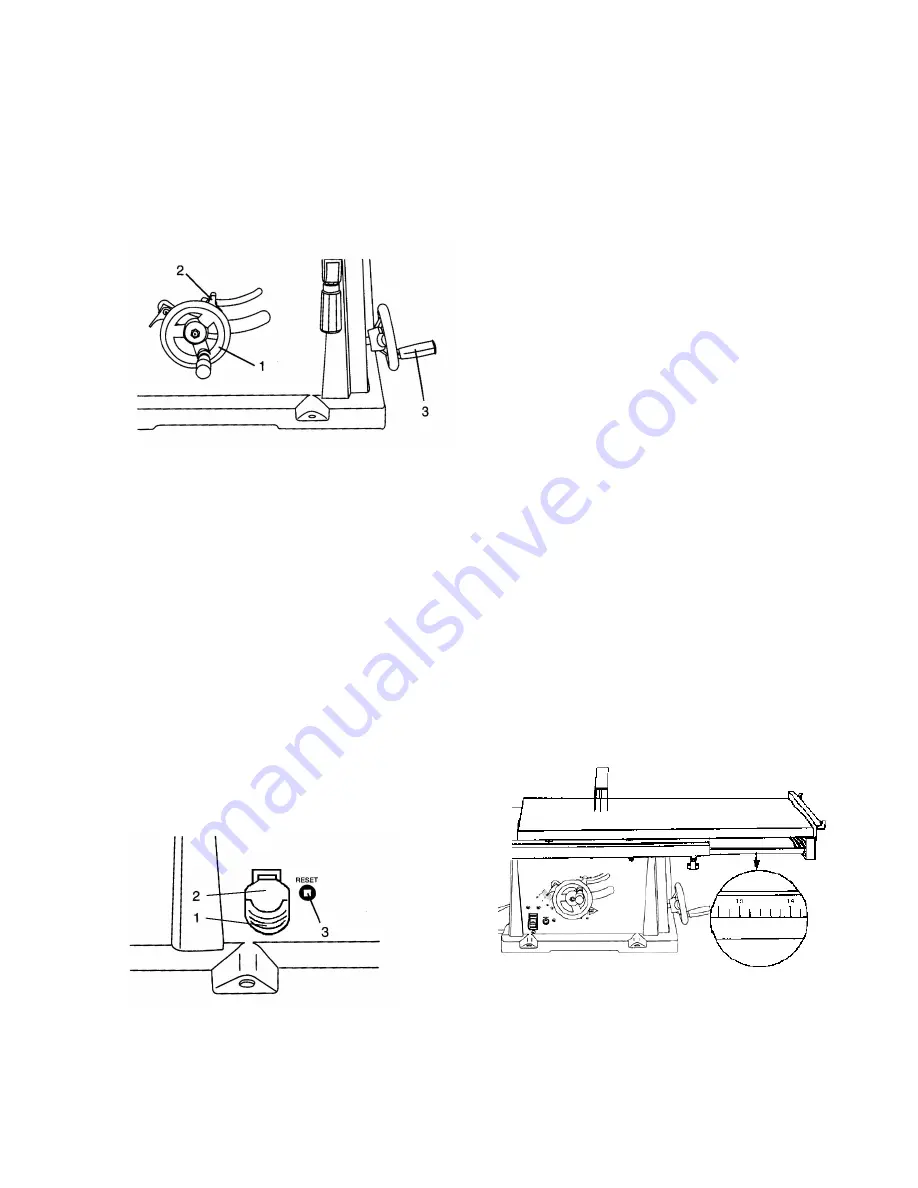
17
OPERATION
RAISE THE BLADE (FIG. 24)
To raise or lower the blade, turn the blade elevation
handwheel (1) to the desired blade height, and then tighten
lock handle (2) to maintain the desired blade angle.
Fig. 24
TILTING THE BLADE (FIG. 24)
1. To tilt the saw blade for bevel cutting, loosen the lock
knob (2) and turn the tilting handwheel (3).
2. Tighten the lock knobs (2) to secure at your desired angle.
ON/OFF SWITCH (FIG. 25)
The ON / OFF switch has a removal key. With the
key removed from the switch, unauthorized and hazardous
use by children and others is minimized.
1. To turn the saw ON, insert key (1) into the slot in the
switch (2). Move the switch upward to the ON position.
2. To turn the saw OFF, move the switch downward.
3. To lock the switch in the OFF position, grasp the end (or
yellow part) of the toggle switch (1), and pull it out.
4. With the switch key removed, the switch will not operate.
5.
If the switch key is removed while the saw is running, it
can be turned OFF but cannot be restarted without
inserting the switch key (1).
Fig. 25
OVERLOAD PROTECTION (FIG. 25)
This saw has a reset overload relay button (3) that
will restart the motor after it shuts off due to overloading or
low voltage. If the motor stops during operation, turn the
ON / OFF switch to the OFF position. Wait about five
minutes for the motor to
cool. Push in on the reset button (3) and turn the switch to
the ON position.
CAUTION!
To avoid injury, the ON / OFF switch should be in the OFF
position and the plug removed from the power source while
the cool down takes place, to prevent accidental starting
when the reset button is pushed. Overheating may be caused
by misaligned parts, a dull blade or too long underside
extension cord. Inspect your saw for proper setup before
using it again.
USING THE TABLE EXTENSION (FIG. 26)
NOTE:
Raise the fence (1) to a position that just clears the
table surface and secure in place using lock handles for
IN-
RIP
position.
NOTE:
To change sides of the table extension.
1. Remove the stop screws from the ends of the tubes.
2. Slide the ends of the tubes through both support
brackets on the side your workpiece will be needed
support, and replace the two stop screws.
3. Rotate the front tube to display the scale as an extension
of the table top scale.
4. Slide the extension out until the correct measurement is
displayed on the tube scale.
5. Loosen the fence handles, and raise or lower the fence
as needed.
6. Tighten all extension support handles and knobs.
Fig. 26
17
Summary of Contents for BTS10W4
Page 7: ...CARTON CONTENTS 7 A M S R B F G C D E Q P K J I H O N L ...
Page 25: ...25 ...
Page 27: ...MOTOR DIAGRAM 27 ...