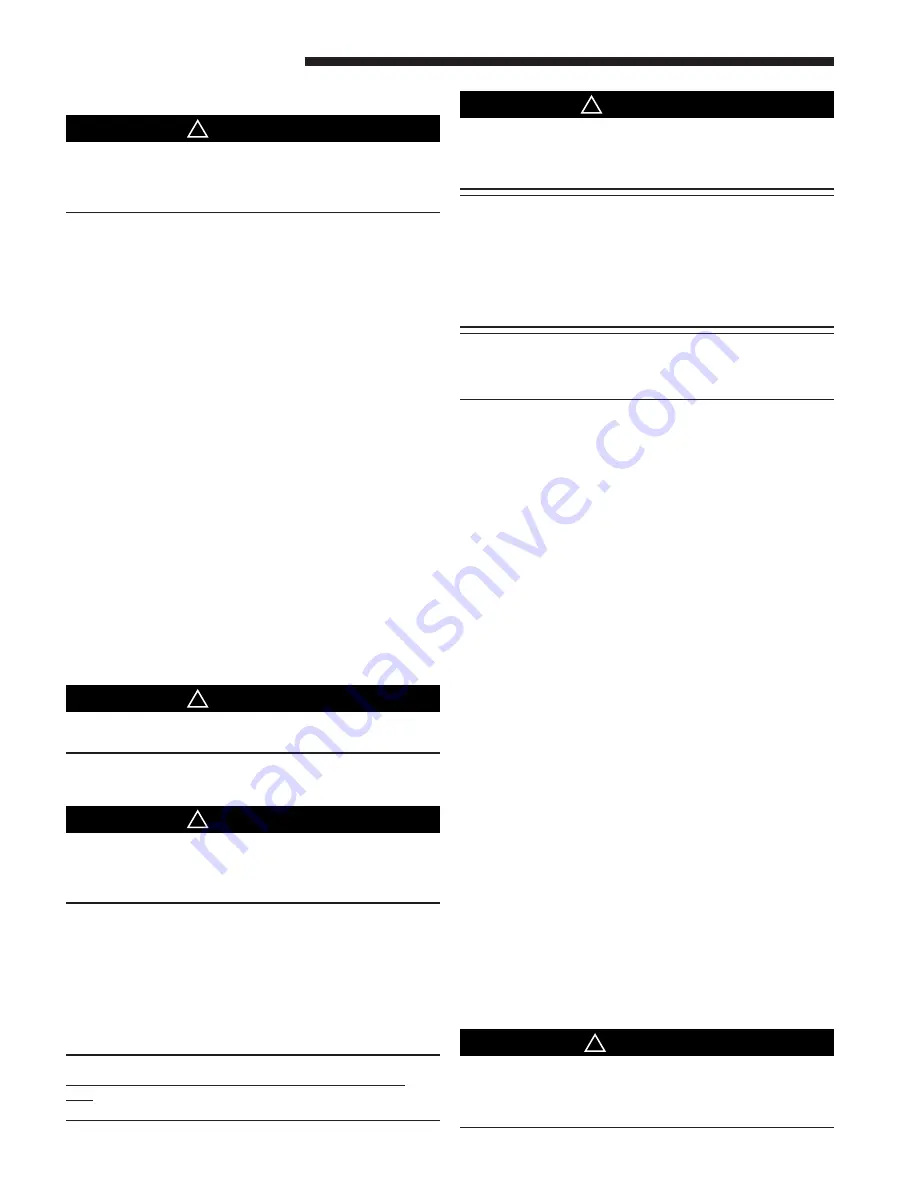
10
UH1-DH1-SF-1L
Service Facts
PERIODIC SERVICING REQUIREMENTS
▲
WARNING
!
Disconnect power to the unit before removing the blower
door.
Failure to follow this warning could result in personal
injury from moving parts.
1. GENERAL INSPECTION –
Examine the furnace
installation annually for the following items:
a. All flue product carrying areas external to the fur-
nace (i.e. chimney, vent connector) are clear and free
of obstruction. A vent screen in the end of the vent
(flue) pipe must be inspected for blockage annually.
b. The vent connector is in place, slopes upward and is
physically sound without holes or excessive corro-
sion.
c. The return air duct connection(s) is physically
sound, is sealed to the furnace and terminates out-
side the space containing the furnace.
d. The physical support of the furnace should be sound
without sagging, cracks, gaps, etc., around the base
so as to provide a seal between the support and the
base.
e. There are no obvious signs of deterioration of the fur-
nace.
2. FILTERS – Filters should be cleaned or replaced (with
high velocity filters only), monthly and more frequently
during high use times of the year such as midsummer
or midwinter.
3. BLOWERS – The blower size and speed determine the
air volume delivered by the furnace. The blower mo-
tor bearings are factory lubricated and under normal
operating conditions do not require servicing. If motor
lubrication is required it should only be done by a
qualified servicer. Annual cleaning of the blower wheel
and housing is recommended for maximum air output,
and this must be performed only by a qualified servicer
or service agency.
▲
WARNING
!
Do NOT touch igniter. It is extremely hot.
Failure to follow this warning could result in severe burns.
4. IGNITER – This unit has a special hot surface direct igni-
tion device that automatically lights the burners. Please
note that it is very fragile and should be handled with care.
▲
WARNING
!
CARBON MONOXIDE POISONING HAZARD
Failure to follow the service and/or periodic maintenance
instructions for the furnace and venting system, could
result in carbon monoxide poisoning or death.
5. BURNERS – Gas burners do not normally require
scheduled servicing, however, accumulation of foreign
material may cause a yellowing flame or delayed igni-
tion. Either condition indicates that a service call is
required. For best operation, burners should be cleaned
annually by a qualified servicer.
Turn off gas and electric power supply. To clean burn-
ers, remove burner box cover (6 to 8 screws) and the top
burner bracket. Lift burners from orifices.
NOTE:
Be careful NOT to break igniter when removing burn-
ers. Clean burners with brush and/or vacuum cleaner.
Reassemble parts by reversal of the above procedure.
▲
WARNING
!
CARBON MONOXIDE POISONING HAZARD
Failure to follow the service and/or periodic maintenance
instructions for the furnace and venting system, could
result in carbon monoxide poisoning or death.
NOTE:
On LP (propane) units, some light yellow tipping of the
outer mantle is normal. Inner mantle should be bright
blue.
Natural gas units should not have any yellow tipped
flames. This condition indicates that a service call is
required. For best operation, burners should be cleaned
annually by a qualified servicer.
NOTE:
On LP (propane) units, due to variations in BTU content
and altitude, servicing may be required at shorter inter-
vals.
6. HEAT EXCHANGER/FLUE PIPE –
These items must
be inspected for signs of corrosion, and/or deterio-
ration at the beginning of each heating season by
a qualified service technician and cleaned annu-
ally for best operation. To clean flue gas passages,
follow recommendations below:
a. Turn off gas and electric power supply.
b. Inspect flue pipe exterior for cracks, leaks, holes or
leaky joints. Some discoloration of PVC pipe is nor-
mal.
c. Remove burner compartment door from furnace.
d. Inspect around insulation covering flue collector
box. Inspect induced draft blower connections from
recuperative cell and to the flue pipe connection.
e. Remove burners. (See 5.)
f. Use a mirror and flashlight to inspect interior of
heat exchanger, be careful not to damage the igniter,
flame sensor or other components.
g. If any corrosion is present, contact a service agency.
Heat exchanger should be cleaned by a qualified
service technician.
h. After inspection is complete replace burners, and all
furnace doors.
i. Restore gas supply. Check for leaks using a soap
solution. Restore electrical supply. Check unit for
normal operation.
7. FURNACE CONDENSATE DRAIN TUBES – Conden-
sate drain tubes must be checked periodically to assure
that condensate can flow freely from unit to drain. If
a drain problem cannot be corrected, call a qualified
servicer.
8. COOLING COIL CONDENSATE DRAIN – If a cooling
coil is installed with the furnace, condensate drains
should be checked and cleaned periodically to assure
that condensate can drain freely from coil to drain. If
condensate cannot drain freely water damage could oc-
cur. (See Condensate Drain in Installer’s Guide.)
▲
CAUTION
!
Label all wires prior to disconnection when servicing
controls. Wiring errors can cause improper and dangerous
operation.
Verify proper operation after servicing.
Summary of Contents for DH1B040A9241C Series
Page 6: ...6 UH1 DH1 SF 1L Service Facts continued on next page WIRING DIAGRAM From Dwg D345803P01 Rev A...
Page 7: ...UH1 DH1 SF 1L Service Facts 7 SCHEMATIC DIAGRAM From Dwg D345803P01 Rev A...
Page 8: ...8 UH1 DH1 SF 1L Service Facts continued on next page WIRING DIAGRAM From Dwg D345804P01 Rev A...
Page 9: ...UH1 DH1 SF 1L Service Facts 9 SCHEMATIC DIAGRAM From D345804P01 Rev A...
Page 18: ...18 UH1 DH1 SF 1L Service Facts...