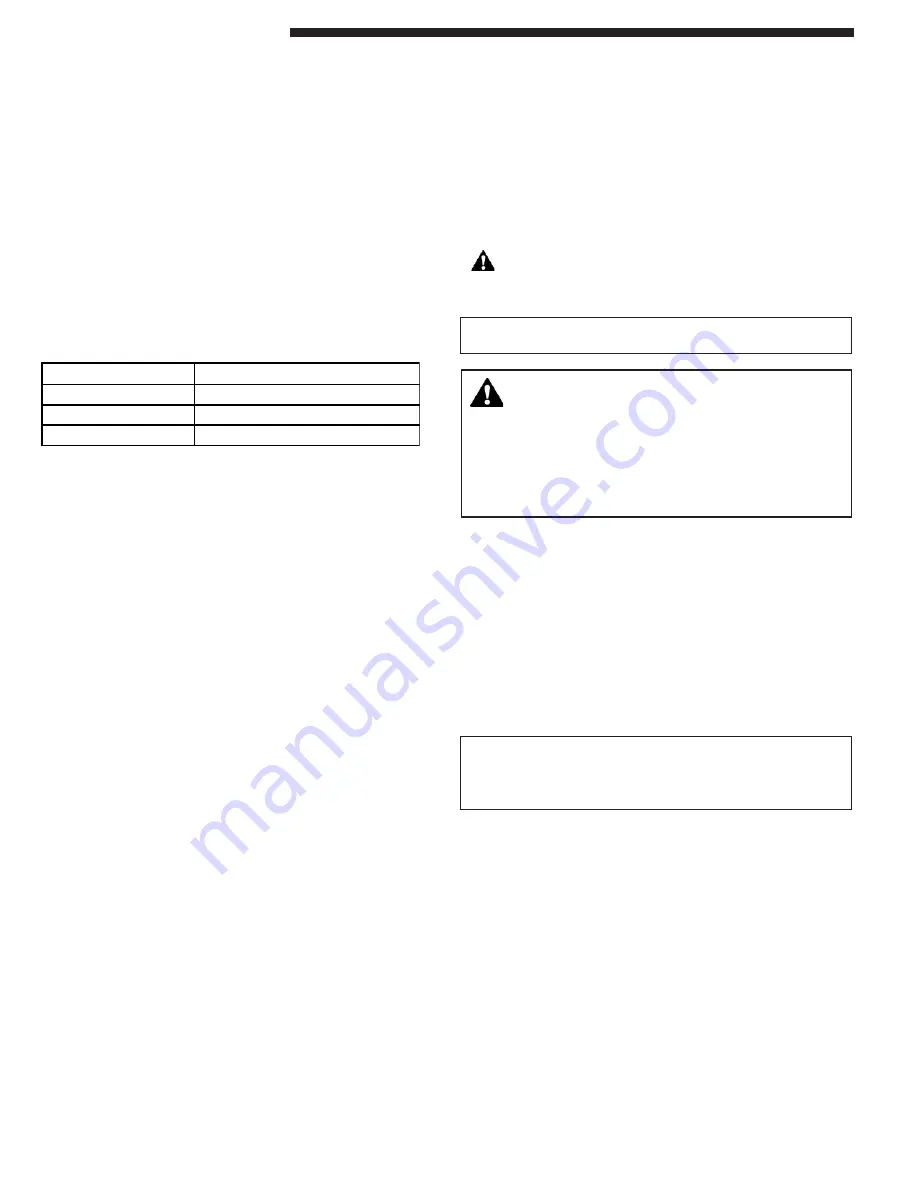
Page 20
Installer’s Guide
Starting the Unit in Cooling Mode
CAUTION: Before starting the system on the cooling cycle,
turn the thermostat switch to OFF and close the unit disconnect
switch. This is a precaution against foaming at startup which
could damage the compressor bearings.
Note: See the section on “Sequence of Operation” for a
description of the cooling operating sequence.
To start the unit in the cooling mode, set the thermostat system
switch to "COOL" and move the thermostat "COOL" indicator to a
setting below room temperature. The condenser fan motor, com-
pressor and evaporator fan motor will operate automatically.
Operating Pressure Checks
After the unit has operated in the cooling mode for a short period of
time, install pressure gauges on the gauge ports of the discharge
and suction line valves (behind the Compressor access panel).
Check the suction and discharge pressures and compare them to
the normal operating pressures provided in the unit’s
SERVICE
FACTS.
Note: Do not use the pressures from the unit's SERVICE FACTS
to determine the unit refrigerant charge. The correct charge is
shown on the unit nameplate. To charge the system accurately,
weigh in the charge according to the unit nameplate.
Voltage Check
With the compressor operating, check the line voltage at the unit
(contactor is located behind the Control access panel). The voltage
should be within the range shown on the unit nameplate. If low
voltage is encountered, check the size and length of the supply line
from the main disconnect to the unit. The line may be undersized
for the length of the run.
Cooling Shut Down
At the thermostat, place the system selector to the "OFF" position or
reset the thermostat to a setting above room temperature.
Control Wiring (Class II)
Low voltage control wiring should not be run in conduit with power
wiring unless Class 1 wire of proper voltage rating is used. Route
the thermostat cable or equivalent single leads of No. 18 AWG
colored wire from the thermostat subbase terminals through the
rubber grommet on the unit. See Figures 2, 4, 6, or 8 for the control
entry (24V Entry) location. Make connections as shown on the field
wiring diagram and in Figure 20.
Do not short thermostat wires since this will damage the control
transformer.
Refer to Table 2 for recommended wire sizes and lengths for
installing the unit thermostat. The total resistance of these low
voltage wires must not exceed one (1) ohm. Any resistance in
excess of 1 ohm may cause the control to malfunction because of
the excessive voltage drop.
IMPORTANT: Upon completion of wiring, check all electrical
connections, including factory wiring within the unit, and make
sure all connections are tight. Replace and secure all electrical
box covers and access panels before leaving the unit or turning
on the power to the unit.
Pre-Start Quick Checklist
Is the unit properly located and level with the proper
clearance? See Figures 1 to 8. See Step 3-Review
Location and Clearances on page 4.
Is the duct work correctly sized, run, taped, insulated, and
weatherproofed with proper unit arrangement? See
Ductwork Installation section on page 17.
Is the condensate line properly sized, run, trapped, and
pitched? See Condensate Drain Piping section on page
17.
Is the filter of the correct size and quantity? Is it clean and in
place? See Air Filter Installation section on page 18.
Is the wiring properly sized and run according to the unit
wiring diagram? See Electrical Wiring section on page 18.
Are all the wiring connections, including those in the unit,
tight? See Electrical Wiring section on page 18.
Has the unit been properly grounded and fused with the
recommended fuse size? See Electrical Wiring section on
page 18.
Is the thermostat well located, level, and correctly wired?
See Electrical Wiring section on page 18.
Have the air conditioning systems been checked at the service
ports for charge and leak tested if necessary?
Do the condenser fan and indoor blower turn free without
rubbing, and are they tight on the shafts?
Step 5—Unit Startup
WIRE SIZE
MAXIMUM LENTGH (Ft)
18
75
16
125
14
200
Table 2. Thermostat Wire Size and Maximum Length
Has the indoor blower speed been determined and the proper
speed been set?
To adjust the fan, see the Indoor Fan Motor
Speed Tap Setting section on page 22.
Has all work been done in accordance with applicable local
and national codes?
Are all covers and access panels in place to prevent air loss and
safety hazards?
WARNING:
DO NOT OPERATE THE UNIT WITH-
OUT THE EVAPORATOR FAN ACCESS PANEL OR EVAPO-
RATOR COIL ACCESS PANEL IN PLACE. REINSTALL THE
ACCESS PANELS AFTER PERFORMING MAINTENANCE
PROCEDURES ON THE FAN. OPERATING THE UNIT WITH-
OUT THE ACCESS PANELS PROPERLY INSTALLED MAY
RESULT IN SEVERE PERSONAL INJURY OR DEATH.