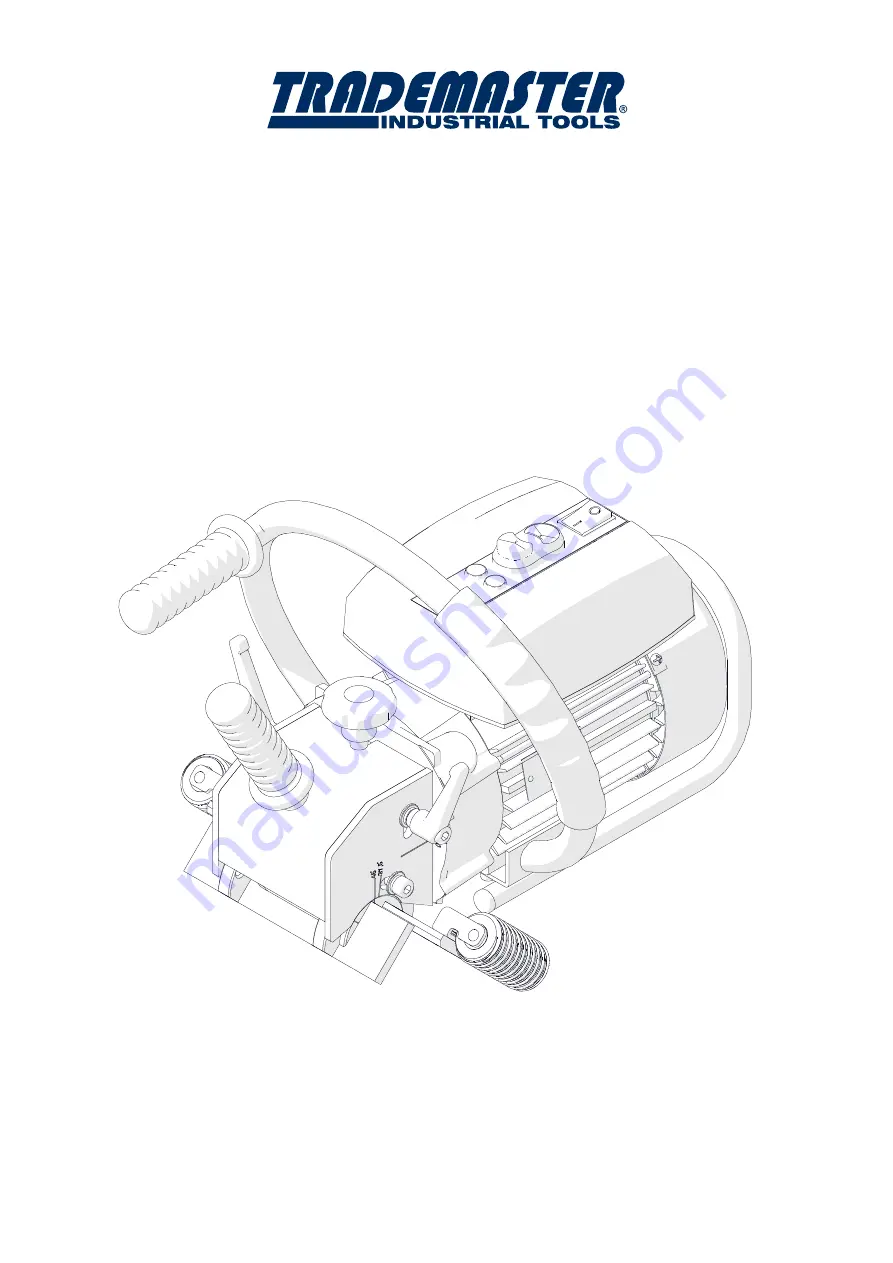
BEFORE USE, ENSURE EVERYONE USING THIS MACHINE READS AND UNDERSTANDS
ALL SAFETY AND OPERATING INSTRUCTIONS IN THIS MANUAL .
Serial #............................................ Date of Purchase............................
Ver: 1.0 01/05/2015
OPERATOR’S MANUAL
PART# WA-B20+
BM-20 PLUS
BEVELLING MACHINE
Summary of Contents for BM-20 Plus
Page 4: ...BM 20 PLUS Operator s Manual 4 446 mm 17 6 315 mm 12 4 323 mm 12 7 ...
Page 16: ...BM 20 PLUS Operator s Manual 16 5 WIRING DIAGRAM ...
Page 18: ...BM 20 PLUS Operator s Manual 18 7 PARTS BREAKDOWN ...
Page 19: ...BM 20 PLUS Operator s Manual 19 9 9 9 9 9 9 ...
Page 21: ...BM 20 PLUS Operator s Manual 21 9 9 9 9 9 2 A9 A A A A A A A ...