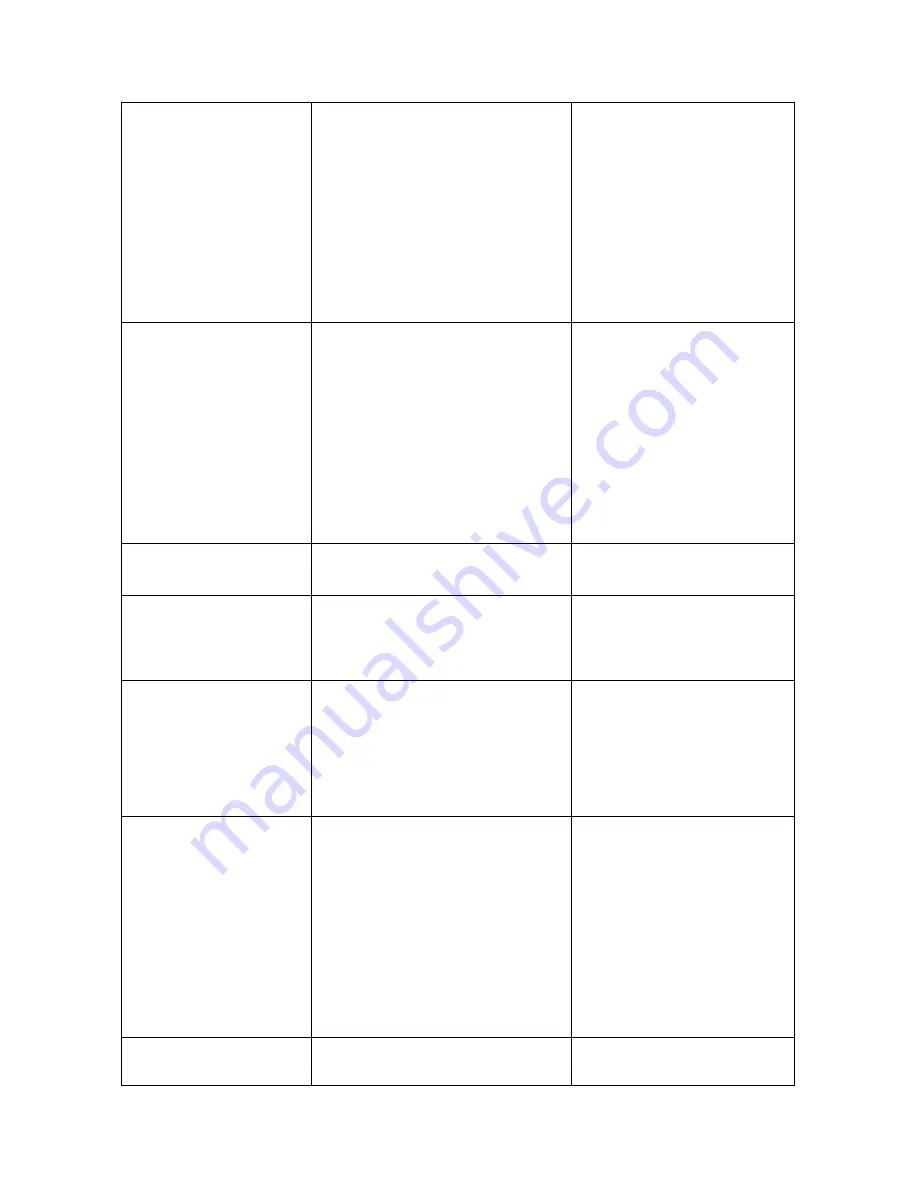
12
4.Material too coarse
5.Incorrect blade tension
6.Teeth in contact with material before saw
is started
7. Blade rubs on wheel flange
8. Miss-aligned guide bearings
9. Blade too thick
10.Cracking at weld
blade
4. Use a blade of slow speed and
small teeth spacing
5. Adjust to where blade just
does not slip on wheel
6. Place blade in contact with
work after motor is starred
7. Adjust wheel alignment
8. Adjust guide bearings
9. Use thinner blade
10. Weld again, beware the welding
skill.
Premature Blade Dulling
1. Teeth too coarse
2. Too much speed
3. Inadequate feed pressure
4.Hard spots or scale on material
5. Work hardening of material.
6.Blade twist
7. Insufficient blade
8. Blade slide
1. Use finer teeth
2. Decrease speed
3. Decrease spring tension on side of
saw
4. Reduce speed, increase feed
pressure
5. Increase feed pressure by reducing
spring tension
6. Replace with a new blade, and
adjust blade tension
7. Tighten blade tension adjustable
knob
8. Tighten blade tension
Unusual Wear on
Side/Back of Blade
1.
Blade guides worn.
2.
Blade guide bearings not adjust properly
3.
Blade guide bearing bracket is loose
1.
Replace.
2.
Adjust as per operators manual
3.
Tighten.
Teeth Ripping from
Blade.
1. Tooth too coarse for work
2. Too heavy pressure; too slow speed.
3. Vibrating work-piece.
4. Gullets loading
1. Use finer tooth blade.
2. Decrease pressure, increase speed
3. Clamp work piece securely
4. Use coarser tooth blade or brush to
remove chips.
Motor running too hot
1.
Blade tension too high.
2.
Drive belt tension too high.
3. Blade is too coarse for work
4. Blade is too fine for work
5. Gears aligned improperly
6. Gears need lubrication
7. Cut is binding blade
1. Reduce tension on blade.
2. Reduce tension on drive belt.
3. Use finer blade.
4. Use coarse blade.
5. Adjust gears so that worm is in
center of gear.
6. Check oil path.
7. Decrease reed anti speed
Bad Cuts (Crooked)
1. Feed pressure too great.
2. Guide bearings not adjusted properly
3. Inadequate blade tension.
4. Dull blade.
5. Speed incorrect.
6. Blade guides spaced out too much
7. Blade guide assembly loose
8. Blade truck too far away from wheel
flanges
1. Reduce pressure by increasing
spring tension on side of saw
2. Adjust guide bearing, the clearance
can not greater than 0.001.
3.
Increase blade tension by adjust
blade tension
4.
Replace blade
5. Adjust speed
6. Adjust guide space.
7. Tighten
8. Re-track blade according to
operating instructions.
Bad Cuts (Rough)
1. Too much speed or feed
2. Blade is too coarse
1. Decrease speed or feed.
2. Replace with finer blade.