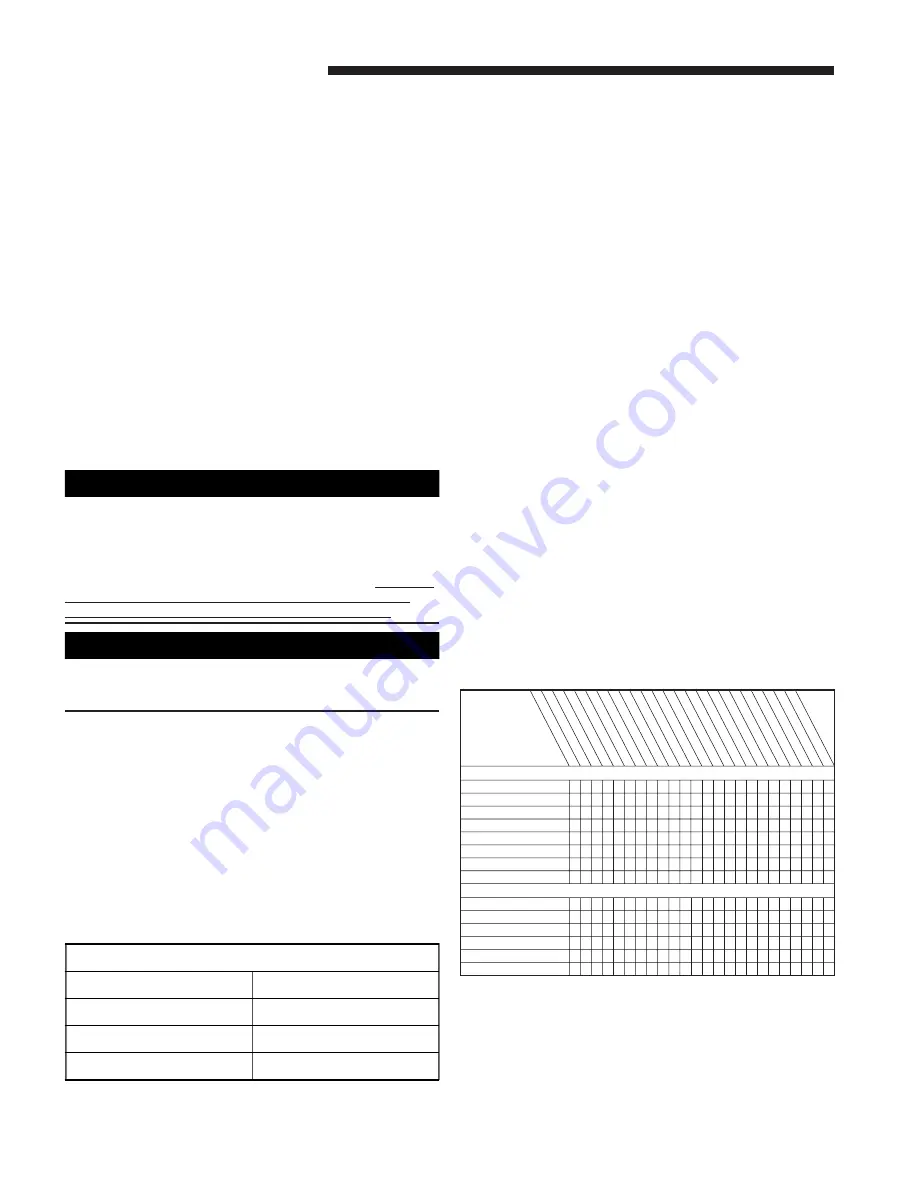
4
18-AC51D3-3
Installer’s Guide
rolled edge (approximately five [5] turns) observing
WARNING statement on page 2. See Figure 4.
10. Replace liquid service pressure tap port cap and valve
stem cap. These caps MUST BE REPLACED to
prevent leaks. Replace valve stem cap and pressure tap
cap finger tight, then tighten an additional 1/6 turn.
11. The gas valve can now be opened. For a ball type gas
valve, open the gas valve by removing the shut-off valve
cap and turning the valve stem 1/4 turn counterclock-
wise, using 1/4" Open End or Adjustable wrench. See
Figure 5. For brass gas line service valve opening, follow
9 and 10 above. See Figure 4.
12. The gas valve is now open for refrigerant flow. Replace
valve stem cap to prevent leaks. Again, these caps
MUST BE REPLACED to prevent leaks. Replace valve
stem cap and pressure tap cap finger tight, then tighten
an additional 1/6 turn. See Figure 5.
If refrigerant lines are longer than 15 feet and/or a
different size than recommended, it will be necessary to
adjust system refrigerant charge upon completion of
installation. See unit Service Facts.
F. ELECTRICAL CONNECTIONS
▲
CAUTION
!
Three phase scroll compressors will run in reverse if
powered up with improper phasing. If the compressor is
running backwards there will be little or no difference in
suction and discharge pressure and it will make a distinct
louder sound. Reversing any two of the field installed
power leads will correct the compressor rotation. Failure to
change the power leads to correct compressor rotation
may result in compressor damage during operation.
▲
WARNING
!
When installing or servicing this equipment, ALWAYS
exercise basic safety precautions to avoid the possibility of
electric shock.
1. Power wiring and grounding of equipment must comply
with local codes.
2. Power supply must agree with equipment nameplate.
3. Install a separate disconnect switch at the outdoor unit.
4. Ground the outdoor unit per local code requirements.
5. Provide flexible electrical conduit whenever vibration
transmission may create a noise problem within the
structure.
6. The use of color coded low voltage wire is recommended
to simplify connections between the outdoor unit, the
thermostat and the indoor unit.
Table 1 — NEC Class II Control Wiring
24 VOLTS
WIRE SIZE
MAX. WIRE LENGTH
18 AWG
150 FT
16 AWG
225 FT.
14 AWG
300 FT.
7. Table 1 defines maximum total length of low voltage
wiring from outdoor unit, to indoor unit, and to thermostat.
REFRIGERANT CIRCUIT
Liquid Pressure Too High
Liquid Pressure Too Low
Suction Pressure Too High
Suction Pressure Too Low
Liquid Refrig. Floodback TXV System
Liquid Refrig. Floodback Capillary Tube System
I.D. Coil Frosting
Compressor Runs Inadequate or No Cooling
ELECTRICAL
Compressor & O.D. Fan Do Not Start
Compressor Will Not Start But O.D. Fan Runs
O.D. Fan Won’t Start
Compressor Hums But Won’t Start
Compressor Cycles on IOL
I.D. Blower Won’t Start
SYSTEM FAULTS
P - Primary Causes S - Secondary Causes
P
P
P
S
S
P
S
S
S
S
S
S
S
P
S
S
S
S
P
P
P
P
S
S
S
S
S
S
S
P
P
P
P
S
P
P
S
S
S
P
P
P
P
P
P
P
P
P
P
S
S
S
S
P
P
P
P
P
S
S
P
S
P
S
S
S
S
S
S
S
P
P
P
P
P
S
P
P
POWER SUPPLY
HIGH VOLTAGE WIRING
COMPR. IOL
RUN CAPACITOR
START CAPACITOR
START RELAY
CONTACTOR CONTACTS
LOW VOLTAGE WIRING
CONTROL TRANSFORMER
CONTACTOR COIL
LOW VOLTAGE FUSE
STUCK COMPRESSOR
INEFFICIENT COMPRESSOR
REFRIGERANT UNDERCHARGE
REFRIGERANT OVERCHARGE
EXCESSIVE EVAP. LOAD
NONCONDENSABLES
RESTRICTED O.D. AIRFLOW
O.D. AIR RECIRCULATION
TXV STUCK OPEN
SUPERHEAT
RESTRICTED I.D. AIRFLOW
REF. CIRCUIT RESTRICTIONS
O.D. FAN SPEED SWITCH
TROUBLESHOOTING CHART — WHAT TO CHECK
8. Mount the indoor thermostat in accordance with instruc-
tion included with the thermostat. Wire per appropriate
hook-up diagram (included in these instructions).
G. COMPRESSOR START UP
After all electrical wiring is complete, SET THE THERMO-
STAT SYSTEM SWITCH IN THE OFF POSITION SO
COMPRESSOR WILL NOT RUN, and apply power by closing
the system main disconnect switch. This will activate the
compressor sump heat (where used). Do not change the
Thermostat System Switch until power has been applied for
one (1) hour. Following this procedure will prevent potential
compressor overload trip at the initial start-up.
H. OPERATIONAL AND CHECKOUT
PROCEDURES
Final phases of this installation are the unit Operational and
Checkout Procedures which are found in this instruction (see
page 8). To obtain proper performance, all units must be
operated and charge adjustments made in accordance with
procedures found in the Service Facts.
I. ELECTRIC HEATERS
Electric heaters, if used, are to be installed in the air han-
dling device according to the instructions accompanying the
air handler and the heaters.
J. OUTDOOR THERMOSTAT
An outdoor thermostat TAYSTAT250B may be field installed.
For data, see wiring diagram attached to unit and instruction
sheet packaged with outdoor thermostat.
K. SEACOAST SHIELD
Units installed within one mile of salt water, including
seacoasts and inland waterways, require the addition of
BAYSEAC001 (Seacoast Kit) at the time of installation.
L. TROUBLESHOOTING