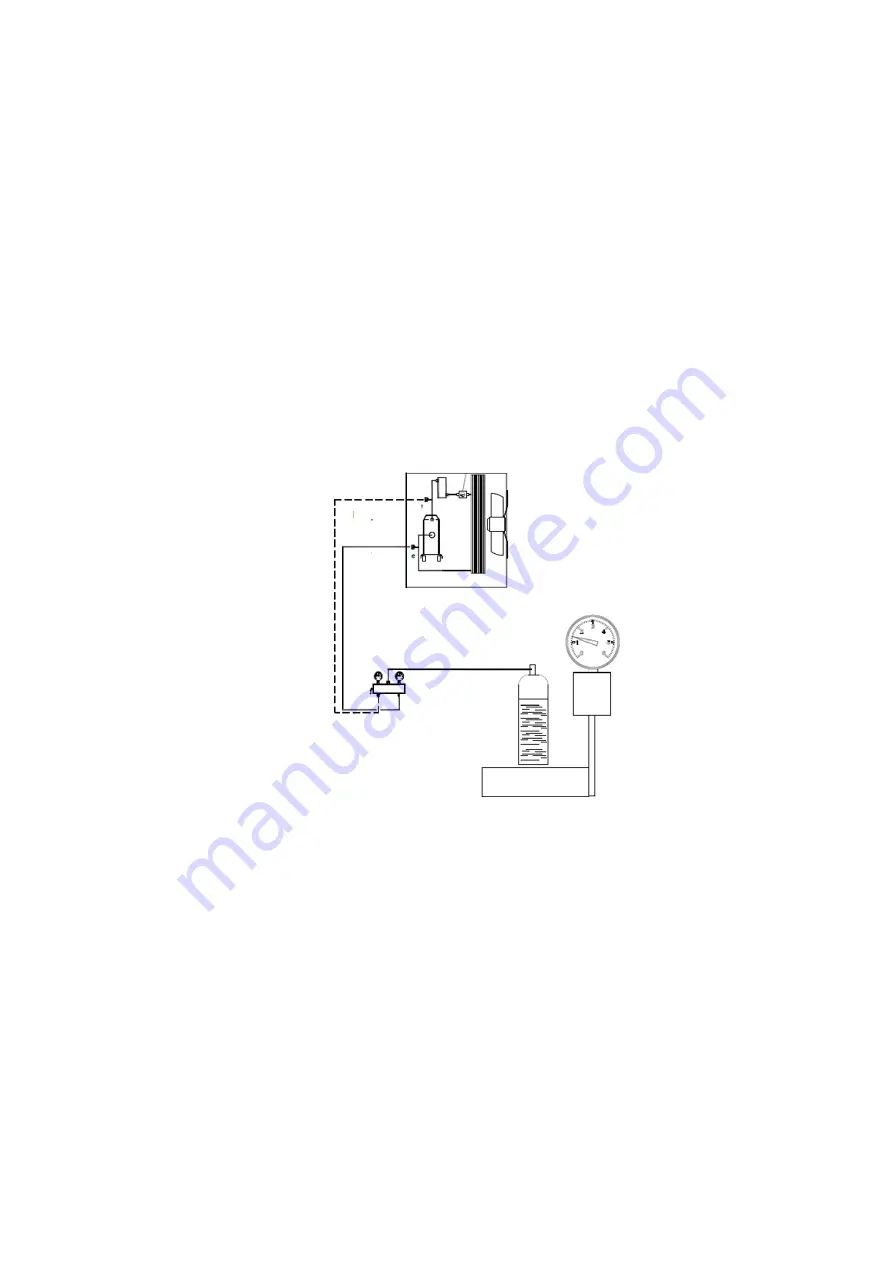
12.1.2
Refrigerant replacement procedure with unit running (refrigerant charge in the vapour phase)
Caution: charge vapour only. Do not charge liquid because it may damage the compressor.
Connect the refrigerant cylinder to the service valve without tightening the coupling. Drain the connection piping and
tighten the coupling. Charge the circuit until the indicator indicates liquid without bubbles. Now the unit has the
required charge. Make sure not to overcharge the circuit. Charging more than necessary leads to a higher delivery
pressure, greater power consumption and possible damage to the compressor.
The symptoms of a low refrigerant charge are:
Low evaporation pressure.
High value of superheating.
Low value of sub cooling.
In this case, add refrigerant R410A. The system is provided with a charging port between the expansion valve and the
evaporator. Charge refrigerant until conditions return to work normal. Remember to replace the cap closing the valve
at the end.
IMPORTANT!
If the unit has not been provided with integrated pump on board, do not turn off the external pump before 3 minutes
have elapsed after turning off the last compressor. The early shutdown of the pump causes a water flow alarm failure.
13
START-UP
13.1
PRELIMINARY CONTROLS
Before starting up the equipment it is very important to check that all the operations described in the paragraph
“CHECK LIST – MANDATORY OPERATION CONTROL BEFORE START UP” have been carried out correctly.
Moreover check that all the mechanical and electric equipment has been tightened perfectly. Particular attention
should be paid to the main components (compressor, exchangers, ventilators, electrical motors, and pump) if loose
fastenings are found, tighten them well before starting up the machine.
The oil heaters have to be inserted at least 8 hours before starting up. Ensure that the compressors’ carter is hot. Open
the compressor valve and the cooling circuit one, which may have been shut for charging. Control all the machinery
connected to the unit.
Refrigerant charge in the vapour phase
Liquid sight glass
HR port
LP port
HP gauge
LP gauge
Scale
Gauge manifold