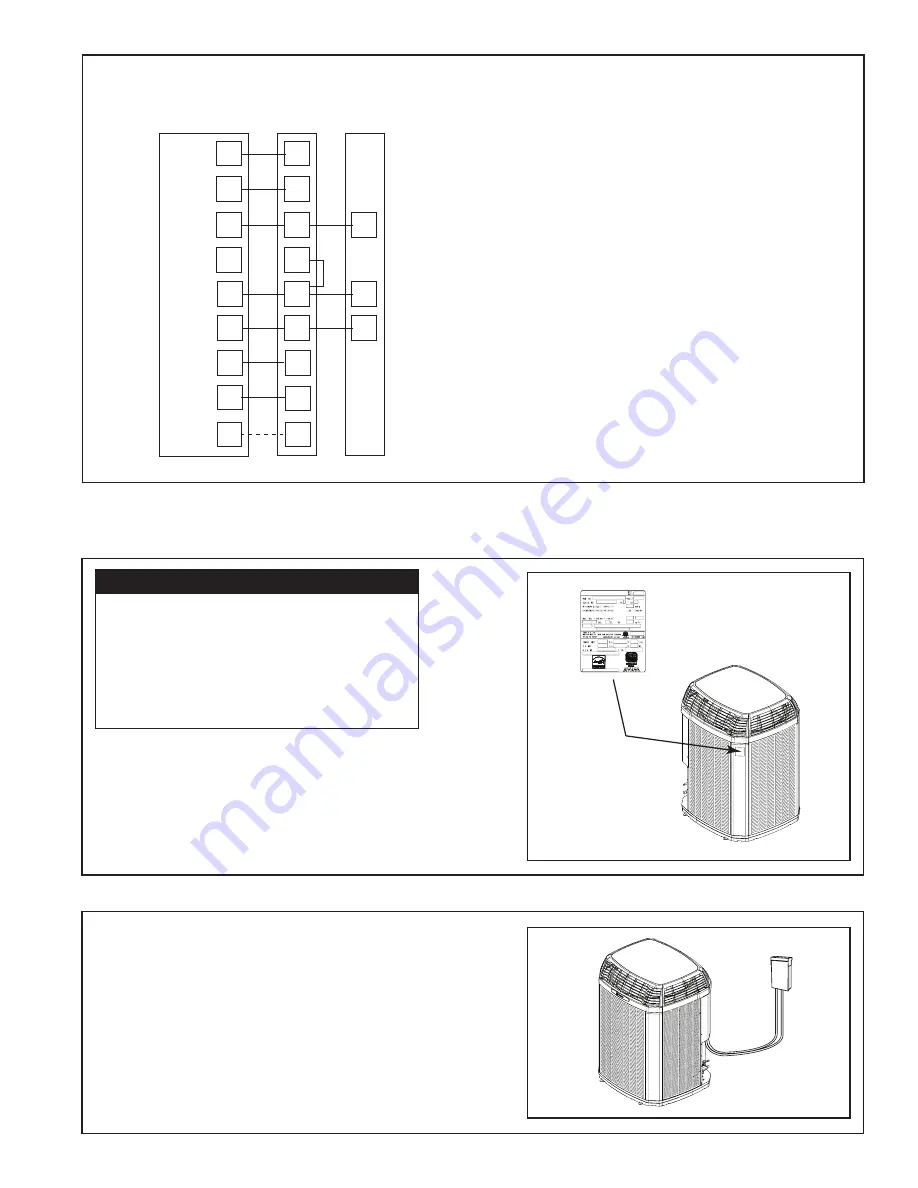
18-AC95D1-5C-EN
15
Section 12. Electrical - High Voltage
12.1 High Voltage Power Supply
The high voltage power supply must agree with
the equipment nameplate. Power wiring must
comply with national, state, and local codes.
Follow instructions on unit wiring diagram located
on the inside of the control box cover and in the
Service Facts document included with the unit.
LIVE ELECTRICAL COMPONENTS!
During installation, testing, servicing, and
troubleshooting of this product, it may be nec-
essary to work with live electrical components.
Failure to follow all electrical safety precau-
tions when exposed to live electrical compo-
nents could result in death or serious injury.
s
s
WARNING
With Variable Speed S-Series Furnace
NOTES:
1) For PWM (BK) enabled thermostats, cut the BK jumper on
the IFC and connect wiring.
2) The factory Y1-O jumper must remain in place for proper
LED read out in cooling mode.
3) Y1 and Y2 wiring from the thermostat must connect to
the IFC for proper airflow and LED readout.
4) Single compressor and two compressor airflow is auto-
matically set with the IFC Menu options in ODU section.
2-1=2 stage / 1 compressor (1st stage airflow = 75%)
2-2=2 stage / 2 compressors (1st stage airflow = 50%)
Furnace
Y1
Y1
Thermostat
Outdoor
Unit
R
G
W1
W2
R
G
B/C
B/C
B
Y1
W1
W2
Y2
Y2
Y2
24 VAC HOT
FAN
SOV
24 VAC
Common
HEATING
O
O
BK
BK
(1)
(2)
COOL
1st STAGE
COOL
2nd STAGE
12.2 High Voltage Disconnect Switch
Install a separate disconnect switch at the
outdoor unit.
For high voltage connections, flexible electri-
cal conduit is recommended whenever vibra-
tion transmission may create a noise problem
within the structure.
Summary of Contents for 4TTX8024A
Page 25: ...18 AC95D1 5C EN 25...