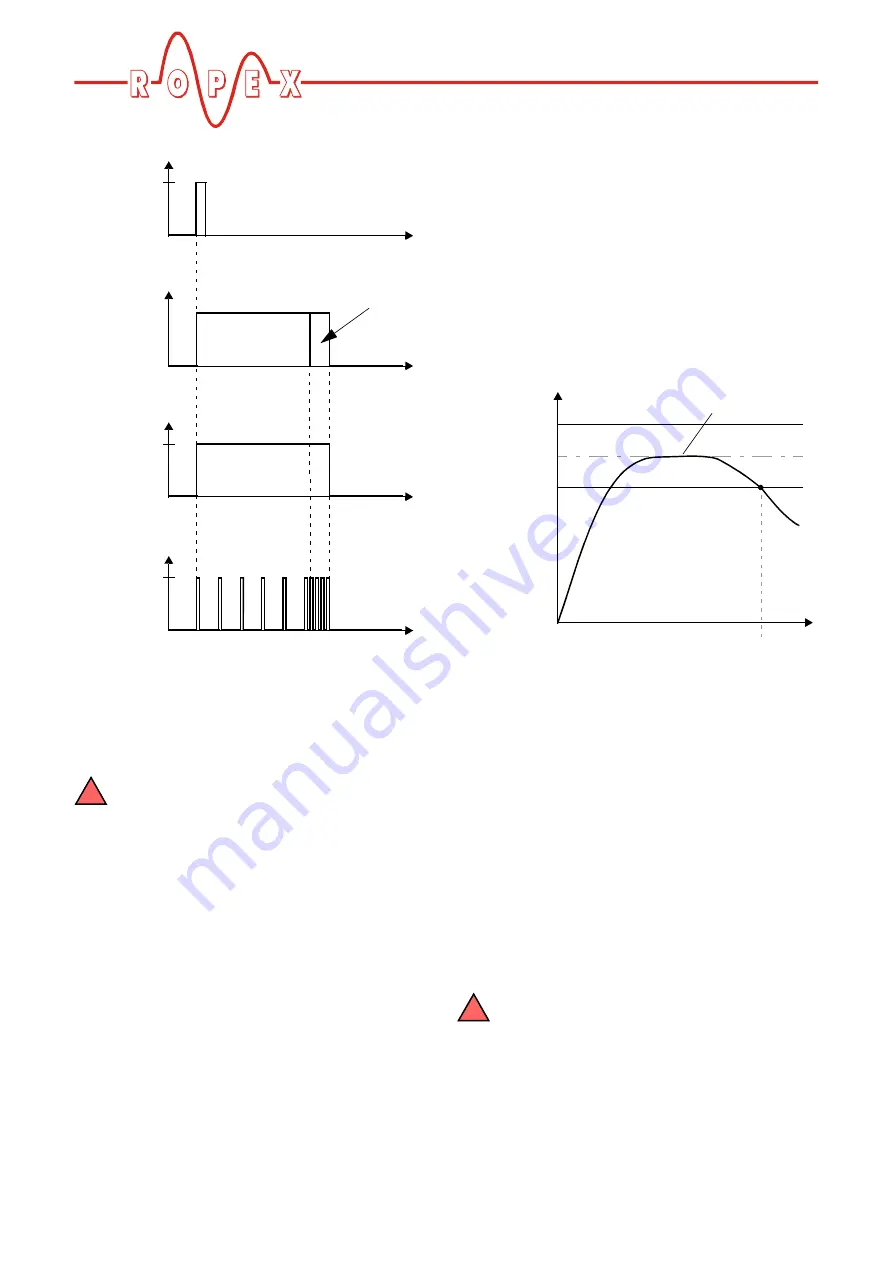
Controller functions
Page 30
RES-407
The "OUTPUT" LED blinks repeatedly when the
"AUTOCOMP" function is executed and the actual
value output (terminals 17+14) is set to 0…3°C (i.e.
app. 0 VDC).
The "AUTOCOMP" function must be
activated in the ROPEX visualization
software (
ª
section 10.11 "Diagnostic interface/
visualization software (as of April 2005)" on
page 31) (default setting: AUTOCOMP off).
10.9
Temperature diagnosis
(as of April 2005)
An additional temperature diagnosis can be activated in
the ROPEX visualization software (
ª
"Diagnostic interface/visualization software (as of April
2005)" on page 31). The RES-407 checks whether the
ACTUAL temperature is within a settable tolerance
band ("OK" window) on either side of the SET
temperature. The lower (
) and upper
(
) tolerance band limits are configured in the
factory to -10K and +10K. These values can be set
independently of one another in the ROPEX
visualization software.
If the actual temperature is inside the specified
tolerance band when the "START" signal is activated,
the temperature diagnosis is activated as well. If the
ACTUAL temperature leaves the tolerance band, the
corresponding error code (307 or 308) is indicated and
the alarm output is switched (
ª
If the temperature diagnosis is not activated by the time
the "START" signal is deactivated (i.e. if the ACTUAL
temperature does not exceed the upper or lower
tolerance band limit), the corresponding error code
(309, 310) is indicated and the alarm output is
switched.
An additional delay time (0…9.9s) can be set in the
ROPEX visualization software. The first time the lower
tolerance band limit is exceeded, the temperature
diagnosis is not activated until the parameterized delay
time has elapsed. The temperature diagnosis function
can thus be explicitly deactivated, e.g. if the
temperature drops temporarily owing to the closure of
the sealing jaws.
The values that can be set in the ROPEX
visualization software for the upper and
lower tolerance band are identical to those for the
"Temperature OK" signal (MOD 46).
Function
AUTOCAL
signal
„AC“
t
t
0
0
AUTOCAL
AUTOCOMP
lit
t
OFF
„AUTOCAL“
t
OFF
LED
lit
„OUTPUT“
LED
24VDC
!
∆ϑ
lower
∆ϑ
upper
Set
Set+
∆ϑ
lower
Set+
∆ϑ
upper
Actual value
Time
Alarm
307
!