
RE
TURN
SUPPL
Y
NOTES:
• DUCT FLANGES MOUNT 7-7/16” DOWN INSIDE THE CURB ON THE 1-1½” CURB FLANGES.
• ROOFCURB IS INTENDED FOR DOWNFLOW USE ONLY.