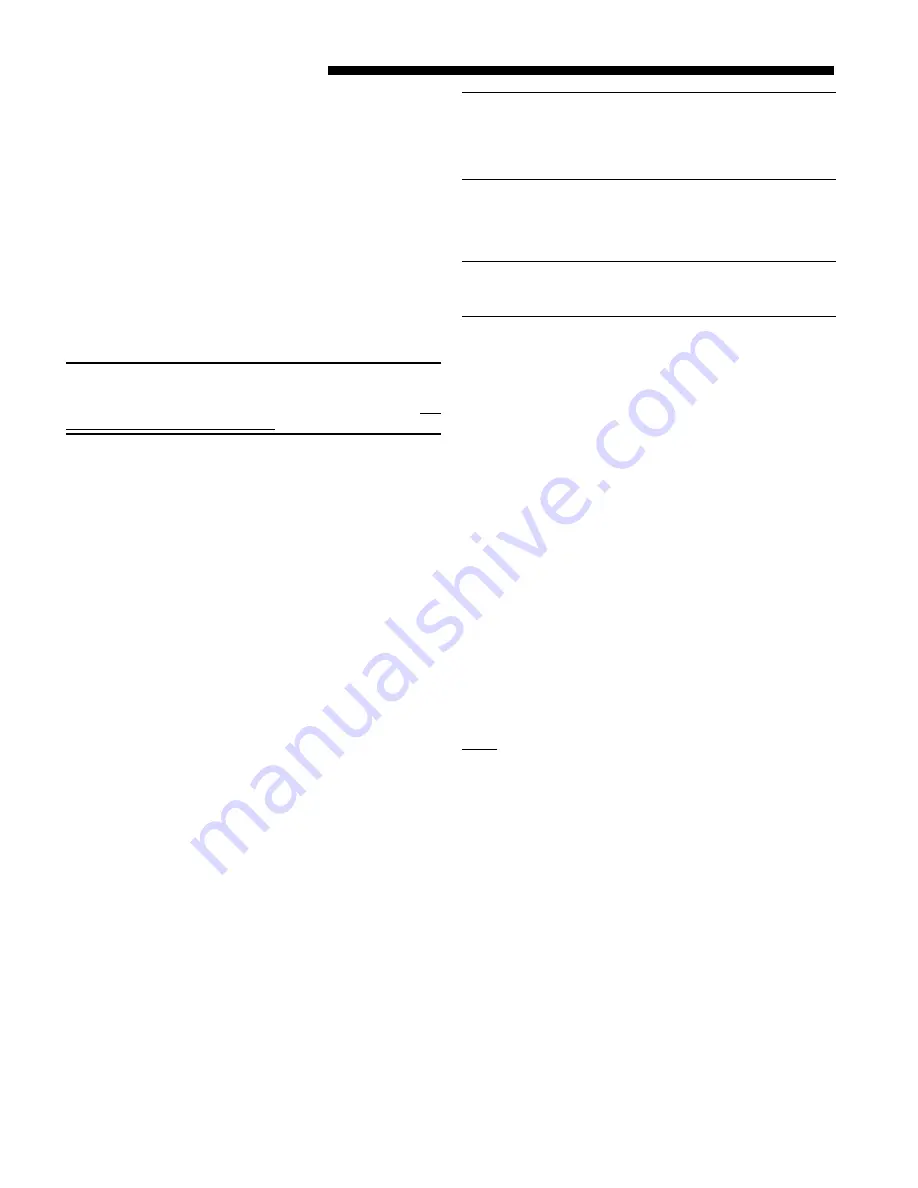
12
18-CD25D1-2
Installer’s Guide
IMPORTANT:
These Furnaces may be installed as Direct Vent (sealed
combustion) or as Nondirect Vent (single pipe). The Fur-
naces are shipped
DIRECT VENT
with sealed combus-
tion.
For
DIRECT VENT APPLICATION:
The Furnaces
must be vented to the exterior of the house and com-
bustion air MUST come through the inlet air pipe
FROM OUTSIDE AIR.
NOTE: BAYVENT200* accessories can be used for inlet
and outlet terminals when the pipes do not exit the
structure together.
For
NON-DIRECT VENT APPLICATION:
The Fur-
nace shall be vented to the exterior of the house, but
combustion air may enter from the surrounding area
as long as combustion air requirements are met.
(See AIR FOR COMBUSTION AND VENTILATION)
FURNACE VENT/ INLET PIPE INSTALLATION
There are many different variations of the vent/ inlet
air pipe combination. The vent/ inlet air combination
used for installation of these Furnaces depends on the
needs of the location. However, these guidelines must
be followed:
1. The Furnace must vent outside the structure.
2. Furnace combustion air requirements must be met
for non-direct, single pipe applications.
3. For direct vent application of these Furnaces, the
vent pipe and air inlet pipe do not have to exit in
the same air space or even on the same surface of
the structure.
However, the longest individual pipe
will decide the value for the longest allowable
equivalent vent/ inlet air length as shown in the
vent length table on page 14.
The following are
EXAMPLES ONLY
:
EX. 1 —
Example 1 shows that the vent may go vertical while
the inlet air may be on any side of the structure. The
vent pipe would decide the maximum equivalent length
for the pipe depending on the furnace and pipe size.
VENT FITTING MATERIAL – PLASTIC
Gas and liquid tight single wall vent fittings, designed
for resistance to corrosive flue condensate, MUST be
used throughout.
Listed in Table 4 are 2" and 3" size fittings that meet
these requirements. The materials listed are various
grades of PVC and ABS plastic.
PIPE JOINTS: All joints must be fastened and sealed
to prevent escape of combustion products into the build-
ing.
The recommended system is assembled from 2", 2-1/2",
or 3" plastic pipe and fittings (See Table 4, page 12).
Where the system is routed to the outdoors through an
existing masonry chimney containing flue products from
another gas appliance, or where required by local codes,
then 3" venting of Type 29-4C stainless steel must be
used in place of PVC material.
These Furnaces have been classified as CATEGORY IV
Furnaces in accordance with ANSI Z21.47 “latest edi-
tion” standards. Category IV Furnaces operate with
positive vent pressure and with a vent gas temperature
less than 140°F above the dewpoint. These conditions
require special venting systems, which must be gas
tight and water tight.
NOTE: When an existing Furnace is removed from a
venting system serving other gas appliances, the vent-
ing system is likely to be too large to properly vent the
remaining attached appliances.
The following steps shall be followed with each appli-
ance remaining connected to the common venting sys-
tem placed in operation, while the other appliances re-
maining connected to the common venting system are
not in operation.
1. Seal any unused openings in the common venting
system.
2. Visually inspect the venting system for proper size
and horizontal pitch and determine there is no
blockage or restriction, leakage, corrosion or other
deficiencies which could cause an unsafe condition.
3. In so far as is practical, close all building doors and
windows and all doors between the space in which
the appliances remaining connected to the common
venting system are located and other spaces of the
building. Turn on clothes dryers and any appliances
not connected to the common venting system.
Turn on any exhaust fans, such as range hoods and
bathroom exhausts, so they will operate at maxi-
mum speed. Do not operate a summer exhaust fan,
close fireplace dampers.
4. Follow the lighting instructions. Place the appliance
being inspected in operation. Adjust Comfort Con-
trol so appliance will operate continuously.
5. After it has been determined that each appliance re-
maining connected to the common venting system
properly vents when tested as outlined above, return
door, windows, exhaust fans, fireplace dampers and
any other gas-burning appliance to their previous
conditions of use.
If improper venting is observed during any of the above
tests, the remaining common venting system must be
corrected. Correction could require rerouting or
resizing the remaining vent system.