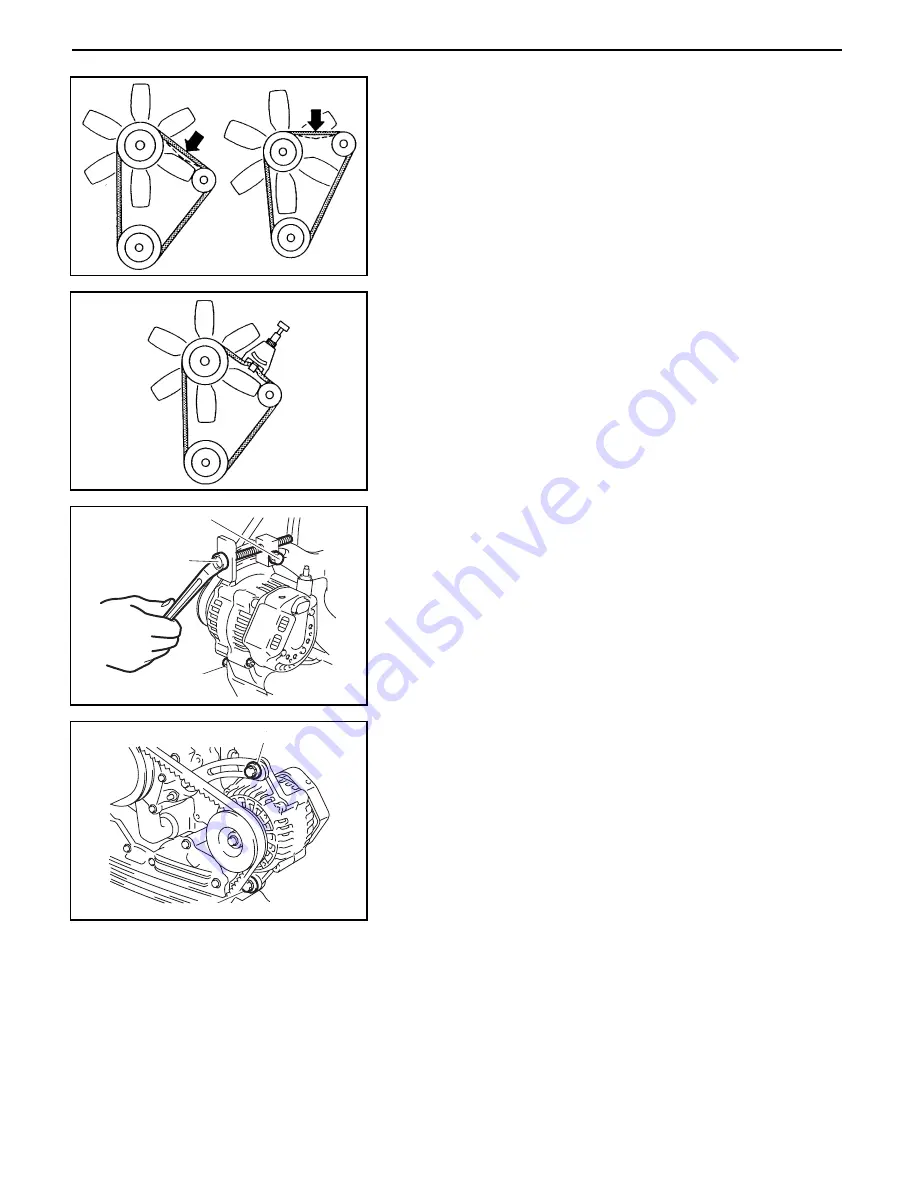
1-26
1-26
V-BELT TENSION ADJUSTMENT
1.
Inspect the V-belt tension.
Standard
[amount of delfection when pressed with 98 N (10 kgf)]
4Y:
8~13 mm (0.31~0.51 in)
1DZ-II:
8~13 mm (0.31~0.51 in)
Standard
[When using a tension gauge (SST)]
SST 09216-76002-71 (09216-00021)
4Y:
294~490 N (30~50 kgf) [66~110 lbf]
1DZ-II:
324~559 N (33~57 kgf) [73~126 lbf]
2.
V-belt deflection adjustment
4Y engine vehicle
(1) Loosen the fixing bolt.
(2) Loosen the set bolt and turn the adjustment bolt to adjust
the tension.
(3) Tighten the fixing bolt and recheck the belt tension.
Note:
Be careful not to apply excessive tension to the belt.
1DZ-II engine vehicles
(1) Loosen the fixing bolt and adjusting bolt.
(2) Stretch the V-belt using a pry bar with the length of 300 to
400 mm (11.8 to 15.7 in), and tighten the alternator
adjustment bolt.
(3) Tighten the fixing bolt then recheck the belt tension.
Note:
Adjustment of the tension using a pry bar gives rise to
considerable individual differences, and tends to result in
excessive or insufficent tension. Therefore, be sure to inspect
the deflection amount.
Set bolt
Adjustment bolt
Fixing bolt
Adjustment bolt
Fixing bolt
Engine
Section 1
Summary of Contents for 8FDU15
Page 3: ...0 2a EXTERIOR VIEWS General Section 0 ...
Page 4: ...0 2 0 2 EXTERIOR VIEWS General Section 0 0 2b ...
Page 21: ...0 17 8FG D U15 32 8FGCU20 32 COMPONENTS WEIGHT 8FGCU15 18 SU20 General Section 0 ...
Page 33: ...1 2 1 2 ENGINE EXTERIOR VIEW 4Y Engine Engine Section 1 ...
Page 34: ...1 3 0 1 2 3 4 5 6 7 8 9 10 11 12 13 14 15 16 17 18 19 20 21 E 1DZ II Engine Engine Section 1 ...
Page 55: ...1 18 1 18 RADIATOR COMPONENTS 4Y 1DZ II 1603 1603 Engine Section 1 8FG D U15 32 8FGCU20 32 ...
Page 57: ...RADIATOR COMPONENTS 1603 Engine Section 1 8FGCU15 18 SU20 1 19b ...
Page 64: ...1 23 BATTERY COMPONENTS 4Y 1DZ II 1901 1901 Engine Section 1 ...
Page 68: ...1 27 ACCELERATOR PEDAL COMPONENTS 4Y 1DZ II 2601 2601 Engine Section 1 ...
Page 71: ...1 30 1 30 EZ PEDAL OPT COMPONENTS 2601 Engine Section 1 ...
Page 83: ......
Page 86: ...ENGINE EXTERIOR VIEW 4Y M 4Y E Repair Section 1 1 0 ...
Page 87: ...4Y E OPT 4Y E Repair Section 1 1 0 ...
Page 88: ...ENGINE SECTIONAL VIEW 4Y E Repair Section 1 1 0 ...
Page 89: ...4Y E Repair Section 1 1 0 ...
Page 103: ......
Page 126: ...CYLINDER HEAD COMPONENTS 40 3 WAY CATALYTIC 4Y E Repair Section 1 1 2 ...
Page 127: ...4Y E Repair Section 1 1 2 ...
Page 128: ...Refer to 2601 HJ 4Y E Repair Section 1 1 2 ...
Page 138: ...TIMING GEAR COMPONENTS 4Y E Repair Section 1 1 2 ...
Page 139: ...4Y E Repair Section 1 1 2 ...
Page 140: ...4Y E Repair Section 1 1 2 ...
Page 151: ...I I L l l l l l l J I I s 2 0 c L l l l 1114 4Y E Repair Section 1 1 2 ...
Page 165: ......
Page 173: ...CYLINDER HEAD COMPONENTS 4Y E Repair Section 1 1 3 ...
Page 174: ...4Y E Repair Section 1 1 3 ...
Page 175: ...4Y E Repair Section 1 1 3 ...
Page 185: ...TIMING GEAR COMPONENTS 4Y E Repair Section 1 1 3 ...
Page 186: ...4Y E Repair Section 1 1 3 ...
Page 187: ...4Y E Repair Section 1 1 3 ...
Page 198: ...I I L l l l l l l I I I L l l l I I l J T 4Y E Repair Section 1 1 3 ...
Page 214: ...FUEL PUMP COMPONENTS 4Y E Repair Section 1 1 4 ...
Page 218: ...COMPONENTS 4Y E Repair Section 1 1 4 ...
Page 231: ...AIR GOVERNOR COMPONENTS 4Y E Repair Section 1 1 4 ...
Page 237: ......
Page 240: ...THROTTLE BODY COMPONENTS 4Y E Repair Section 1 1 5 ...
Page 243: ...INJECTOR COMPONENTS 4Y E Repair Section 1 1 5 ...
Page 248: ...FUEL PUMP COMPONENTS COOLER I I FUEL CAP WIKEY I 4Y E Repair Section 1 1 5 ...
Page 253: ......
Page 255: ...VENTILATION VALVE COMPONENTS 4Y E Repair Section 1 1 6 ...
Page 257: ......
Page 259: ...WATER PUMP COMPONENTS 4Y E Repair Section 1 1 7 ...
Page 265: ...SST TO BE USED Illustration I I Part No Part name 4Y E Repair Section 1 1 8 ...
Page 268: ...OIL PUMPmSTRAINER COMPONENTS 4Y E Repair Section 1 1 8 ...
Page 273: ......
Page 275: ...CIRCUIT DIAGRAM Ignition key Switch Black with two orange stripes 4Y E Repair Section 1 1 9 ...
Page 277: ...DISTRIBUTOR COMPONENTS I I Refer to Refer to FIG 1901 FIG 1901 4Y E Repair Section 1 1 9 ...
Page 290: ...DISTRIBUTOR COMPONENTS Refer to Refer to 4Y E Repair Section 1 1 10 ...
Page 295: ......
Page 298: ...STARTER MOTOR COMPONENTS 4Y E Repair Section 1 1 11 ...
Page 309: ...ALTERNATOR ELECTRICAL CIRCUIT DIAGRAM COMPONENTS 4Y E Repair Section 1 1 12 ...
Page 327: ... This Page Intentionally Left Blank ...
Page 329: ... This Page Intentionally Left Blank ...
Page 332: ...ENGINE EXTERIOR VIEWS 1DZ II Repair Section 1 2 0 ...
Page 333: ...ENGINE SECTIONAL VIEWS 1DZ II Repair Section 1 2 0 ...
Page 334: ...1DZ II Repair Section 1 2 0 ...
Page 368: ...CYLINDER HEAD COMPONENTS 1DZ II Repair Section 1 2 2 ...
Page 369: ...1DZ II Repair Section 1 2 2 ...
Page 379: ...TIMING GEAR COMPONENTS 1DZ II Repair Section 1 2 2 ...
Page 380: ...1DZ II Repair Section 1 2 2 ...
Page 381: ...2 22 DISASSEMBLY INSPECTION AND REASSEMBLY 1DZ II Repair Section 1 2 2 ...
Page 392: ...CYLINDER BLOCK COMPONENTS 1DZ II Repair Section 1 2 2 ...
Page 393: ...1DZ II Repair Section 1 2 2 ...
Page 414: ...1DZ II Repair Section 1 2 3 ...
Page 419: ...3 8 INJECTION NOZZLE COMPONENTS 1DZ II Repair Section 1 2 3 ...
Page 425: ...1DZ II Repair Section 1 2 3 ...
Page 463: ...1DZ II Repair Section 1 2 3 ...
Page 465: ...WATER PUMP COMPONENTS Refer to 5701 30 1DZ II Repair Section 1 2 4 ...
Page 469: ...1DZ II Repair Section 1 2 4 ...
Page 474: ...OIL PUMP COMPONENTS 1DZ II Repair Section 1 2 5 ...
Page 480: ...PREHEATING SYSTEM ELECTRIC CIRCUIT DIAGRAM COMPONENTS 1DZ II Repair Section 1 2 6 ...
Page 483: ...STARTER MOTOR COMPONENTS 1DZ II Repair Section 1 2 6 ...
Page 493: ...1DZ II Repair Section 1 2 6 ...
Page 497: ...ALTERNATOR ELECTRIC CIRCUIT DIAGRAM COMPONENTS 1DZ II Repair Section 1 2 7 ...
Page 523: ... This Page Intentionally Left Blank ...
Page 537: ... This Page Intentionally Left Blank ...
Page 549: ... This Page Intentionally Left Blank ...
Page 569: ... This Page Intentionally Left Blank ...
Page 618: ...4 5 WIRING DIAGRAM ...