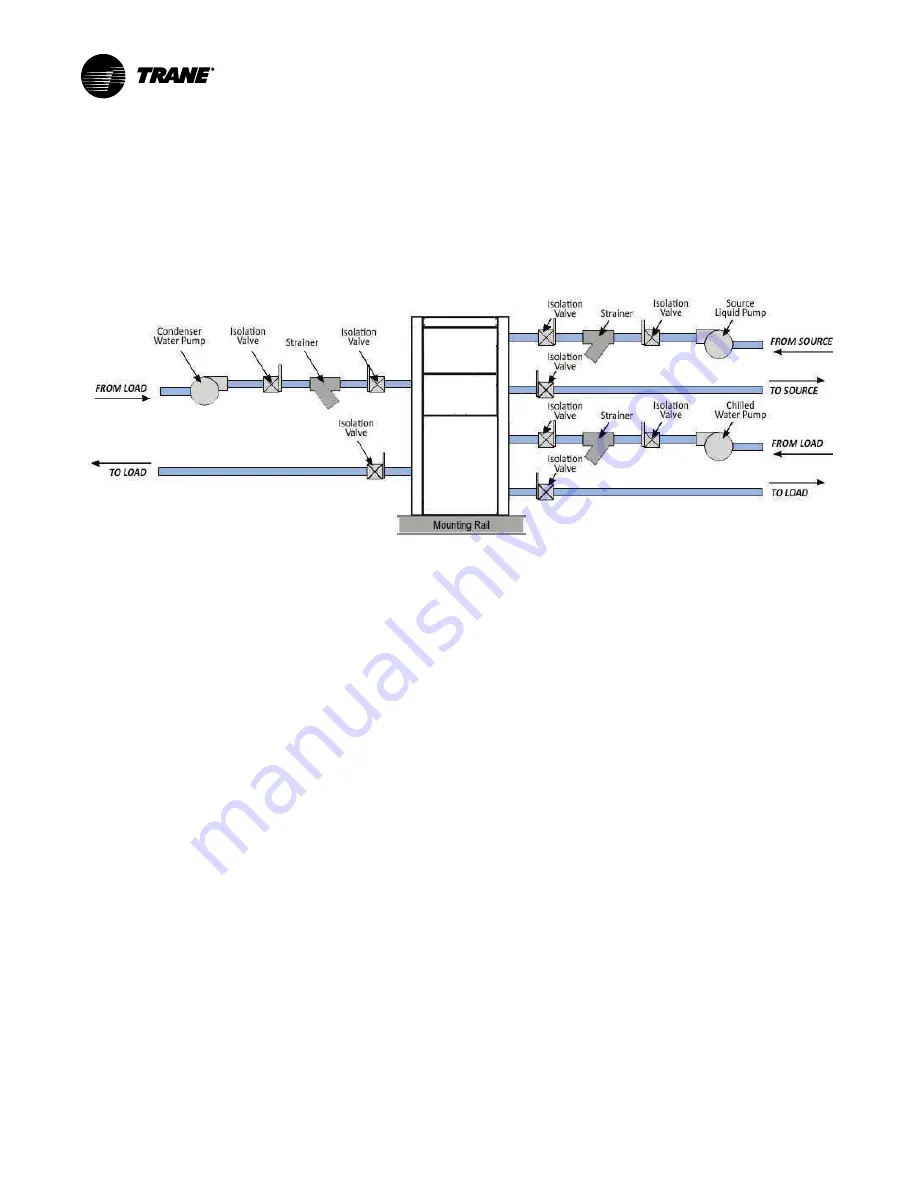
ARTC-SVX005B-EN
21
Installation Piping
Install Piping and External
Components
Proper support of piping and pipe hangers must
consider the weight of the piping as well as the water
weight inside the pipes. A 40-mesh screen strainer
must be installed in each water/liquid system piping
inlet for proper filtration an protection of the heat
exchangers. The following figure provides a
recommended installation of components.
Figure 5. Recommended PolyTherm chiller/heater piping
IIm
mp
po
orrtta
an
ntt:: An electronic expansion valve is a butterfly
valve used on an evaporator when the
water/glycol mixture flow is variable or to
operate an ‘N+1’ chiller/heater module
configuration. (‘N+1’ is a configuration
whereby a spare module is brought on line
should an operating module fail. The spare
module’s electronic expansion valve
opens, and the failed module’s valve closes
thereby keeping the pressure drop and flow
through each evaporator in the system
constant). Each valve has a 24 Vac power
supply opening, closing or modulation by a
0 to 10 Vdc signal. A sensor in the water/
glycol mixture header detects temperature
or pressure via an electronic signal to the
microprocessor that in turn controls the
voltage to the valve actuator motor. The
signal is either 0 or 10 volts.
Initial Flushing of Piping
After installation of system piping and before
connection to the chiller/heater system, it is important
to clean and remove debris, weld slag, and other
contamination deposited during fabrication of the
piping system. Typical flushing includes hot water with
mild detergent followed by a dilute phosphoric acid
solution until all visible residue is removed.
Only cleaning liquids, acids, and detergents compatible
with SAE Grade 316 stainless steel, copper, and carbon
steel should be used. Consult a professional water
treatment specialist when in doubt.
Flushing should take place across a filter/strainer with a
maximum 30 mesh screen and continue for a minimum
of six hours with frequent removal of the screen to
capture residue or until the strainer is clean.
After detergent and chemical cleaning, flush the water
piping with fresh water for one hour to remove any
remaining cleaning compounds.
Fill with Water/Glycol Solution
The installing contractor is responsible for charging
glycol into the chiller/heater hydronic system. These
instructions are typically for water cooled as air cooled
modules have more work space.
1. Mix the concentrate of propylene glycol in a tank or
drum for transfer into the chiller. Use
to determine the appropriate glycol
concentration.
2. Mix the glycol and water externally before filling
the chiller/heater to prevent clogging of the chiller
piping with a heavy concentrate.
3. Fill the tank using the manual fill port on the
cabinet. Fill so that the mixture reaches near the
top. Stop every so often so the fill level can be
monitored.
N
No
otte
e:: Do not use a glycol feeder pump to fill the chiller/
heater loop. It is not designed for continuous use
and will fail.
Only after the above steps have been completed
should the water piping be connected to the chiller/
heater system.