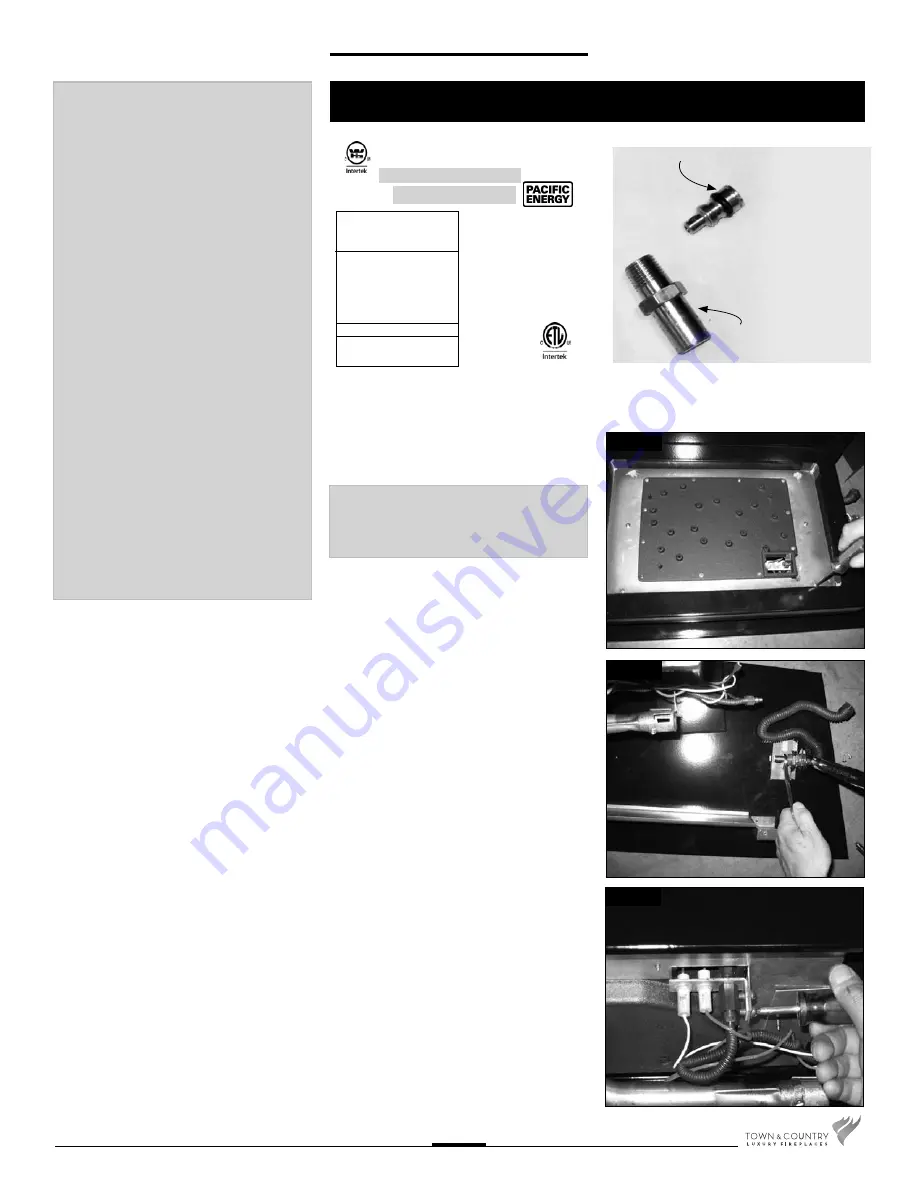
TC42.NG04C 260411-16
9
WARNING
This conversion kit
shall be installed by a
qualifi ed service agency
in accordance with the
manufacturer's instructions
and all applicable codes
and requirements of
the authority having
jurisdiction.
If the information in these
instructions is not followed
exactly, a fi re, explosion
or production of carbon
monoxide may result
causing property damage,
personal injury or loss of
life.
The qualifi ed service
agency is responsible for
the proper installation of
this kit.
The installation is not
proper and complete
until the operation of the
converted appliance is
checked as specifi ed in the
manufacturer's instructions
supplied with the kit.
If the unit is to be used on propane
c o nve r t a s fo l l ow s u s i n g t h e
components supplied with this
burner:
CAUTION
The gas supply and electrical power
shall be shut off before proceeding
with the conversion.
Note: Factory supplied components must be
used to ensure correct input.
After conversion confi rm proper manifold
pressure.
1.
Remove the 2 front screws holding the
burner tray in place.
(Fig.
#16)
2.
Gently lift up the burner tray while
sliding to the left to disengage the
burner tube from the orifi ce. Then tip
back to expose the orifi ce.
3.
Using a 1/2” wrench, undo the
natu ral gas burner orifi ce,
(marked
#25
). Apply a small amount
of pipe joint compound to the threads
of the propane burner orifi ce
(marked
3/32
) to ensure a good seal,
before screwing it into the fi tting.
Loosen the primary air shutter screw,
open shutter fully
and re-tighten.
(Fig.
#17)
4.
Remove the 2 screws
holding the pilot assembly in place with
a stubby screwdriver.
(Fig
#18)
The burner assembly must
be removed from the unit if
previously installed.
Propane Conversion
Fig #16
Fig #17
Fig #18
LP GAS/
DU GAZ LP
12.5 in/wc /12.5 po/c.e.
(3.11 kPa)
13.9 in/wc / 13.9 po/c.e.
(3.45 kPa)
11.0 in/wc / 11.0 po/c.e.
(.95 kPa)
3/32” (2.38 mm)
Max.: 61,000 (17.9)
Min.: 46,200 (13.5)
260411 6-TC42C 5052.5206C
Date: ______________________
By / Par: ___________________
Kit # TC42.LPKTB/EB/EC for use with model:
Pour utilise avec du modèle:
This appliance was converted
to PROPANE GAS with this
kit on this date by the or-
ganization which accepts the
responsibility that this conver-
sion has been properly made.
/ Cet appariel etair converter
au gaz LP par l’emploi de la
trousse de conversion par une
organization qui accepte la
responsibilité pour une instal-
lation en bon état.
TC42
Series C
MAIN BURNER
(3/32”) ORIFICE (5021.31)
MINIMUM RATE SCREW (5005.016)
CONVERSION LABEL (5052.5206C)
Summary of Contents for TC42.NG04C
Page 15: ...TC42 NG04C 260411 16 15 ...