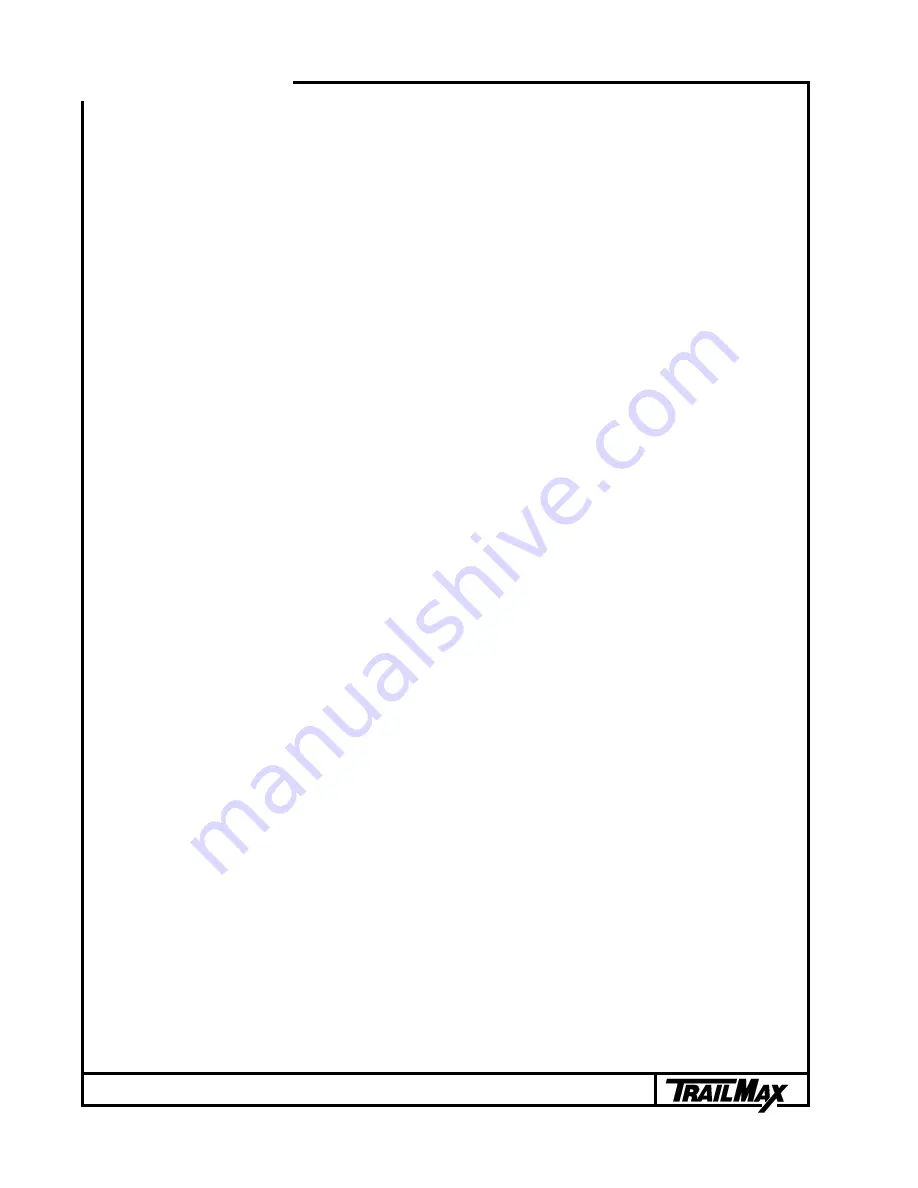
®
page 32
8012DT
Increasing the current flow to the electromagnet causes the magnet to grip the
armature surface of the brake drum more firmly. This results in increasing the pressure
against the shoes and brake drums until the desired stop is accomplished.
Using your Brakes Properly
Your trailer brakes are designed to work in synchronization with your tow vehicle
brakes. Never use your tow vehicle or trailer brakes alone to stop the combined load.
In order for your tow vehicle to provide the correct amperage flow to the trailer brake
magnets for comfortable and safe braking it is imperative that you make the proper
brake system adjustments. Changing trailer load and driving conditions as well as un-
even alternator and battery output can mean unstable current flow to the brake mag-
nets. It is therefore crucial that you maintain and adjust your brakes as set forth in this
manual, use a properly modulated brake controller, and perform the synchronization
procedure noted below.
In addition to the synchronization adjustment detailed below, electric brake control-
lers provide a modulation function that varies the current to the electric brakes with the
pressure on the brake pedal or amount of deceleration of the tow vehicle. It is important
that your brake controller provide approximately 2 volts to the braking system when the
pedal is first depressed and gradually increases the voltage to 12 volts as brake pres-
sure is increased. If the controller “jumps” immediately to a high voltage output, even
during a gradual stop, then the electric brakes will always be fully energized and will
result in harsh brakes and potential wheel lockup.
Proper synchronization of the tow vehicle to trailer braking can only be accom-
plished by road testing. Brake lockup, grabbiness, or harshness is quite often due to
the lack of synchronization between the tow vehicle and the trailer being towed, too
high of a threshold voltage (over 2 volts), or under adjusted brakes.
Before any synchronization adjustments are made, your trailer brakes should be
burnished-in by applying the brakes 20 to 30 times with approximately a 20 mph de-
crease in speed, for example slowing from 40 to 20 mph each time. Allow ample time for
the brakes to cool between application. This allows the brake shoes and magnets to
slightly “wear-in” to the drum surfaces.
Maintenance
Summary of Contents for 8012DT
Page 43: ...page 43 8012DT 1 2 3 4 6 5 8 7 9 10 11 12 13 14 15 16...
Page 44: ...page 44 8012DT THIS PAGE LEFT BLANK INTENTIONALLY...
Page 49: ...page 49 8012DT Parts P A R T S 1 2 3 4 5 6...
Page 53: ...page 53 8012DT Parts P A R T S 9 10 8 6 12 11 13 17 1 7 14 15 3 2 5 16 4...
Page 57: ...page 57 8012DT Parts P A R T S 9 10 2 3 2 1 6 8 7 5 4...
Page 61: ...page 61 8012DT Parts P A R T S 1 3 2 7 8 5 6 4 10 9...
Page 63: ...page 63 8012DT Parts 9 7 5 3 1 20 25 24 17 15 14 21 23 13 12 16 10 8 2 6 11 18 4 22...
Page 64: ...page 64 8012DT Parts Power Unit Motor...
Page 65: ...page 65 8012DT P A R T S Parts THIS PAGE LEFT BLANK INTENTIONALLY...
Page 66: ...page 66 8012DT Power Unit Control Valve Parts...
Page 67: ...page 67 8012DT Parts P A R T S Power Unit Control Valve Schematic...
Page 68: ...page 68 8012DT Gear Pump and Manifold Assembly Parts List Parts...
Page 69: ...page 69 8012DT Parts P A R T S Gear Pump and Manifold Assembly Parts Illustration...
Page 70: ...page 70 8012DT 3 7 Tool Box Ref Quantity Description Part No 1 1 Tool Box TM321 421...
Page 71: ...page 71 8012DT P A R T S THIS PAGE LEFT BLANK INTENTIONALLY...