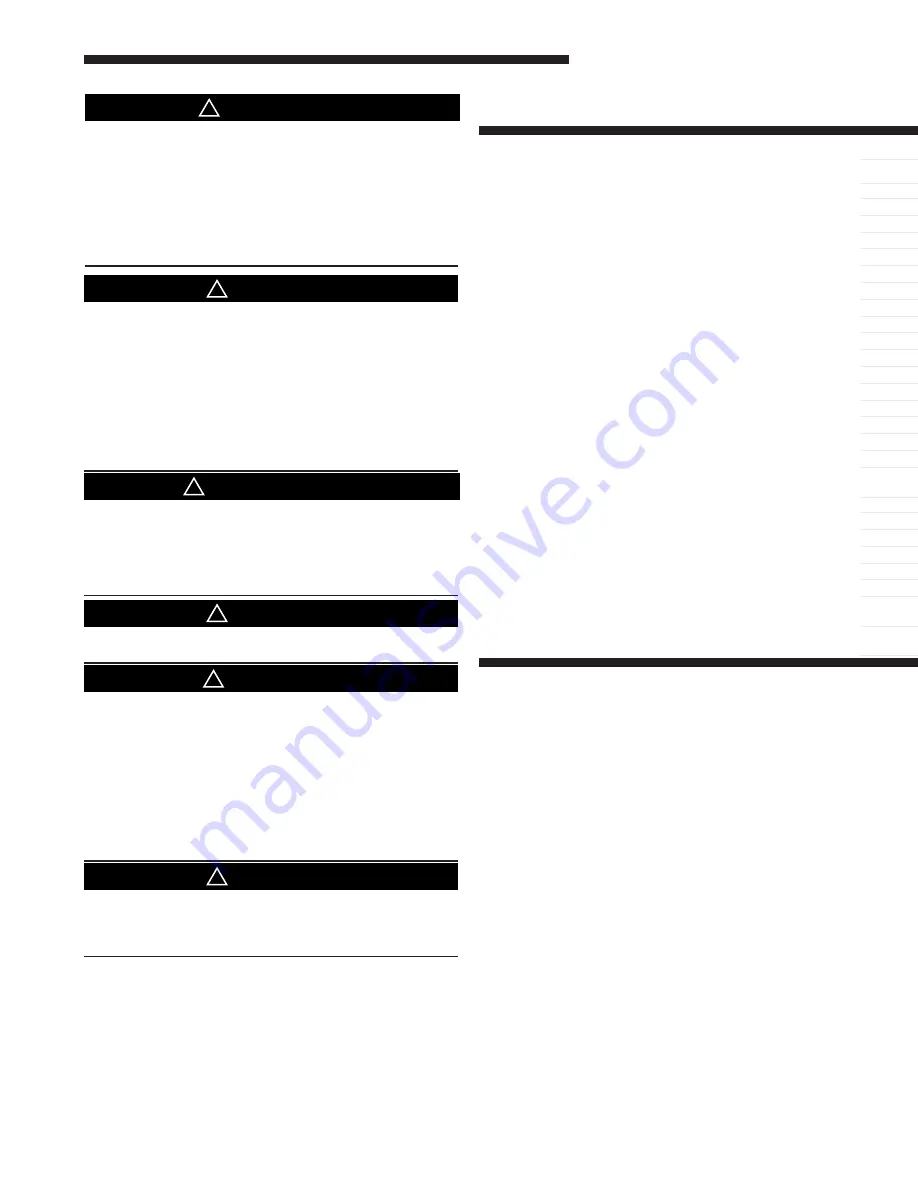
18-CD32D1-3
3
Installer’s Guide
Safety Section
2
Installation Instructions
4
General Installation Instructions
4
Location and Clearances
4
Outline Drawing
5-6
Upflow Installation
7
Downflow Installation
7
Horizontal Installation
7
Air for Combustion and Ventilation
9
Duct Connections
10
Return Air Filters
12
General Venting Instructions
15
Venting into a Masonry Chimney
15
Electrical Connections
17
Field Wiring Diagrams
17-20
Gas Piping
22
Combustion and Input Check
22
Gas Valve Adjustment
23
High Altitude Derate
24
Start Up and Adjustment
25
Preliminary Inspections
25
Lighting Instructions
25
User Interface menu - Communicating Mode
27
User Interface menu - 24 VAC Mode
28
Sequence Of Operation
29
Control and Safety Switch Adjustment
32
Conditions Affecting Furnace Operation
33
Furnace Alert Codes
35
Contents
The following safety practices and precautions must be
followed during the installation, servicing, and operation of
this furnace.
1. Use only with the type of gas approved for this furnace.
Refer to the furnace rating plate.
2. Install this furnace only in a location and position as
specified in “Location and Clearances” (page 4), of these
instructions.
3. Provide adequate combustion and ventilation air to the
furnace space as specified in “Air for Combustion and
Ventilation” (pages 9), of these instructions.
4. Combustion products must be discharged outdoors.
Connect this furnace to an approved vent system only,
as specified in the “Venting” section (pages 15-16), of
these instructions.
5. Never test for gas leaks with an open flame. Use a
commercially available soap solution made specifically
for the detection of leaks to check all connections, as
specified in “Gas Piping” (page 22) of these instruc-
tions.
6. Always install the furnace to operate within the fur-
nace’s intended temperature-rise range with a duct sys-
tem which has an external static pressure within the
allowable range, as specified on the unit rating plate.
Airflow with temperature rise for cfm versus static is
shown in the Service Facts accompanying this furnace.
7. When a furnace is installed so that supply ducts carry
air circulated by the furnace to areas outside the space
containing the furnace, the return air shall also be
handled by a duct(s) sealed to the furnace casing and
terminating outside the space containing the furnace.
8. A gas-fired furnace for installation in a residential
garage must be installed as specified in “Location and
Clearances” section (page 4) of these instructions.
▲
CAUTION
!
Do not install the furnace in a corrosive or contaminated
atmosphere.
▲
WARNING
!
SAFETY HAZARD
Do not install the furnace directly on carpeting, tile or
other combustible material other than wood flooring.
For vertical downflow application, subbase (BAY-
BASE205) must be used between the furnace and
combustible flooring. When the downflow furnace is
installed vertically with a cased coil, a subbase is not
required. Failure to follow this warning could result
in property damage, personal injury or death.
▲
CAUTION
!
LABELING WIRES!
Label all wires prior to disconnection when servicing con-
trols. Wiring errors can cause improper and dangerous
operation. Verify Proper Operation after servicing.
▲
CAUTION
!
To prevent shortening its service life, the Furnace
should NOT be used as a “Construction Heater”
during the finishing phases of construction until the
requirements listed in item 9, a-i of the safety sec-
tion of this publication have been met. Condensate
in the presence of chlorides and fluorides from paint,
varnish, stains, adhesives, cleaning compounds,
and cement create a corrosive condition which may
cause rapid deterioration of the heat exchanger.
▲
WARNING
!
SAFETY HAZARD
DO NOT USE SEMI-RIGID METALLIC GAS CONNEC-
TORS (flexible GAS lines) within the Furnace cabinet.
Failure to follow this warning could result in property
damage, personal injury or death.
▲
WARNING
!
EXPLOSION HAZARD
NEVER USE AN OPEN FLAME TO DETECT GAS
LEAKS. EXPLOSIVE CONDITIONS MAY OCCUR.
USE A LEAK TEST SOLUTION OR OTHER AP-
PROVED METHODS FOR LEAK TESTING. FAIL-
URE TO FOLLOW THIS WARNING COULD RESULT
IN PROPERTY DAMAGE, PERSONAL INJURY OR
DEATH.