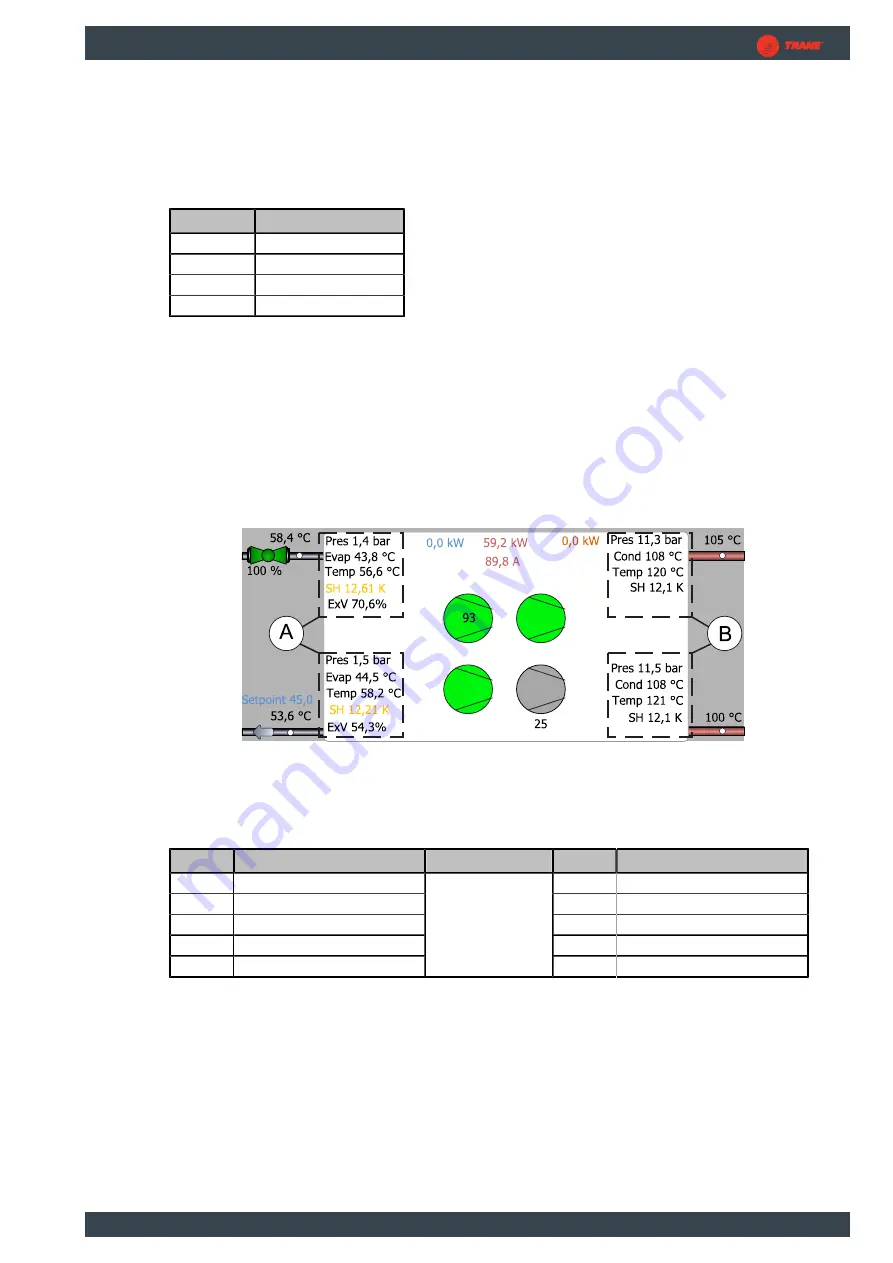
Compressors
Each compressor's current power is expressed as a percentage (shown as a number
inside the compressor's icon). The compressor color codes are shown in the table
below.
Color
Status
Grey
Not ready to start
White
Ready to start
Green
Running
Blinking red
Alarm
If a compressor has a restart delay (greater than 0), the delay is displayed under the
compressor’s icon.
To view a compressor’s motor status, tap on the compressor’s icon. The
Motor status
popup will be discussed in section
Viewing motor status
.
Key process values
Process screen center ver. 3
A number of key process values are shown in the center of the process view.
A
Cold side values
B
Warm side values
Pres
Suction pressure
Pres
Discharge pressure
Evap
Evaporating pressure
Cond
Condensating temperature
Temp
Suction temperature
Temp
Discharge temperature
SH
Suction superheat
SH
Discharge superheat
ExV
Expansion valve opening, %
Accessing setting views
To access different settings views, open the
Process
view and tap on one of the
buttons in the bottom button row (see the figure below). These views are also displayed
when the Startup Assistant is active (during the first start-up, for example). The views
will be discussed in following chapters.
EXES01 2150EN
47 (66)