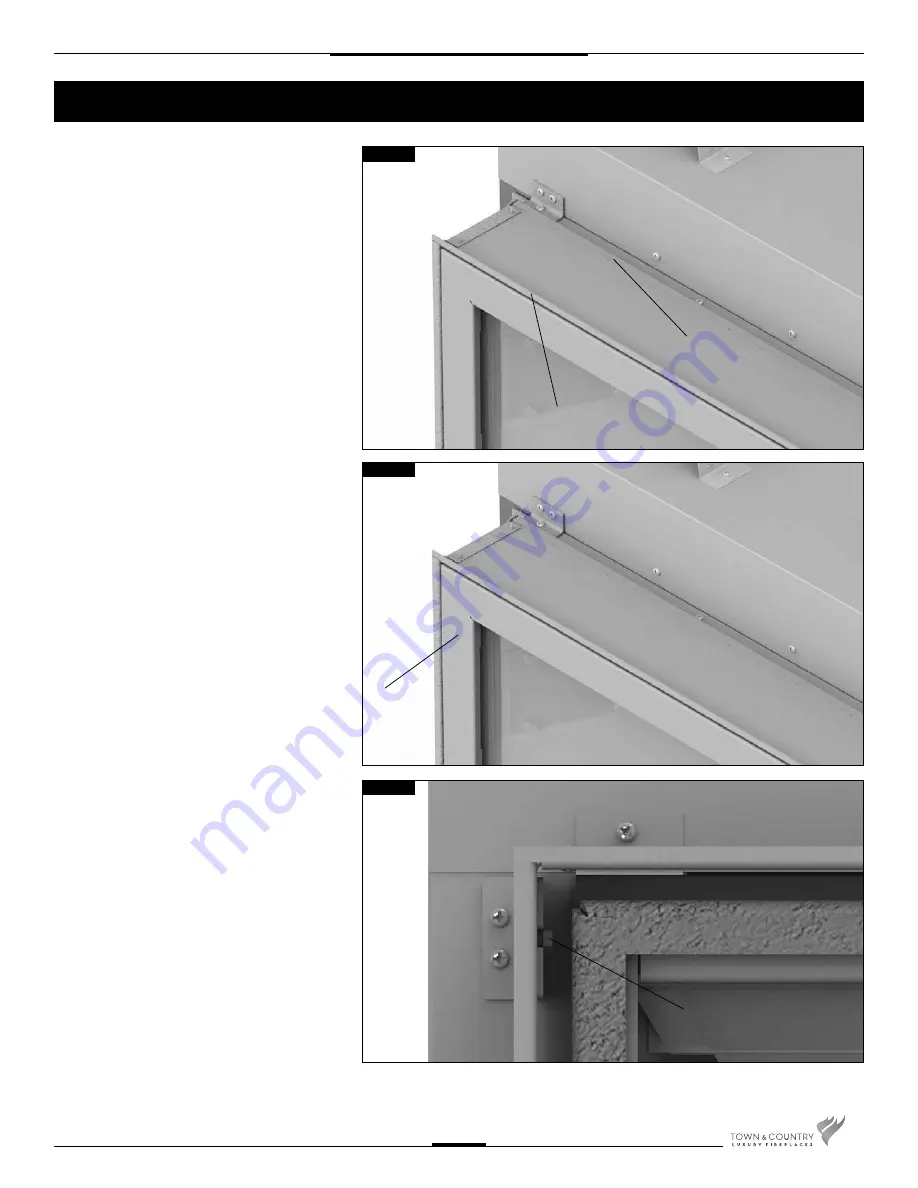
Adjustable Lintel
Fig. #20
Fig. #21
Fig. #22
1. The adjustable lintel assembly has two
orientations for desired fi nishing. A fl anged
edge and a hemmed edge. The lintel comes
factory installed with the fl ange edge out. If
the desired edge is different from the factory
setting, use the following steps to change
it(Fig.#20).
2. Remove the window trim (Fig.#21).
3. Loosen the securing bolts in the upper and
lower corners on each side of the lintel
and remove the lintel. Rotate the assembly
to have the desired edge away from the
fi replace(Fig .#22).
4. The lintel assembly has a maximum range
of adjustability of 1” to accommodate varying
facing material thicknesses. The maximum
depth is 6” (Fig.#19).
5. The lintel assembly can then be adjusted
to align fl ush with your facing material by
sliding in or out approximately 1”.
6. Tighten the securing bolts. (Fig.#22).
7.
Re-attach the window trim.
HEMMED EDGE
FLANGED EDGE
TRIM
SECURING
BOLT
15
TCWS.54CODE 102813-40
Summary of Contents for TCWS.54OD
Page 30: ...Fig 43 Wiring Diagram 30 TCWS 54CODE 102813 40 ...
Page 35: ...35 TCWS 54CODE 102813 40 ...
Page 36: ...36 TCWS 54CODE 102813 40 ...
Page 37: ...37 TCWS 54CODE 102813 40 ...
Page 38: ...38 TCWS 54CODE 102813 40 ...